Industrial Epoxy Coating
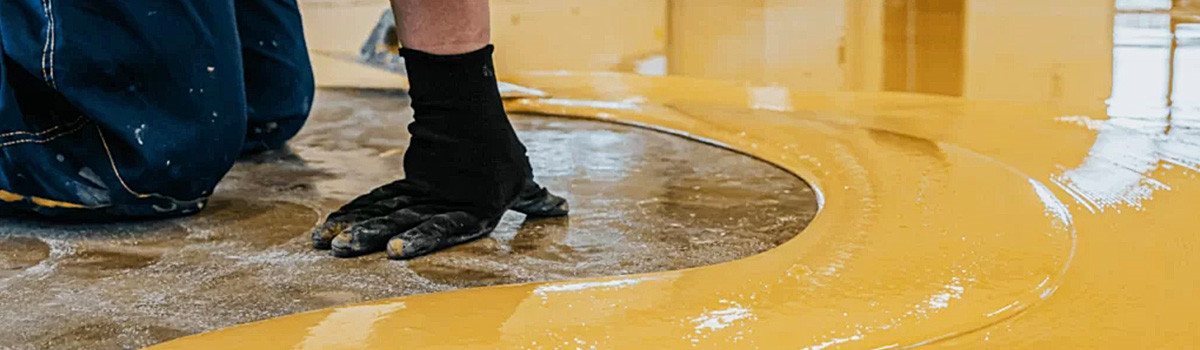
In the realm of protective coatings, industrial epoxy coatings have emerged as a versatile and indispensable solution. These coatings offer an array of benefits and find applications across various industries. From enhancing durability to providing corrosion resistance, industrial epoxy coatings have revolutionized the way surfaces are protected and preserved. In this comprehensive article, we will delve into the diverse applications and advantages of industrial epoxy coatings, shedding light on their importance in modern manufacturing and construction.
Understanding Industrial Epoxy Coatings
Industrial epoxy coatings are pivotal in safeguarding surfaces against environmental and operational challenges. With their exceptional durability, adhesion, and chemical resistance, epoxy coatings have become a staple in industries ranging from manufacturing and automotive to aerospace and construction. To truly comprehend their significance and application, one must delve into industrial epoxy coatings’ key attributes, benefits, and application considerations.
Key Attributes of Industrial Epoxy Coatings
- Chemical Resistance:Industrial epoxy coatings exhibit remarkable resistance to chemicals, acids, solvents, and various corrosive substances. These products are perfect for settings where there is frequent exposure to chemicals.
- Durability and Wear Resistance:Epoxy coatings offer exceptional durability, with the ability to withstand heavy foot traffic, machinery movement, and impacts. Their wear-resistant nature ensures prolonged surface life.
- Adhesion:Epoxy coatings form strong bonds with various substrates, including concrete, metal, and wood, enhancing their longevity and stability.
- Versatility:These coatings are adaptable to various surfaces and can be customized with additives to meet specific requirements such as slip resistance or UV stability.
Benefits of Industrial Epoxy Coatings
- Protection:Epoxy coatings act as a protective barrier, shielding surfaces from corrosion, abrasion, moisture infiltration, and chemical damage.
- Easy Maintenance:Their seamless and non-porous nature simplifies cleaning and maintenance, reducing downtime and operational costs.
- Aesthetic Enhancement:Epoxy coatings are available in various colors, finishes, and designs, contributing to an appealing and professional appearance.
- Safety Improvement:Certain epoxy formulations can include additives that enhance traction, reducing the risk of slips and falls in industrial settings.
Application Considerations
- Surface Preparation:Ensuring optimal adhesion of the epoxy coating requires proper surface preparation, which includes cleaning, repairing cracks, and removing contaminants.
- Environmental Factors:Temperature, humidity, and substrate type influence the epoxy curing. Adhering to recommended application conditions is vital.
- Coating Thickness:The required coating thickness varies based on the intended use and the substrate’s condition. Applying the right consistency ensures optimal performance.
- Professional Application:Industrial epoxy coatings demand skillful application techniques. Hiring experienced professionals guarantees a uniform and well-bonded coating.
Chemistry Behind Epoxy Coatings
Industrial epoxy coatings owe their remarkable performance and versatility to a complex chemical composition and reaction process. Understanding the chemistry behind these coatings sheds light on their adhesive strength, durability, and resistance to various environmental factors.
Epoxy Resin and Hardener Reaction
- Epoxy coatings consist of two primary components: epoxy resin and a hardener.
- Epoxy resin, derived from bisphenol-A or bisphenol-F, is a thermosetting polymer containing epoxide groups (oxirane rings).
- The hardener, often a polyamine or polyamide compound, contains amine groups that react with the epoxide groups in the resin through a cross-linking process.
- This chemical reaction, called curing or polymerization, produces a three-dimensional network of interconnected polymer chains.
Cross-Linking and Polymerization
- Cross-linking creates a solid and rigid molecular structure contributing to the coating’s durability and mechanical properties.
- The extent of cross-linking affects the coating’s final characteristics, including hardness, flexibility, and chemical resistance.
- You can tailor the curing reaction to achieve specific properties by adjusting the resin-to-hardener ratio and selecting the appropriate hardener type.
Mechanical and Chemical Properties
- The cross-linked epoxy network imparts high tensile strength, impact resistance, and load-bearing capacity to the coating.
- The non-porous nature of the cured epoxy helps prevent moisture penetration, enhancing resistance to corrosion and chemical damage.
Coating Thickness and Adhesion
- Achieving proper adhesion relies on the penetration of the epoxy into the substrate’s surface pores.
- An ideal surface profile, achieved through cleaning and preparation, ensures optimal mechanical interlocking between the epoxy and the substrate.
- Coating thickness influences performance, as an adequate thickness protects against environmental factors.
Environmental Factors and Curing
- Temperature and humidity influence the epoxy curing process.
- Some epoxy formulations require specific temperature ranges for curing to ensure complete cross-linking and optimal mechanical properties.
- Low temperatures can slow curing, while high temperatures might lead to a rapid exothermic reaction.
Exceptional Adhesion Properties
Industrial epoxy coatings have garnered significant attention for their outstanding performance in protecting and enhancing various surfaces. One of the key factors contributing to their effectiveness is their exceptional adhesion properties. These coatings adhere tenaciously to substrates, creating a strong bond that withstands harsh environments and provides long-lasting protection.
