Industrial Bonding Adhesive
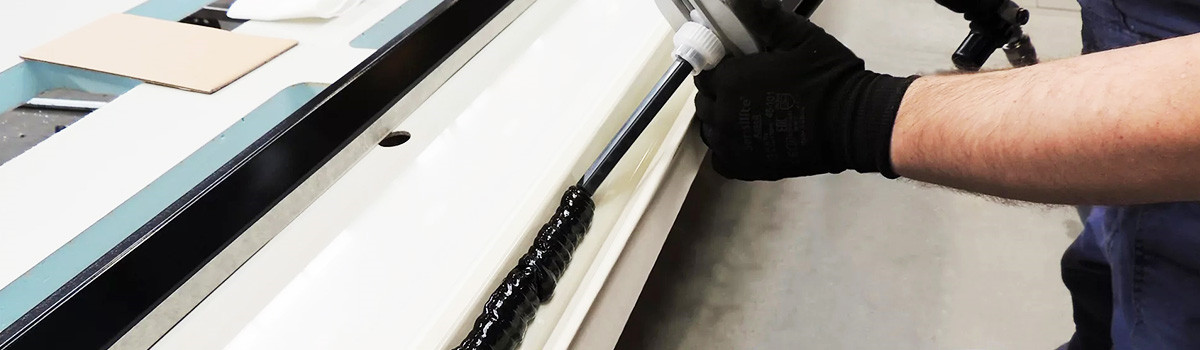
Industrial bonding adhesives play a crucial role in various industries by providing a solid and reliable means of joining materials. These adhesives have evolved significantly and become a preferred alternative to traditional mechanical fastening methods like welding, riveting, and screwing. They offer several advantages, such as distributing stress evenly across the bonded area, reducing the need for drilling or punching holes, and enabling the joining of dissimilar materials .
From humble beginnings to cutting-edge formulations, join us as we spotlight these unassuming yet indispensable agents of innovation.
Elevate Your Skills with Industrial Bonding Adhesives: The In-Depth Guide You Need
What are industrial bonding adhesives and their primary function?
Industrial bonding adhesives, also known as industrial adhesives or structural adhesives, are specialized materials used in various manufacturing and industrial processes to bond or join different substrates together. These adhesives are designed to provide strong, durable, and reliable bonds between multiple materials, including metals, plastics, composites, ceramics, and more. Their primary function is to replace or complement traditional joining methods like welding, riveting, and mechanical fasteners.
The primary functions and advantages of industrial bonding adhesives include the following:
- Strong Bonding:Industrial adhesives create robust bonds that distribute stress evenly across the bonded surfaces. This helps enhance the overall strength and structural integrity of the assembled parts.
- Uniform Stress Distribution:Adhesives distribute stress more evenly than mechanical fasteners, often creating localized stress concentrations.
- Sealing and Insulating:Adhesives can create a sealed and insulated joint, protecting the bonded components from environmental factors such as moisture, chemicals, and temperature fluctuations.
- Weight Reduction:Unlike traditional joining methods that often require additional materials (like fasteners), adhesives can lead to weight savings, which is crucial in industries where weight reduction is essential, such as aerospace and automotive.
- Improved Aesthetics:Adhesives can provide a smooth and aesthetically pleasing finish since they don’t leave visible marks or deformations on the surfaces like some traditional joining methods.
- Corrosion Resistance:Certain industrial adhesives offer resistance to corrosion, which is particularly beneficial for applications in harsh or corrosive environments.
- Vibration Damping:Adhesives can absorb and dampen vibrations and noise, improving assembled products’ overall performance and comfort.
- Design Flexibility:Adhesives enable more flexible design possibilities by allowing the bonding of dissimilar materials that may be difficult to join using traditional methods.
- Reduced Heat Distortion:In applications where heat can cause distortion or damage to the components, adhesives can provide a solution as they require lower temperatures than welding.
- Time and Labor Efficiency:Adhesive bonding often requires less time and labor than traditional methods, increasing production efficiency.
Various industrial bonding adhesives are available, each with specific properties and applications. Some common types include epoxy adhesives, polyurethane adhesives, cyanoacrylate adhesives (super glues), acrylic adhesives, and more. The choice of adhesive depends on factors such as the materials being bonded, the required bond strength, environmental conditions, and other application-specific requirements.
