What Is Potting Material for Electronics
What Is Potting Material for Electronics
Potting materials are liquid resins that blanket a circuit board in a protective coating, fortifying the electronic components within. From water to heat, vibrating impact and even just plain old Mother Nature herself – these devices need all the extra defense they can get! Even though it might seem like overkill, potting is an incredibly important part of keeping your circuits safe.
There are basically three types of potting stuff out there; each brings its own special perks and cons. Clear as day, you’ll get something different depending on the material you choose. In this post, we will look at various potting materials for electronics along with their advantages and disadvantages.
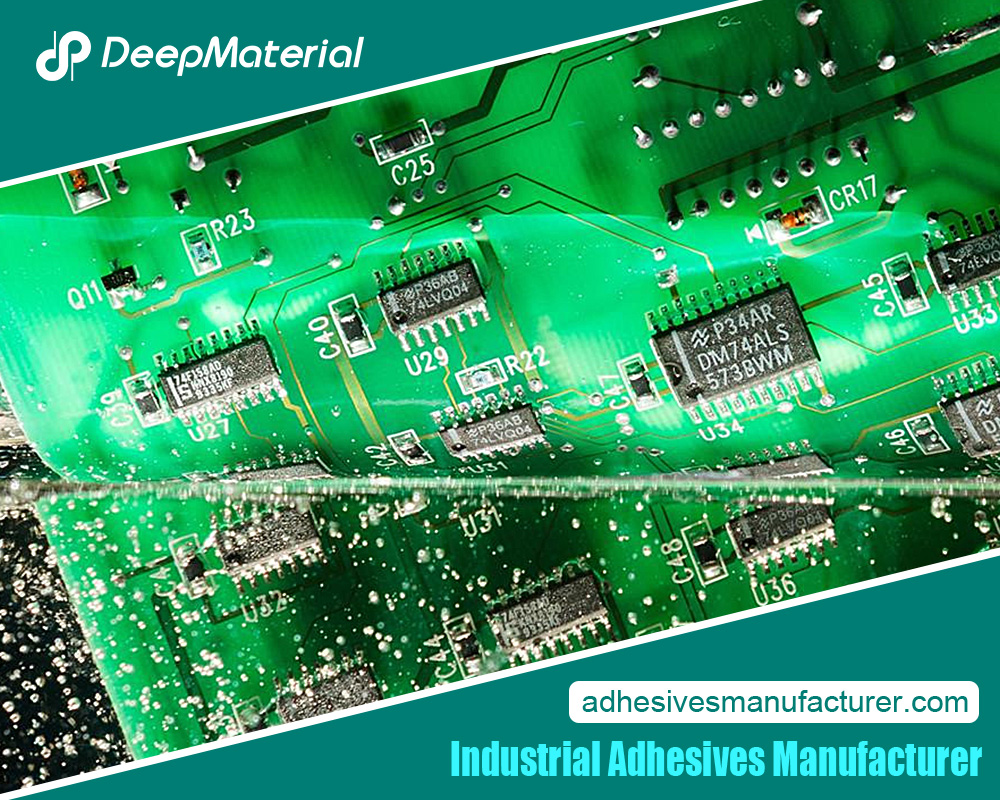
Types of Potting Materials for Electronics
Urethane and Epoxy
Potting electronics requires the best protection and fabricators know there’s no better materials for the job than epoxy and urethane. For a scorching 180°F, you’ve got urethanes taking care of your delicate components, or if extreme temperatures are to be expected – as high as 250°F – then epoxies are just what your electronics need!
Of course, it is, providing considerable safeguarding with hard-as-nails materials that won’t let you down. It simply makes sense.
Epoxy and urethane offer powerful binding capabilities, making them virtually impervious to prying eyes wishing to reincarnate existing products. In other words, these adhesives work wonders when you need to protect your ideal from others!
These materials have lots of great advantages, but there’s a dark side too. Take the potting, for instance; you can’t take it off once it sets, so if something goes wrong, your part is history – no getting around that one. It’s an incredibly frustrating position, and not much can be done about it.
Silicone
Silicone-formulated potting compounds provide an array of impressive advantages over other materials, especially epoxies and urethanes. As a result, electronics experts are turning to silicone more than ever before in order to take advantage of its unique characteristics. That’s why it keeps coming out on top for each of the following hallmark areas!
- Repairs– Removing silicone is a breeze, hard material chemistries included. So, you don’t need to worry about jeopardizing strength and stability if something is brought to your workshop – it can be fixed up!
- Temperature Resistance– the regular epoxy and urethane components used for circuit boards just can’t handle the heat, but that’s where silicone comes in handy. It has a generous temperature capacity from freezing lows of -50°F to scorching highs of 400°F, so you can count on its reliable performance no matter what kind of challenge is thrown your way.
- UV Resistance– Under sunlight, silicone-made components don’t suffer from the deteriorating effects that other materials endure – no cracking! This is due to their UV resistance, which safeguards them in this fashion. Unsurprisingly, they can be incorporated into many devices and applications where prolonged exposure to sunlight isn’t off the cards.
- Color Temperature– This refers to an essential element when considering LED lighting. Still, the finish color of your product can easily be distorted or even changed entirely from the material used in setting up the hardware. So, think very carefully about what you’re going with there! By comparison, silicone is resistant to yellowing and comes in a range of optically clear solutions. Therefore, you can rest assured that the lighting will maintain its true color over time.