Several factors contribute to the exceptional adhesion properties of industrial epoxy coatings:
- Surface Preparation: Proper surface preparation, including cleaning, degreasing, and abrasion, significantly enhances adhesion by creating a clean and rough texture for the epoxy to bond to.
- Chemical Composition:Epoxy coatings are formulated with reactive resins that chemically bond with substrates, promoting strong adhesion.
- Cross-linking:The curing process of epoxy coatings involves cross-linking, forming a dense network that adheres tightly to the substrate.
- Wetting Ability:Epoxy coatings possess excellent wetting ability, allowing them to spread and conform to the substrate’s contours, increasing the contact area and adhesion.
Benefits of Exceptional Adhesion
The remarkable adhesion properties of industrial epoxy coatings offer a range of benefits:
- Corrosion Protection:The strong bond prevents moisture and corrosive substances from reaching the substrate, safeguarding it against corrosion.
- Abrasion Resistance:Epoxy coatings adhere tightly to surfaces, enhancing their resistance to abrasion and wear caused by friction or impact.
- Chemical Resistance:The chemical bonding between the epoxy and the substrate results in resistance to various chemicals, making epoxy-coated surfaces suitable for diverse industrial settings.
- Temperature Extremes:Epoxy coatings maintain their adhesion even in extreme temperatures, ensuring reliable performance in hot and cold conditions.
- Durability and Longevity:Due to their exceptional adhesion, epoxy coatings exhibit exceptional durability, extending the lifespan of coated surfaces.
Applications
The outstanding adhesion properties of industrial epoxy coatings find applications across various industries:
- Flooring:Epoxy-coated industrial floors benefit from improved adhesion, providing a seamless, durable, and hygienic surface suitable for factories, warehouses, and healthcare facilities.
- Pipelines and Tanks:Epoxy coatings adhere effectively to pipelines and tanks, protecting them from corrosion, chemicals, and weathering.
- Marine Environments:Epoxy coatings are widely used in marine applications, adhering well to ship decks, hulls, and offshore structures.
- Automotive:Epoxy-coated automotive parts benefit from enhanced adhesion, ensuring protection against road debris, chemicals, and weather.
Corrosion Mitigation with Epoxy Coatings
Industrial epoxy coatings are a potent defense against corrosion, a pervasive and costly issue affecting various materials and industries. Understanding how epoxy coatings mitigate pollution involves exploring their mechanisms, advantages, and application methods.
Mechanisms of Corrosion Mitigation
- Barrier Protection:Epoxy coatings form a physical barrier that shields the substrate from direct contact with corrosive agents, such as moisture, chemicals, and salts.
- Electrochemical Inhibition:Formulators can include corrosion inhibitors in epoxy coatings to hinder the electrochemical reactions that drive corrosion processes.
- Cathodic Protection:Some epoxy coatings contain conductive additives that facilitate cathodic protection, where the layer acts as a sacrificial anode to protect the underlying substrate.
Advantages of Epoxy Coatings in Corrosion Mitigation
- Longevity:Epoxy coatings are renowned for their durability, maintaining their protective integrity over extended periods, thus preventing corrosion initiation.
- Adhesion:Their strong bond with various substrates ensures a reliable and uniform protective layer that resists peeling or detachment.
- Chemical Resistance:Epoxy coatings effectively guard against various corrosive chemicals, acids, and environmental elements.
- Flexibility and Toughness:Some epoxy formulations offer flexibility, allowing them to withstand substrate movement without cracking or compromising the barrier.
- Seamless Application:The ability to coat intricate shapes, edges, and crevices without seams or gaps enhances their effectiveness in preventing corrosion.
Application Methods for Corrosion Mitigation
- Surface Preparation:Thoroughly cleaning, removing rust or contaminants, and profiling the substrate surface enhance coating adhesion and performance.
- Primer Coats:A primer enhances adhesion and corrosion resistance by creating a solid foundation for the epoxy coating.
- Layer Thickness:Achieving the recommended coating thickness ensures adequate protection against corrosion.
- Environmental Considerations:Factors like temperature, humidity, and substrate condition influence the curing and performance of epoxy coatings.
Industries and Applications
- Marine:Epoxy coatings shield ships, offshore platforms, and marine structures from saltwater corrosion.
- Infrastructure:Bridges, pipelines, and storage tanks benefit from epoxy coatings to extend their lifespan.
- Automotive: Epoxy coatings protect vehicle undercarriages and chassis from road salt and moisture-induced corrosion.
- Oil and Gas:Epoxy coatings guard pipelines and equipment against harsh oil and gas production conditions.
Enhancing Structural Longevity
Industrial epoxy coatings play a pivotal role in extending the structural longevity of various surfaces by providing a robust barrier against many environmental and operational challenges. Their unique properties reinforce feelings, prevent deterioration, and ensure lasting integrity.
1.Corrosion Resistance:Epoxy coatings excel in protecting surfaces from corrosion caused by exposure to moisture, chemicals, and harsh elements. By forming a durable barrier, they prevent the underlying material from weakening due to rust and corrosion.
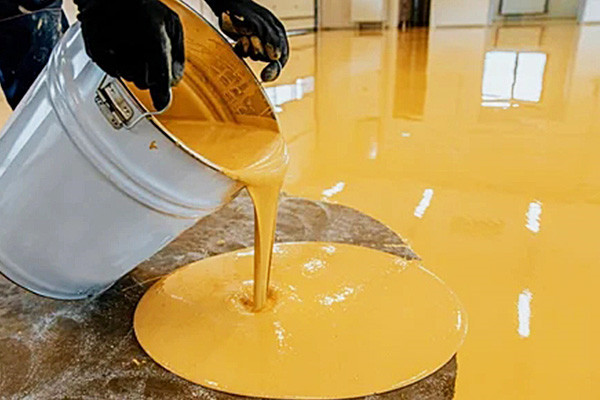
2.Weathering Protection:Harsh weather conditions, such as UV radiation, extreme temperatures, and rainfall, often affect industrial structures. Epoxy coatings act as a shield, deflecting the damaging effects of weathering and preserving the structural integrity.