Overall, industrial bonding adhesives are crucial in modern manufacturing processes, creating solid and reliable bonds in various industries, from automotive and aerospace to electronics and construction.
How do industrial bonding adhesives differ from traditional joining methods?
Industrial bonding adhesives and traditional joining methods serve the same purpose of joining materials together but differ in several significant ways. Here are some critical differences between industrial bonding adhesives and traditional joining methods:
- Material Compatibility:
- Adhesives: Industrial adhesives can bond various materials, including dissimilar ones like metals, plastics, ceramics, and composites.
- Traditional methods: Welding, riveting, and soldering are often limited to specific materials or combinations, restricting design and material choices.
- Stress Distribution:
- Adhesives: Adhesive bonds distribute stress more evenly across the joint, reducing localized stress concentrations. This can be particularly advantageous for materials prone to distortion or cracking under pressure.
- Traditional methods: Traditional methods can introduce stress concentrations at the joints, potentially leading to material weakening and fatigue over time.
- Aesthetic Appearance:
- Adhesives: Adhesive joints can create a smooth, aesthetically pleasing appearance with minimal visible joint lines, making them suitable for applications where appearance matters.
- Traditional methods: Welding, riveting, and other methods often leave visible joint marks, which may require additional finishing or cover-up.
- Thermal Impact:
- Adhesives: Many industrial adhesives cure at lower temperatures than welding, which can help avoid heat-related damage to sensitive materials, electronic components, or heat-sensitive coatings.
- Traditional methods: Welding and other methods involve high heat that can alter material properties or cause distortion.
- Weight and Stress Distribution:
- Adhesives: Adhesively bonded joints tend to be lightweight, and the adhesive itself can act as a stress-distributing layer, potentially enhancing the overall structural integrity of the joint.
- Traditional methods: Traditional joining methods like welding can add weight to the joint, and the heat-affected zones can lead to localized stress concentrations.
- Vibration Damping and Noise Reduction:
- Adhesives: Adhesives can provide better vibration damping and noise reduction properties due to their viscoelastic nature, making them suitable for applications where vibration control is essential.
- Traditional methods: Due to their rigid nature, traditional joints may transmit vibrations and noise more effectively.
- Complex Geometries:
- Adhesives: Adhesives can bond complex shapes, irregular surfaces, and intricate designs that might be challenging or impossible with traditional methods.
- Traditional methods: Traditional methods often require more straightforward and standardized joint configurations.
- Labor and Equipment:
- Adhesives: Applying adhesives might require specialized equipment, but the process is generally less labor-intensive and requires less technical training than traditional methods like welding.
- Corrosion Resistance:
- Adhesives: Some adhesive formulations offer better corrosion resistance than traditional joining methods like welding, which can help extend the lifespan of the joint and the overall structure.
- Joining Speed and Efficiency:
- Adhesives: Adhesive bonding can be faster than traditional methods, especially when dealing with large surface areas or complex shapes, and may require little preparation and post-processing.
When did industrial bonding adhesives gain prominence in manufacturing processes?
Industrial bonding adhesives began to gain prominence in manufacturing processes during the mid-20th century. Advancements in polymer chemistry, materials science, and manufacturing technology drove the development and adoption of these adhesives. The transition from traditional mechanical fastening methods (such as screws, bolts, and rivets) to adhesive bonding offered several advantages, including improved aesthetics, reduced weight, better stress distribution, and enhanced overall performance of bonded materials.
One significant milestone in the rise of industrial bonding adhesives was the introduction of epoxy resins in the 1940s. Epoxy adhesives provided solid and durable bonds across various substrates and became widely used in aerospace, automotive, electronics, construction, and more industries.
Over the years, other types of adhesives, such as acrylics, cyanoacrylates (super glues), polyurethanes, and silicones, were developed and optimized for specific applications. These adhesives offered varying properties, such as fast curing, flexibility, resistance to harsh environments, and thermal stability, making them suitable for various manufacturing needs.
The 1960s and 1970s saw further advancements in adhesive technology, with manufacturers investing in research and development to create specialized formulations for specific industries. As a result, adhesives became integral to assembling products ranging from electronics and appliances to automobiles and aircraft.
Industrial bonding adhesives continue to play a crucial role in modern manufacturing processes, contributing to improved efficiency, product design, and overall quality across various industries.
Why are industrial bonding adhesives considered versatile solutions in diverse industries?
