About Industrial Adhesives
Shenzhen Deepmaterial Technologies Co., Ltd is a leading industrial adhesives technologies manufacturer with expertise to create adhesive formulations for any product or application. Deepmaterial Adhesives has the capabilities to manufacture adhesives ranging in viscosity, bond strength, application temperature, and more. Our industrial adhesives include hot melt adhesives, instant adhesives, pressure sensitive adhesives, threadlockers, structural adhesives and more, to deliver optimal performance, convenience, and reliability no matter your industry or application need.
Industrial adhesives are organic and inorganic chemical compounds that are used to join components. Products include acrylic, epoxy, hot melt, polyurethane, silicone, thermoset, and UV curing adhesives, as well as industrial sealants. Most industrial adhesives are used in fastening applications. Industrial sealants are used to fill gaps between seams, or on surfaces; and to contain fluids, prevent leaks, and prevent the infiltration of unwanted material.
From preformed adhesives, tape and labeling adhesives, packaging, automotive and electronics, or custom formulations. Industrial adhesives are used to bond various substrates via adhesion (surface bonding) and cohesion (internal strength).
If you need it, we have it. And if we don’t, we’ll create it. Yes, you can custom the adhesives what you want at Deepmaterial.
Driven by a passion to innovate, create, solve and serve, we develop and manufacture nearly any type of adhesive solution imaginable. We also utilize custom-formulated adhesives for specific materials.
Deepmaterial Adhesives, Sealants & Fillers for Electronics Technologies
Electronics innovation is anywhere in our lives. Just like drive hybrid and electric vehicles with advanced driver assistance systems, use smartphones to manage our work and play, see a new world through augmented reality (AR) headsets, enjoy personalized on-screen entertainment while flying in airplanes, and control our living space through connected home devices. But, years ago, most of these innovations were only a dream.
Deepmaterial is the premier materials manufacturer & supplier for the electronics assembly and semiconductor packaging industries. Our advanced formulations include a range of products that facilitate electrical interconnect, provide structural integrity, offer critical protection, and transfer heat for reliable performance. We’re proud to create more products that support the latest electronics technologies.
Adhesives provide a strong bond during electronics assembly while protecting components against potential damage.
Recent innovations in the electronics industry, such as hybrid vehicles, mobile electronic devices, medical applications, digital cameras, computers, defense telecommunications, and augmented reality headsets, touch nearly every part of our lives. Electronics adhesives are a crucial part of assembling these components, with a range of different adhesive technologies available to address specific application needs.
Adhesives provide a strong bond while protecting components against the damaging effects of excessive vibration, heat, moisture, corrosion, mechanical shock, and extreme environmental conditions. They also offer thermal and electrically conductive properties, as well as UV curing abilities.
Designed to meet today’s demands for strength, durability and versatility
Increasing mass production and miniaturization of electronic devices calls for faster, stronger and more precise bonding processes to new substrates. At Bostik, we understand the challenge this brings when it comes to addressing:
*Precise application needs
*Design requirements
*Aesthetic demands
Today, engineering adhesives are the primary solution for assembling electric vehicles, smartphones, medical and other electronic devices.
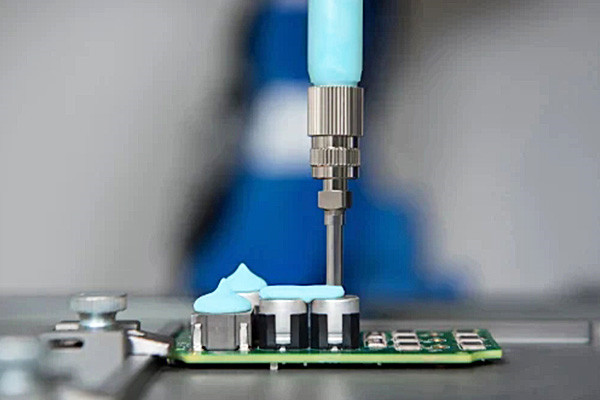
Deepmaterial Electronic Grade Systems Feature Exceptional Performance Properties
Products are easy to apply and available for use in convenient applicators (including premixed and frozen syringes for two component epoxy systems). Properties of specific grades include:
*High bond strength to similar and dissimilar substrates
*Low stress
*High/low temperature serviceability
*Fast cures
*Resistance to water and many chemicals
*Low coefficient of thermal expansion
Silicone Systems Offer Excellent Protection from Mechanical Stress and Temperature Fluctuations
One and two component electronics grade possess high thermal stability, low moduli of elasticity, superior dielectric properties. Other beneficial characteristics of select silicone compounds are as follows:
*Low shrinkage
*Thermal and electrical conductivity
*Low outgassing
*Chemical inertness
*Low moisture absorption
*Vibration damping
No mix UV/visible LIght Curing Compounds for Protection of Electronic Parts
Rapid curing single part solvent free products feature superior bond strength, environmental resistance for electronic assembly applications. Low viscosity compounds for conformal coating and higher viscosity compounds for glob top applications are engineered to resist abrasion, moisture, vibration and thermal cycling exposure.