3.Chemical and Abrasion Resistance:Epoxy coatings highly resist chemicals, acids, alkalis, and solvents, safeguarding surfaces from chemical degradation. Additionally, their abrasion-resistant properties counteract wear and tear caused by mechanical forces, prolonging the lifespan of the coated surfaces.
4.Enhanced Durability:By adhering firmly to substrates and forming a resilient layer, epoxy coatings improve the overall durability of surfaces. This characteristic is especially advantageous for structures subjected to significant loads, impacts, and repeated stresses.
5.Seamless Protection:Epoxy coatings provide a seamless and impenetrable barrier that prevents moisture infiltration and the potential for microcracks, ensuring that no weak points are vulnerable to structural compromise.
6.Adaptability to Diverse Substrates:Whether applied to concrete, metal, wood, or other materials, epoxy coatings demonstrate remarkable adhesion and compatibility with various substrates, making them a versatile choice for multiple applications.
7.Long-Term Cost Savings:Investing in epoxy coatings proves cost-effective in the long run. By significantly reducing the need for frequent repairs and replacements, these coatings minimize maintenance expenses and extend the operational lifespan of structures.
The utilization of industrial epoxy coatings for enhancing structural longevity finds applications in diverse industries:
- Infrastructure:Bridges, highways, and tunnels benefit from epoxy coatings that resist the corrosive effects of de-icing salts and heavy traffic loads.
- Industrial Facilities:Manufacturing plants, warehouses, and chemical processing units rely on epoxy coatings to protect surfaces against chemical spills, abrasions, and mechanical stress.
- Marine and Offshore:Epoxy coatings are essential for maritime structures, protecting them from saltwater, marine organisms, and the challenges of the marine environment.
- Commercial and Residential:Epoxy-coated floors, walls, and roofs in commercial and residential buildings ensure prolonged protection and aesthetics.
Industrial Flooring Solutions
In industrial environments where durability, safety, and performance are paramount, industrial flooring solutions, particularly those involving epoxy coatings, play a pivotal role. Understanding these flooring solutions’ essential features, benefits, and application considerations provides insights into their significance across various sectors.
Key Features of Industrial Flooring Solutions
- Durability:Designers create industrial flooring solutions to withstand heavy foot traffic, machinery movement, and various operational stresses, ensuring prolonged service life.
- Chemical Resistance:These solutions exhibit exceptional resistance to chemicals, oils, solvents, and corrosive substances, making them ideal for industries where chemical exposure is common.
- Anti-Slip Properties:Some formulations can incorporate additives to enhance traction and prevent slips and falls in high-risk environments.
- Seamless and Hygienic: Industrial flooring solutions, especially epoxy coatings, offer a seamless and non-porous surface, simplifying cleaning and maintenance and promoting hygienic conditions.
Benefits of Industrial Flooring Solutions
- Safety Enhancement:Slip-resistant surfaces and designated walkways contribute to a safer work environment, reducing the risk of accidents.
- Enhanced Durability:These solutions extend the lifespan of flooring by protecting against wear and tear, impacts, and chemical damage.
- Easy Maintenance:Seamless and non-porous surfaces are easy to clean, minimizing downtime and maintenance costs.
- Aesthetic Appeal:Industrial flooring solutions can be customized with various colors, designs, and finishes, enhancing the overall aesthetic of the workspace.
Application Considerations
- Surface Preparation:To ensure proper adhesion of the flooring solution, adequate surface preparation is crucial, including cleaning, repairing cracks, and removing contaminants.
- Environmental Factors: Temperature, humidity, and substrate type can influence the application and curing. Adhering to recommended conditions is essential.
- Coating Thickness:The required thickness varies based on the intended use and the substrate’s condition. Optimal thickness ensures adequate protection.
- Professional Application:Skillful application techniques are essential for uniform coverage and proper adhesion. Professional installation ensures optimal performance.
Industries and Applications
- Manufacturing:Epoxy-coated floors withstand heavy machinery and chemical exposure.
- Warehousing and Logistics:Durable floors handle forklift traffic and the movement of heavy goods.
- Food and Beverage:Hygienic and easy-to-clean surfaces comply with strict sanitation standards.
- Automotive:Resistant to oil, grease, and automotive fluids, providing a clean and safe environment.
Epoxy Coatings for Manufacturing Equipment
Manufacturing equipment forms the backbone of industrial operations, and ensuring its longevity and optimal performance is paramount. Epoxy coatings have emerged as a game-changer in this realm, offering a range of benefits that contribute to the reliability and efficiency of manufacturing processes.
Protection Against Corrosion and Chemicals
Epoxy coatings provide a robust barrier against corrosion, shielding manufacturing equipment from the corrosive effects of chemicals, moisture, and harsh environments. This protection is particularly vital in industries where corrosive substances are prevalent. The chemical resistance of epoxy coatings ensures that equipment remains functional and durable over extended periods.
Abrasion Resistance for Heavy-Duty Operations
Manufacturing equipment often undergoes heavy-duty usage, leading to wear and tear caused by abrasion. Epoxy coatings, with their exceptional abrasion resistance, act as a shield against the mechanical forces generated during manufacturing processes. This resistance enhances the equipment’s longevity, reducing the need for frequent replacements and repairs.
Seamless and Hygienic Surfaces
When applied to manufacturing equipment, epoxy coatings provide a seamless and smooth surface finish. This quality is invaluable in industries where hygiene and cleanliness are essential, such as food processing or pharmaceutical manufacturing. The seamless surface prevents the accumulation of dirt, grime, and contaminants, making cleaning and maintenance more efficient.
Thermal Stability for Varied Conditions
Manufacturing processes can subject equipment to a wide range of temperatures. Epoxy coatings offer excellent thermal stability, ensuring the coated equipment can withstand high and low-temperature extremes without compromising their structural integrity. This property is particularly advantageous in industries where temperature variations are commonplace.
Customization and Aesthetics
You can tailor epoxy coatings to meet specific requirements, including color coding, safety markings, and logos. This customization enhances the aesthetics of manufacturing equipment but also aids in organizing the workspace, optimizing workflows, and ensuring safety compliance.