Industrial bonding adhesives are considered versatile solutions in diverse industries due to several key characteristics and advantages they offer:
- Bonding Versatility: Industrial adhesives can bond a wide range of materials, including metals, plastics, composites, ceramics, glass, and even dissimilar substrates. This versatility allows them to be used in various applications across different industries.
- Strength and Durability: Many industrial adhesives provide strong and durable bonds that withstand extreme temperatures, vibrations, impacts, and harsh environmental conditions. This is crucial in industries where reliability and longevity are essential.
- Weight Reduction: Adhesives can often replace traditional mechanical fastening methods (such as screws, rivets, or welding), reducing the need for additional components and contributing to lighter-weight designs. This is especially important in industries like aerospace and automotive, where weight savings can lead to improved fuel efficiency and performance.
- Design Flexibility: Adhesives enable more intricate and complex designs since they bond irregular or difficult-to-reach surfaces without compromising structural integrity. This is advantageous in industries like electronics and medical devices.
- Uniform Distribution of Stress: Adhesives distribute stress evenly across the bonded surfaces, reducing localized stress concentrations that can lead to material fatigue or failure. This is particularly beneficial in applications subject to dynamic loads.
- Corrosion Prevention: In industries where metal bonding is prevalent, adhesives can help prevent galvanic corrosion by acting as a barrier between dissimilar metals.
- Improved Aesthetics: Adhesive bonding often eliminates the need for visible fasteners, welds, or joints, resulting in smoother and more aesthetically pleasing surfaces. This is crucial in industries where appearance matters, such as consumer electronics and luxury goods.
- Reduced Processing Time: Adhesive bonding can be faster than traditional methods, such as welding or mechanical fastening, reducing assembly times and increasing productivity.
- Reduced Thermal Stress: Adhesives typically have lower heat input compared to welding, minimizing the risk of thermal distortion in heat-sensitive materials.
- Enhanced Sealing and Insulating Properties: Certain adhesive formulations offer sealing and insulating properties, making them valuable in applications where moisture, chemicals, or electrical isolation are concerns.
- Ease of Automation: Adhesive applications can often be automated, leading to consistent and repeatable results in high-volume production environments.
- Environmental and Safety Benefits: Adhesive bonding can eliminate the need for processes like welding that produce hazardous fumes, reducing workplace health and safety risks.
Overall, the versatility of industrial bonding adhesives lies in their ability to offer robust, reliable, and adaptable bonding solutions across a broad spectrum of industries, addressing various technical and operational requirements. This adaptability and functionality make them an essential tool in modern manufacturing and engineering.
Where are the typical applications of industrial bonding adhesives across sectors?
Industrial bonding adhesives are used across various sectors for various applications due to their ability to combine materials intensely and durably. Here are some typical applications of industrial bonding adhesives across different sectors:
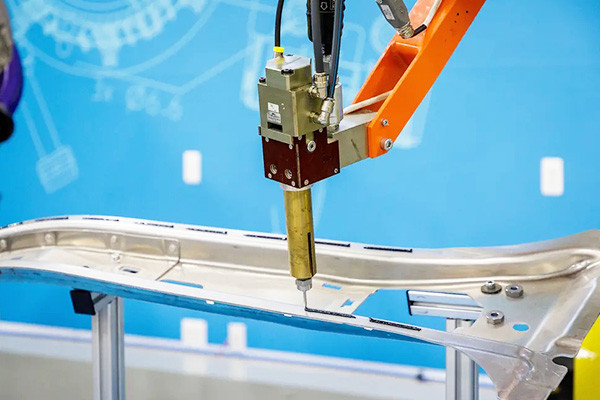
- Automotive Industry:
- Body Assembly:Adhesives are used to bond various vehicle body components, such as panels and trim.
- Structural Bonding:Adhesives can replace traditional welding and mechanical fastening in specific structural applications, reducing weight and improving design flexibility.
- Windshield Bonding:Adhesives attach windshields and rear windows, providing a solid and leak-free seal.
- Aerospace Industry:
- Composite Bonding:Adhesives are essential for bonding lightweight composite materials used in aircraft construction.
- Panel Bonding:Adhesives bond interior and exterior panels, providing a smooth surface and reducing vibration.
- Electronics Industry:
- Component Bonding:Adhesives bond components onto circuit boards, enabling compact and reliable electronic assemblies.