- Easy Assembling– Silicone potting moves with a liquid-like consistency, making it easy to seal components without all the hassles that other materials demand. This gives you an effortless edge when it comes to potting!
- No Shrinkage– Epoxy and urethane are notorious for shrinking when they set. On the other hand, silicone, being far less temperamental, is virtually shrinkage-free when it cures, so no extra steps are needed! This means you just got yourself a time-saver there.
- Health –With the kind of potting materials used, the safety and well-being of those who handle them are at stake! Silicone is far more secure for those using it, so engineers are utilizing this material when they need to sidestep any issues with labor compliance. If health and safety are of major importance – which they often are! – then having a product that maximizes worker-friendliness is a top priority. That’s why silicone turns up in tons of medical devices out there; the benefits can’t be ignored.
- Adhesion– Working with silicone has one downside: some types of encapsulants need a primer for sticking – which epoxy and urethane don’t require. That being said, this can also be a plus sometimes since lighter adhesion allows you to fix up your parts in ways that other compounds prevent.
Choosing The Right Potting Material for Electronics
Considering the best potting material for your application? You’ll need to take some things into account before settling on one. Consider these main characteristics you should look out for as you decide- they may tip the scales in favor of one product!
- Hardness: It’s no secret that hardness is often a deciding factor when considering different applications. While harder items provide extra protection against abrasions, environmental factors and IP intrusion, something softer can often be more conducive to repairs. Take epoxy and urethane, for example; their range of hardness ranges from 80 D on the top end to as low as 10A at the bottom – all based on their own durometer scale. But when it comes time to deal with gel silicones, we switch things up and begin evaluating penetration instead!
- Viscosity– With their low viscosity, the majority of potting compounds can flow freely and at a natural level while setting. Yet occasionally, you need more control over where the resin flows to, for which cases a higher viscosity material comes in handy!
- Thermal Conductivity– Enemy number one in high-powered electronics? It’s simple: heat. In order to give this beast the boot, selecting a proper potting solution is essential. Choose silicones if you want something extraordinary at conducting thermal energy away from the hotter components. More often than not, they do their job splendidly, but epoxy or urethane compounds can fill in as adequate subs when needed. There are even some unique mixtures with special additives to adjust conduction and tailor it towards specialized uses!
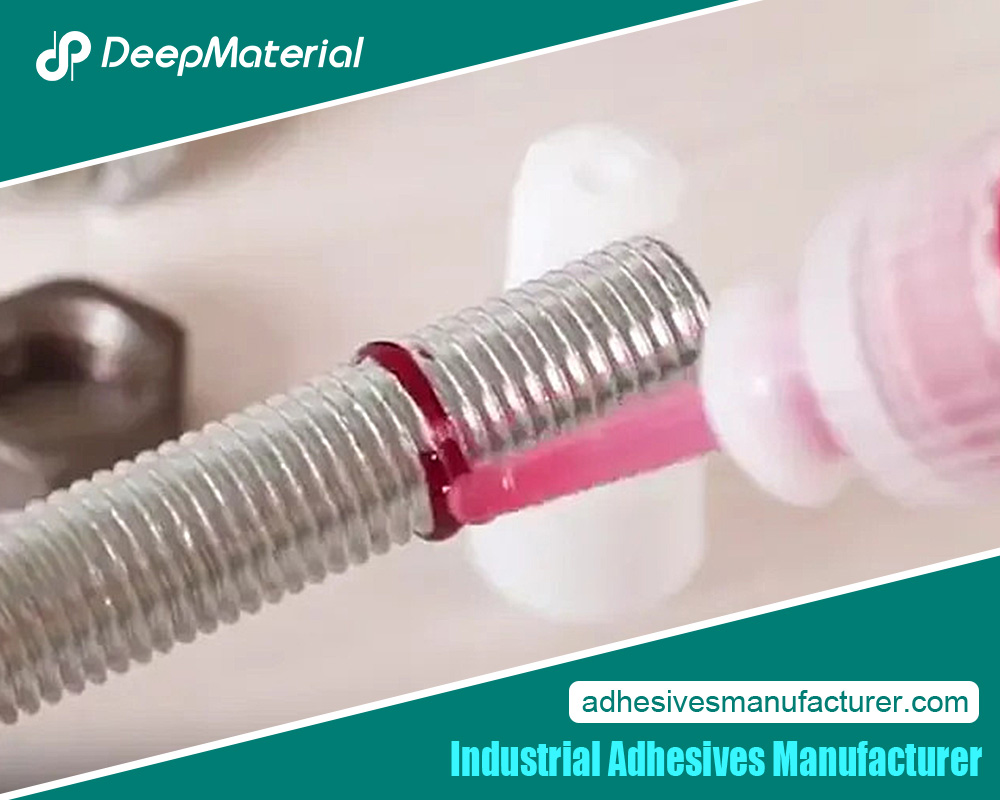
Final Thoughts
Choosing the correct potting compound can make all the difference when creating high-quality parts. Using the appropriate potting material for every application helps fabricators in many ways while getting top results. So, remember that taking these small steps towards perfection isn’t just brilliant – they’re essential.
For more about a complete guide to Potting Material for Electronics, you can pay a visit to Deepmaterial at https://www.adhesivesmanufacturer.com/ for more info.