Protective Epoxy Coatings in Construction
In construction, protective epoxy coatings have emerged as a pivotal technology, contributing significantly to the longevity and safety of various structures. These industrial epoxy coatings offer a robust shield against environmental stresses, chemical corrosion, and mechanical abrasion, extending the service life of buildings, bridges, and other infrastructure elements.
Key Benefits and Applications
- Durability Amplification:Protective epoxy coatings act as a formidable barrier against moisture infiltration, preventing the onset of rust and corrosion. This quality is especially crucial in environments exposed to harsh weather conditions, saline air, or chemical pollutants.
- Structural Reinforcement:By forming a seamless and durable layer over substrates, epoxy coatings enhance the structural integrity of concrete, steel, and other materials. This reinforcement is particularly valuable in high-traffic areas, such as industrial floors and parking garages.
- Chemical Resistance:Epoxy coatings possess remarkable resistance to a broad spectrum of chemicals, including acids, solvents, and alkalis. This feature makes them indispensable in industrial settings, where exposure to corrosive substances is commonplace.
- Aesthetic Enhancement:Beyond protection, epoxy coatings contribute to aesthetics. They are available in various colors and finishes, allowing architects and designers to incorporate functionality and visual appeal into their projects.
Application Process and Techniques
- Surface Preparation:Proper surface preparation is crucial for successful epoxy coating adhesion. Techniques like shot blasting, diamond grinding, or acid etching ensure a clean and rough surface, facilitating strong bonding.
- Primer Application:A suitable primer enhances adhesion and prevents potential chemical reactions between the substrate and the epoxy coating. Epoxy primers also help in achieving a uniform and flawless final finish.
- Epoxy Coating Application:You can apply epoxy coatings using various methods, including a brush, roller, or spray. Achieving the desired thickness and protection level might require applying multiple coats.
- Curing and Maintenance:Curing time is vital for epoxy to harden and achieve optimal properties. Regular maintenance, such as cleaning and periodic reapplication, ensures the longevity of the protective coating.
Aesthetic Enhancements and Customization
Industrial epoxy coatings have transcended their utilitarian roles to become a creative medium for elevating the aesthetics of various surfaces. These coatings offer a versatile canvas for customization, enabling businesses to infuse their spaces with branding, visual appeal, and unique designs that resonate with their identity.
- Vibrant Color Palette:Epoxy coatings come in diverse colors, allowing businesses to select hues that align with their branding or desired ambiance. The color options are virtually limitless, from bold and vibrant to subtle and sophisticated.
- Creative Patterns and Textures:You can manipulate epoxy coatings to create intricate patterns, textures, and visual effects. This characteristic opens the door to endless design possibilities, transforming mundane surfaces into visually captivating focal points.
Brand Identity and Visual Communication
Industrial spaces often serve as showcases of a company’s identity and values. Epoxy coatings offer a dynamic means of conveying these messages through design and aesthetics.
- Custom Logos and Branding:Epoxy coatings can incorporate custom-made logos and branding elements directly onto floors, walls, or other surfaces, reinforcing brand identity and leaving a lasting impression on visitors and clients.
- Safety Markings and Signage:Epoxy coatings can create clearly defined safety markings, directional signage, and instructional graphics, enhancing safety compliance and facilitating efficient traffic flow within a facility.
Tailored Solutions for Unique Spaces
Every industrial environment is distinct, and epoxy coatings offer the flexibility to cater to various spaces’ specific needs and functionalities.
- Zoning and Organization:Different zones within a facility can be restricted using contrasting epoxy colors or patterns, aiding in efficiently organizing space and equipment.
- Showroom Elegance:For automotive or luxury retail environments, epoxy coatings can replicate the luxurious appearance of high-end materials like marble or granite, elevating the showroom experience.
Durability Meets Aesthetics
While focusing on aesthetics, industrial epoxy coatings do not compromise on their inherent durability and performance characteristics.
- Long-Lasting Aesthetics:Epoxy coatings retain their vibrant colors, patterns, and textures over time, resisting fading and wear due to foot traffic or other stresses.
- Seamless Hygiene:In environments where hygiene is paramount, such as healthcare facilities or food processing plants, epoxy coatings provide a visually appealing and easy-to-clean surface, maintaining cleanliness without compromising aesthetics.
Eco-Friendly Epoxy Coating Options
As environmental concerns take center stage, the industrial sector is increasingly seeking eco-friendly alternatives, even in protective coatings. Eco-friendly epoxy coatings have emerged as a pioneering solution, offering robust protection while minimizing the environmental footprint. These coatings combine performance with sustainability, making them a viable choice for various industrial applications.
Advantages of Eco-Friendly Epoxy Coatings
- Low Volatile Organic Compounds (VOCs): Eco-friendly epoxy coatings are formulated with reduced VOC content, minimizing air pollutants and contributing to better indoor air quality in workplaces.
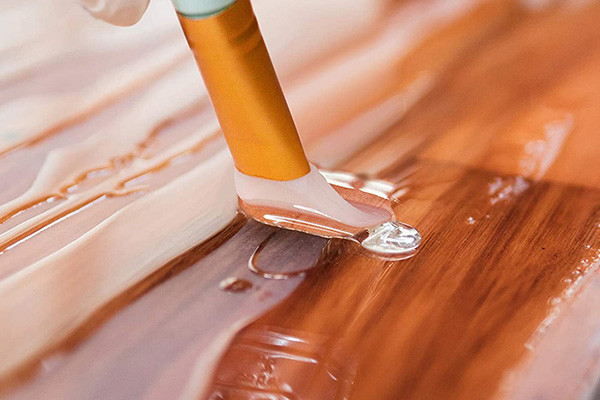
- Renewable Resources:Some eco-friendly epoxy coatings incorporate bio-based or renewable raw materials, reducing dependency on fossil fuels and depletable resources.
- Reduced Hazardous Chemicals:These coatings are formulated without hazardous solvents or chemicals, making them safer for workers and the environment.
- Energy Efficiency:Certain formulations of eco-friendly epoxy coatings require lower curing temperatures, leading to energy savings during application.
- Biodegradability:Bio-based epoxy coatings often exhibit biodegradable properties, reducing long-term environmental impact and facilitating disposal.
Innovative Eco-Friendly Formulations
- Water-Based Epoxy Coatings:These coatings replace traditional solvent-based systems with water as a carrier, resulting in lower VOC emissions and safer application.