Light-curing adhesives, coatings and encapsulants are being used in the electronics manufacturing industry with increasing frequency because they meet the requirements for materials and processing within this industry. Those factors include environmental demands (environmentallydamaging solvents and additives are not required), manufacturing-yield improvement and product cost. Light-curing adhesives are simple to use, and are quickly cured without the need for elevated temperature curing.
The adhesives are normally acrylic-based formulations and contain photo-initiators which, when activated by ultraviolet radiation, form free radicals to initiate the polymer-forming (curing) process. Ultraviolet light must be able to penetrate into the uncured resin – a drawback of lightcuring adhesives. Deposits of resin that are dark-coloured, inaccessible or very thick are difficult to cure.
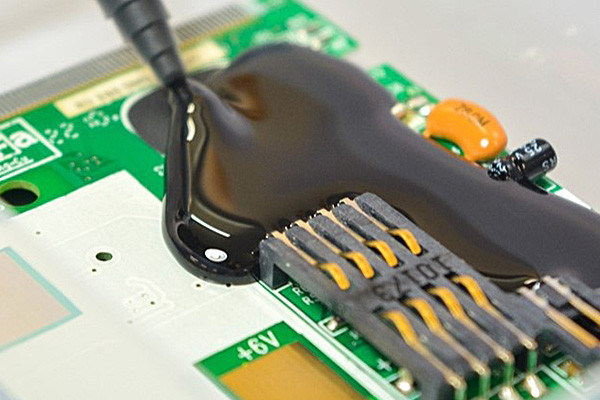
Potting and encapsulation
Potting is a method of filling small spaces or surfaces with a material that will protect components from physical and environmental damage. Potting components also provides additional insulation capability.
Potting compounds usually exhibit good chemical properties and high adhesion to plastics and metals, these being the materials of construction of the containers and also of the components.
Typical resins used for potting are epoxies, polyurethanes, silicones and acrylics, the latter usually being UV-curing formulations.
In addition to potting, there are other methods of encapsulating electronic components, namely casting and moulding. Casting uses the same type of adhesive resins as potting, although the container (outer casing) is usually removed after the resin has cured, unlike the potting process where the container becomes an integral part of the component. Moulding usually involves the injection of pre-melted thermoplastic resins into a mould containing the electronic components or circuitry.
Electrically conductive adhesives
By their nature, most adhesives, both organic and inorganic, are not electrically conductive. This applies to the main types used in electronic applications such as epoxies, acrylics, cyanoacrylates, silicones, urethane acrylates and cyanoacrylates. However, in many applications, including integrated circuits and surface-mount devices, electrically conductive adhesives are required.
The usual way of converting non-conductive adhesives to electrically conductive materials is to add suitable filler to the base material; usually the latter is an epoxy resin. Typical fillers used to confer electrical conductivity are silver, nickel and carbon. Silver is the most widely used. The conductive adhesives themselves are either in a liquid or pre-form (reinforced adhesive films die-cut before bonding to the shape required).
Thermally conductive adhesives
Miniaturisation of electronic circuitry may result in problems of heat build-up, which can cause premature failure of electronic components if their maximum operating temperature is exceeded. Thermally conductive adhesive can be used to provide a heat-conducting path, fastening transistors, diodes or other power devices to suitable heat sinks to ensure such a heat build-up does not occur.
Metallic (electrically conductive) or non-metallic (insulating) powders are blended into the adhesive formulation to make high-viscosity (paste) adhesives, which are highly thermally conductive (in comparison with unfilled adhesives). The most common thermally conductive systems are formulated with epoxy, silicone and acrylics.
From specialty wire-coating and coil encapsulation to audio component assembly and mounting, Deepmaterial offers a variety of high performance adhesive products for electronics applications in the assembly market.