- Plant-Based Epoxy Resins:These coatings, formulated using plant-derived resins, minimize the use of petrochemicals and offer a sustainable alternative to conventional epoxy options.
- High-Solid Epoxy Coatings:These coatings have a higher solid and lower solvent content, reducing emissions and waste during application.
- UV-Curable Epoxy Coatings:UV-curable formulations eliminate the need for traditional curing processes, reducing energy consumption and enabling quicker cure times.
- Recyclable Coating Systems:Some eco-friendly epoxy coatings undergo design to facilitate recycling and waste reduction by allowing easy stripping from substrates.
Application and Considerations
- Proper Surface Preparation:Like traditional coatings, eco-friendly epoxy coatings require adequate surface preparation for optimal adhesion and performance.
- Compatibility and Performance:Selecting the proper eco-friendly formulation depends on the specific application requirements, such as chemical resistance, durability, and mechanical strength.
- Long-Term Benefits:While eco-friendly epoxy coatings might entail slightly higher upfront costs, the long-term benefits, including reduced environmental impact and potential cost savings, make them a prudent investment.
Epoxy Coatings in Marine Industry
The marine industry relies heavily on the durability and protection of materials exposed to the relentless challenges of salt water, humidity, and harsh environmental conditions. Epoxy coatings have emerged as a transformative solution, offering a comprehensive range of benefits that redefine how the marine industry approaches corrosion prevention, aesthetics, and maintenance.
- Corrosion Resistance:Epoxy coatings provide an impenetrable barrier against the corrosive effects of saltwater, protecting ship hulls, decks, and structures from deterioration caused by exposure to marine environments.
- Anti-Fouling Properties:Some epoxy coatings can be formulated with anti-fouling additives, deterring the growth of marine organisms on submerged surfaces. This process reduces maintenance efforts and improves vessel fuel efficiency by maintaining a smooth surface.
- Durability in Harsh Conditions:Epoxy coatings exhibit exceptional resistance to UV radiation, extreme temperatures, and mechanical stress, ensuring that marine structures maintain their integrity under diverse and challenging conditions.
- Enhanced Aesthetics:Epoxy coatings offer the opportunity to improve the visual appeal of marine vessels. With various colors and finishes, ships and yachts can be transformed into eye-catching containers while maintaining protection.
- Extended Maintenance Intervals:The long-lasting durability of epoxy coatings minimizes the need for frequent repainting and maintenance, reducing downtime and associated costs.
- Compatibility with Various Substrates:Epoxy coatings adhere effectively to various materials used in the marine industry, including steel, aluminum, fiberglass, and concrete, providing versatile protection and customization options.
- Protection for Offshore Structures:Epoxy coatings play a crucial role in safeguarding offshore oil platforms, wind turbines, and other marine structures against the corrosive effects of saltwater and harsh weather.
Epoxy coatings are revolutionizing the marine industry by offering unparalleled protection, longevity, and aesthetic possibilities. As vessels and structures face the relentless forces of the sea, these coatings play a crucial role in extending the lifespan of marine assets, reducing maintenance burdens, and upholding the industry’s commitment to sustainability.
Application of Epoxy Coatings in Aerospace
Epoxy coatings have emerged as a crucial component in the aerospace industry, offering a range of benefits that enhance the durability, performance, and safety of aircraft and spacecraft. These specialized coatings exhibit exceptional properties that make them an ideal choice for various aerospace applications, contributing to the longevity and efficiency of aerospace vehicles.
Corrosion Protection
- Epoxy coatings are known for their outstanding corrosion resistance, a critical concern in aerospace due to exposure to harsh environments, moisture, and chemicals.
- These coatings form a protective barrier that prevents corrosion and rust formation on metallic surfaces, extending the lifespan of aerospace components.
Abrasion Resistance
- Aerospace vehicles experience frequent friction and wear during takeoff, landing, and flight, making abrasion resistance vital.
- Epoxy coatings with high abrasion resistance safeguard surfaces against mechanical damage and maintain structural integrity, reducing maintenance needs.
Chemical Protection
- Aerospace environments can expose components to various chemicals, such as fuels, lubricants, and cleaning agents.
- Epoxy coatings offer a barrier against chemical exposure, preventing degradation and preserving the overall performance of aerospace equipment.
Heat and Fire Resistance
- Epoxy coatings exhibit remarkable resistance to high temperatures and flames, a crucial feature for aerospace applications involving engines, exhaust systems, and components subjected to extreme heat.
- These coatings act as a thermal barrier, reducing the risk of structural failure and enhancing safety.
Electrical Insulation
- In aerospace electronics and avionics systems, epoxy coatings provide electrical insulation.
- The coatings prevent short circuits and electrical malfunctions by isolating components from conductive surfaces.
Weight Savings
- Epoxy coatings are lightweight compared to traditional protective methods like metal plating, contributing to overall weight reduction in aerospace vehicles.
- Reduced weight enhances fuel efficiency, performance, and payload capacity.
Bonding and Adhesion
- Epoxy coatings offer excellent bonding and adhesion properties, enabling them to adhere firmly to various substrates, including metals, composites, and plastics.
- This feature ensures that coatings remain intact even in high-stress situations, preventing delamination and enhancing structural integrity.
Surface Smoothness
- Formulators can create epoxy coatings that provide a smooth surface finish, reducing aerodynamic drag and enhancing fuel efficiency.
- The improved flow characteristics enhance overall performance and reduce energy consumption during flight.
Epoxy-Coated Automotive Components
Epoxy-coated automotive components have ushered in a new era of innovation in the automotive industry, enhancing both the performance and longevity of vehicles. This advanced coating technology offers many advantages that are reshaping how cars are designed, manufactured, and maintained.
- Corrosion Defense:Epoxy coatings act as a robust barrier, safeguarding automotive components from the corrosive effects of road salts, moisture, and environmental elements. This protection extends the lifespan of parts and contributes to the overall durability of the vehicle.
- Enhanced Durability:Epoxy-coated components exhibit remarkable resistance to abrasion, impacts, and mechanical stress. This durability ensures that critical parts, such as suspension components and underbody panels, remain structurally sound even under challenging conditions.
- Chemical Resistance:The chemical bonding of epoxy coatings provides a protective shield for automotive components, guarding them against exposure to chemicals, oils, and fluids commonly encountered on roads. Maintaining peak performance is ensured by preventing degradation.
- Noise and Vibration Dampening:You can tailor epoxy coatings to offer noise and vibration-dampening properties, contributing to a quieter and more comfortable driving experience by reducing unwanted vibrations and sounds.
- Aesthetic Enhancement:Beyond protection, epoxy coatings offer aesthetic benefits, enabling manufacturers to customize the appearance of components. This encompassing range includes a variety of color choices, textures, and finishes that all complement the design style of the vehicle.
- Eco-Friendly Solution:Formulators can create epoxy coatings with low VOC (volatile organic compound) content, contributing to environmentally conscious manufacturing processes.
Across chassis components and exhaust systems, the automotive sector’s application of epoxy coatings has brought about a paradigm shift in vehicle construction. These coatings shield against corrosion and wear and optimize vehicle performance, reduce maintenance requirements, and provide an avenue for creative design expression. As the automotive industry continues to evolve, epoxy-coated components stand as a testament to the synergy between cutting-edge technology and the pursuit of excellence on the road.
Electrical Insulation Applications
Epoxy coatings have gained prominence for their exceptional electrical insulation properties, finding widespread application in various industries where safeguarding against electrical conductivity and preventing electrical malfunctions are crucial. These coatings offer a reliable solution to ensure the integrity and safety of electrical components and systems across diverse sectors.
Electronics and Electrical Components
- Industries extensively use epoxy coatings to insulate electronic devices and electrical components, preventing short circuits and maintaining signal integrity.
- They provide a protective layer that prevents moisture, dust, and contaminants from compromising the functionality of delicate components.
Circuit Boards and PCBs
- Epoxy coatings are applied to printed circuit boards (PCBs) to insulate and protect the delicate circuitry from environmental factors and potential electrical interference.
- These coatings enhance the durability and longevity of PCBs in various applications, from consumer electronics to industrial machinery.
Power Distribution Systems
- Industrial epoxy coatings insulate power distribution systems, including transformers, switchgear, and power cables.
- The coatings prevent leakage currents, improve dielectric strength, and reduce the risk of electrical breakdowns, enhancing the overall reliability of the power infrastructure.
Motors and Generators
- Epoxy coatings are utilized in motors and generators to isolate winding coils, reducing the risk of electrical short circuits.
- By providing a robust electrical insulation layer, these coatings contribute to the rotating machinery’s efficient and safe operation.
Aerospace and Avionics
- In the aerospace industry, epoxy coatings serve as electrical insulators for avionics systems, ensuring reliable communication and operation.
- They safeguard critical electronic components from electromagnetic interference and maintain performance in the demanding aerospace environment.
Renewable Energy Systems
- Epoxy coatings play a role in renewable energy applications, such as wind turbines and solar panels.
- They insulate components, such as windings in generators and photovoltaic cells, contributing to the efficiency and longevity of these systems.
High Voltage Equipment
- For high-voltage equipment like transformers and capacitors, epoxy coatings provide insulation that can withstand extreme electrical stress.
- These coatings minimize energy loss and maintain stable performance in high-power applications.
Protection in Harsh Environments
- Epoxy coatings offer insulation in harsh and corrosive environments, such as marine and industrial settings.
- They shield electrical components from moisture, chemicals, and temperature fluctuations, ensuring consistent performance and longevity.
Epoxy Coatings for Chemical Processing
In chemical processing, where harsh chemicals, corrosive substances, and demanding operating conditions prevail, epoxy coatings have emerged as a cornerstone for safeguarding infrastructure and ensuring operational efficiency. The unique properties of epoxy coatings make them indispensable in this sector, offering a range of benefits that address the challenges inherent to chemical processing environments.
- Corrosion Resistance:Epoxy coatings create an impenetrable barrier that shields equipment and structures from the corrosive effects of chemicals, acids, and acidic substances. This protection is paramount in preventing premature deterioration and maintaining the structural integrity of critical components.
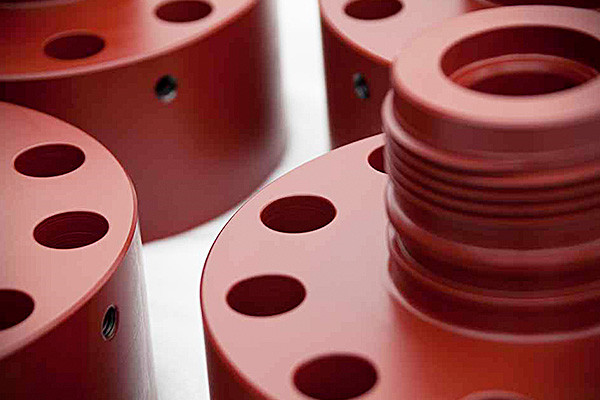
2.Chemical Immunity:Epoxy coatings exhibit high chemical resistance, withstanding exposure to a broad spectrum of corrosive substances commonly found in chemical processing plants. This quality ensures that coated surfaces remain unaffected by chemical spills and leaks.
3.Surface Hygiene:In environments where contamination can have severe consequences, epoxy coatings provide a smooth, easy-to-clean surface that minimizes the risk of cross-contamination and ensures compliance with stringent hygiene standards.
4.Thermal Stability:Epoxy coatings offer remarkable thermal resistance, enabling them to endure extreme temperatures and thermal cycling commonly experienced in chemical processing operations. This property prevents layers from deteriorating and maintains their protective qualities.
5.Longevity and Cost Savings:By effectively shielding against corrosion and chemical degradation, epoxy-coated equipment and structures require less frequent maintenance, resulting in reduced downtime and cost savings over the long term.
6.Customization for Functionality:You can tailor epoxy coatings to meet specific requirements, including creating non-slip surfaces, applying color coding for safety, and incorporating directional markings that aid in optimizing workflows and ensuring safety protocols.
Epoxy coatings play an essential role in chemical processing facilities, fortifying equipment and structures against the aggressive nature of chemical interactions. With their resistance to corrosion, chemicals, and extreme temperatures, these coatings contribute to the safety, durability, and operational continuity of facilities where the integrity of materials is paramount. In chemical processing, epoxy coatings stand as a testament to the symbiosis between cutting-edge technology and industrial necessity, ensuring that infrastructure remains robust and reliable despite harsh conditions.
Advancements in Epoxy Coating Technology
Epoxy coating technology has witnessed remarkable advancements reshaping industries and redefining protection, durability, and versatility standards. These innovations are driving the evolution of epoxy coatings from traditional solutions to cutting-edge materials that address various challenges across various sectors.
- Nanotechnology Integration:The integration of nanotechnology has led to the development of epoxy coatings with enhanced properties. Nanoparticles incorporated into layers offer improved adhesion, hardness, and chemical resistance, elevating overall performance.
- Innovative Coatings:Advancements in epoxy technology have paved the way for “smart coatings” equipped with sensors and indicators that monitor structural integrity, corrosion levels, and other crucial factors. These coatings provide real-time data for proactive maintenance.
- High-Performance Formulations:Companies have refined formulations to provide specialized coatings tailored to specific industries. High-performance epoxy coatings are designed for extreme environments, offering unparalleled resistance to abrasion, UV exposure, and chemical attacks.
- Eco-Friendly Options:With growing environmental concerns, epoxy coatings have evolved to include eco-friendly formulations with low VOC content. These coatings not only provide protection but also align with sustainable practices.
- Self-Healing Properties:Advancements have led to self-healing epoxy coatings that can repair minor damage through chemical reactions. This property extends the lifespan of coatings and reduces maintenance requirements.
- Functional Additives:Now, you can customize epoxy coatings with functional additives that impart specific properties, such as anti-slip, anti-static, flame retardant, and antimicrobial characteristics.
- Digital Design and Customization:Modern epoxy technology allows for digital design and customization, enabling businesses to incorporate intricate patterns, logos, and branding into coatings for aesthetics and functionality.
These advancements transcend traditional expectations of epoxy coatings, offering industries unparalleled tools for protection, durability, and customization. As epoxy technology continues to push boundaries, it is shaping a future where materials are not just passive but actively contribute to improved performance, sustainability, and innovation across sectors.
Surface Preparation for Epoxy Coatings
Proper surface preparation is foundational in achieving successful and long-lasting epoxy coatings in industrial settings. A well-prepared surface ensures strong adhesion, optimal performance, and durability of the epoxy coatings. The following bullet points outline key surface preparation aspects crucial for applying epoxy coatings.
Cleaning and Degreasing
- Thorough surface cleaning removes dirt, dust, grease, oil, and contaminants.
- Cleaning agents, solvents, or detergents ensure a pristine substrate for coating adhesion.
Surface Profiling
- Mechanical methods like abrasive blasting, grinding, or sanding create a suitable surface profile.
- A proper shape enhances epoxy coating adhesion by providing a roughened texture for the coating to grip onto.
Removal of Previous Coatings
- You must remove previous coatings, paints, or finishes to prevent adhesion issues.
- Techniques such as chemical stripping, scraping, or sandblasting strip old layers from the substrate.
Repairing Surface Imperfections
- You must repair substrate cracks, holes, or imperfections using suitable fillers or patching compounds.
- Smooth surfaces prevent air pockets and ensure even coating application.
Moisture and Humidity Control
- Moisture on the substrate can hinder epoxy adhesion and cause coating failures.
- Proper moisture testing and control measures, such as dehumidification, ensure a dry surface.
Testing for Contaminants
- Conduct surface testing for contaminants like oil, grease, or chemicals to ensure proper adhesion.
- Methods such as water break test or solvent wipe test identify surface contamination.
Compatibility with Substrate
- Substrate compatibility is essential to ensure the epoxy coating bonds effectively.
- Different substrates may require specific primers or pretreatment to enhance adhesion.
Masking and Protection
- Mask areas to prevent overspray or unintentional coating on surfaces.
- Proper masking ensures clean and defined coating edges.
Final Inspection
- Conduct a thorough visual inspection of the prepared surface before applying the epoxy coating.
- Address any remaining contaminants or imperfections to ensure a flawless surface.
Factors Influencing Epoxy Coating Durability
A combination of factors influences the durability of epoxy coatings, determining their ability to withstand the rigors of various environments and applications. Understanding these factors is crucial for achieving optimal performance and extending the lifespan of coated surfaces.
- Surface Preparation:Proper surface preparation is foundational to coating durability. Inadequate cleaning, rust, or contaminants can hinder adhesion, compromising the longevity of the coating.
- Coating Thickness:The thickness of the applied epoxy coating directly impacts its ability to resist wear, abrasion, and chemical exposure. Adequate thickness ensures comprehensive protection.
- Substrate Compatibility:The type of substrate plays a significant role in coating durability. Epoxy coatings must adhere well to the substrate material to maintain their protective qualities.
- Curing Conditions:Curing processes affect the formation of the epoxy’s cross-linked structure. Proper curing time, temperature, and humidity levels are essential for achieving full coating strength and durability.
- Environmental Exposure:Exposure to external factors like UV radiation, temperature fluctuations, humidity, and chemicals can degrade epoxy coatings over time. Unique formulations may be required to counter specific environmental challenges.
- Coating Formulation:The formulation of the epoxy coating, including additives and resin type, determines its resistance to chemicals, impact, and other stressors. High-quality formulations enhance durability.
- Maintenance and Cleaning:Regular maintenance and appropriate cleaning methods can significantly extend the life of epoxy coatings. Harsh cleaning agents or abrasive techniques can deteriorate coatings prematurely.
- Application Technique:Proper application techniques, including spray, brush, or roller application, ensure uniform coverage and adhesion, contributing to coating durability.
- Quality Control:Stringent quality control measures during the manufacturing and application processes help identify defects or inconsistencies that could compromise coating durability.
In industrial epoxy coatings, durability is a critical aspect that directly impacts the effectiveness and lifespan of protective coatings. By addressing factors such as surface preparation, substrate compatibility, curing conditions, and environmental exposure, industries can ensure that epoxy coatings provide reliable, long-lasting surface protection for various applications.
Quality Control and Testing of Epoxy Coatings
Ensuring the quality and reliability of epoxy coatings is vital for their successful performance in industrial settings. Rigorous quality control measures and testing protocols are essential to verify that epoxy coatings meet the desired standards and provide the expected protection and durability. The following bullet points highlight key aspects of quality control and testing for epoxy coatings.
Adhesion Testing
- Adhesion tests, such as crosshatch or pull-off tests, evaluate the bonding strength between the epoxy coating and the substrate.
- Proper adhesion ensures that the coating remains securely attached to the surface.
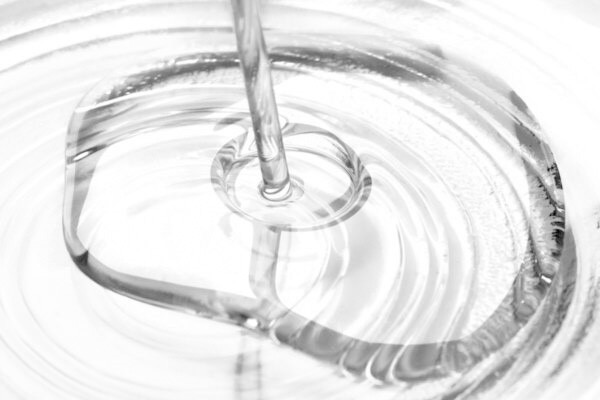
Thickness Measurement
- Monitor coating thickness using methods like magnetic induction or ultrasonic gauges.
- Correct consistency is crucial for achieving the desired protective properties and performance.
Visual Inspection
- Visual inspections identify surface irregularities, inconsistencies, and defects in the epoxy coating.
- This process ensures a uniform and defect-free coating application.
Holiday Detection
- Holiday or pinhole detection tests identify microscopic defects in the coating that could lead to corrosion.
- Techniques like high-voltage spark testing or low-voltage wet sponge testing are employed.
Salt Spray Testing
- Salt spray tests simulate corrosive environments to assess the coating’s resistance to corrosion.
- This process evaluates the protective properties of the epoxy coating over time.
Chemical Resistance Testing
- Coatings are exposed to various chemicals to determine their resistance and performance.
- Ensures the coating’s ability to withstand exposure to specific substances.
Impact Resistance Testing
- Impact tests assess the coating’s ability to resist physical impact and deformation.
- Important for coatings in high-traffic or industrial environments.
Abrasion Resistance Testing
- Abrasion tests measure the coating’s ability to withstand wear and abrasion.
- This measure ensures durability and longevity in environments prone to mechanical stress.
Heat and Temperature Resistance Testing
- Coatings are subjected to elevated temperatures to evaluate their thermal stability.
- Ensures coatings can withstand temperature fluctuations without degradation.
Flexibility and Elongation Testing
- Flexibility tests assess the coating’s ability to withstand bending and stretching without cracking.
- Important for coatings on flexible substrates or surfaces with movement.
Curing and Hardness Testing
- Curing tests verify that the epoxy coating has reached its desired hardness and durability.
- This step ensures proper curing for optimal performance.
UV Resistance Testing
- UV exposure tests evaluate the coating’s resistance to ultraviolet radiation and fading.
- Necessary for outdoor applications to prevent degradation from sunlight exposure.
Future Prospects of Industrial Epoxy Coatings
The evolution of industrial epoxy coatings continues to shape the landscape of various industries, driven by technological advances, sustainability demands, and the need for enhanced performance. As enterprises seek innovative solutions for protection, durability, and environmental considerations, epoxy coatings are poised to be pivotal in addressing emerging challenges and opportunities. The following bullet points highlight key prospects for industrial epoxy coatings.
Nanotechnology Integration
- Nanoparticles can be incorporated into epoxy coatings to enhance properties like hardness, scratch resistance, and UV protection.
- Nanotechnology offers the potential to create advanced coatings with tailored properties for specific applications.
Innovative Coatings and Sensors
- Developers could create epoxy coatings with integrated sensors to monitor corrosion, temperature, and structural integrity.
- Innovative coatings enable real-time data collection and predictive maintenance, enhancing safety and efficiency.
Self-Healing Capabilities
- Researchers are developing epoxy coatings with self-healing properties, enabling them to repair cracks and defects automatically.
- Self-healing coatings significantly extend the lifespan of coated surfaces and reduce maintenance needs.
Sustainable Formulations
- Demand for eco-friendly coatings is driving the development of epoxy formulations with reduced VOC emissions and lower environmental impact.
- Researchers are exploring biobased and recycled materials to create more sustainable epoxy coatings.
Enhanced Corrosion Resistance
- The need for adequate corrosion protection in challenging environments, such as marine and offshore, continues to drive epoxy coating research.
- Advanced formulations could offer excellent resistance to corrosive substances and harsh conditions.
High-Temperature Applications
- Researchers are developing epoxy coatings capable of withstanding higher temperatures for applications such as automotive engines and industrial equipment.
- High-temperature-resistant coatings contribute to improved efficiency and durability in extreme conditions.
Aerospace and Space Exploration
- Epoxy coatings will play a crucial role in aerospace applications, protecting against space radiation, thermal stress, and micro-meteor impacts.
- As space exploration advances, epoxy coatings will be essential for ensuring the integrity of spacecraft and equipment.
Digitalization and Automation
- Researchers use digital simulations and virtual testing to accelerate coating development and optimization.
- Automation in coating application processes ensures consistent quality and reduces human error.
Advanced Surface Functionalities
- Epoxy coatings with specialized functionalities, such as anti-fouling, anti-icing, or anti-bacterial properties, are being explored for diverse applications.
- These coatings add unique value to the marine, healthcare, and transportation industries.
Customization and Hybrid Coatings
- You can tailor epoxy coatings to meet specific requirements by combining them with other materials or additives.
- Hybrid coatings, combining epoxy with other polymers, nanoparticles, or fillers, offer a range of customizable properties.
Industrial epoxy coatings have undoubtedly transformed the landscape of surface protection and enhancement. From their exceptional adhesion properties to their remarkable resistance against corrosion and chemicals, these coatings have found their way into various sectors. Whether it’s safeguarding manufacturing equipment, enhancing aesthetics, or extending the life of structures, epoxy coatings have proven their mettle. As technology continues to evolve, we can anticipate even more innovative applications and eco-friendly formulations, ensuring that industrial epoxy coatings remain a cornerstone of modern protective solutions.