- Encapsulation:Adhesives seal and protect delicate electronic components from moisture, dust, and mechanical stress.
- Construction Industry:
- Facade Bonding:Adhesives are used for attaching facade panels, providing an aesthetically pleasing appearance and thermal insulation.
- Flooring Installation:Adhesives are used to bond various types of flooring materials, such as tiles, carpet, and wood.
- Medical Device Industry:
- Medical Device Assembly:Adhesives bond components of medical devices, ensuring biocompatibility and reliability.
- Wound Closure:Medical-grade adhesives are used instead of traditional sutures for specific wound closures.
- Packaging Industry:
- Sealing and Closure:Adhesives seal boxes, cartons, and packages, ensuring product integrity during shipping and storage.
- Label and Tape Application:Adhesives apply labels, tapes, and decals to products and packaging.
- Renewable Energy Industry:
- Solar Panel Manufacturing:Adhesives bond various layers of solar panels, ensuring durability and efficiency.
- Wind Turbine Blade Bonding:Adhesives are used to construct wind turbine blades to bond composite materials.
- Furniture Industry:
- Furniture Assembly:Adhesives bond wood, laminate, and other materials in furniture manufacturing.
- Upholstery Bonding:Adhesives attach fabric, foam, and other materials to furniture frames.
- Marine Industry:
- Boat Construction:Adhesives are used in bonding various materials used in boat construction, such as fiberglass, wood, and metal.
- Hull and Deck Bonding:Adhesives join hull and deck components, providing watertight seals.
These are just a few examples of the diverse applications of industrial bonding adhesives across different sectors. These adhesives’ versatility, strength, and durability make them indispensable in modern manufacturing and construction processes.
What types of materials can be effectively bonded using these adhesives?
The effectiveness of an adhesive in bonding materials depends on the adhesive’s properties and the characteristics of the materials being bonded. Here are some common types of materials that can be effectively connected using different types of adhesives:
1.Wood Adhesives:
a.Wood-to-wood bonding.
b.Wood to other porous materials like paper, cardboard, fabric, etc.
2.Cyanoacrylate (Super Glue) Adhesives:
a.Plastics, including many types of rigid and flexible plastics.
b.Rubber and elastomers.
c.Metal-to-metal bonding for specific applications.
d.Glass and ceramics in some cases.
3.Epoxy Adhesives:
a.Metals, including aluminum, steel, and other alloys.
b.Plastics, especially when the surfaces are adequately prepared.
c.Composite materials like carbon fiber.
d.Glass and ceramics.
e.Wood, when a strong bond is required.
4.Polyurethane Adhesives:
a.Many plastics, including rigid and flexible types.
b.Rubber and elastomers.
c.Metals.
d.Wood, especially in construction and woodworking.
e.Concrete and other construction materials.
5.Acrylic Adhesives:
a.Plastics, including acrylic, PVC, and others.
b.Metals.
c.Glass.
d.Ceramics.
6.Pressure-Sensitive Adhesives (PSAs):
a.Paper and cardboard.
b.Plastics.
c.Fabrics and textiles.
d.Foam materials.
7.Silicone Adhesives:
a.Glass.
b.Ceramics.
c.Some plastics and rubber materials.
d.Metals, if the adhesive is designed for high-temperature applications.
8.Hot-Melt Adhesives:
a.Paper and cardboard.
b.Plastics.
c.Fabrics and textiles.
d.Foam materials.
9.Contact Cement:
a.Laminate materials.
b.Wood.
c.Leather.
d.Some plastics and metals.
10.Anaerobic Adhesives:
a.Metal-to-metal bonding in cases where a chemical reaction can occur without air (anaerobic conditions).
b.Thread Locking compounds, retaining compounds, and gasketing compounds are typical applications.
Remember that the success of an adhesive bond depends on several factors, including surface preparation, adhesive choice, and application techniques. Following the manufacturer’s guidelines and recommendations for the specific adhesive and materials you’re working with is essential to achieve optimal bonding results.
How do industrial bonding adhesives achieve solid and reliable bonds?
Industrial bonding adhesives achieve solid and reliable bonds through chemical, physical, and mechanical processes. The specific mechanisms and factors can vary based on the type of adhesive and the materials being bonded, but here are some general principles:
- Surface Preparation:Proper surface preparation is crucial for achieving solid bonds. Characters must be clean, dry, and free from contaminants like oils, dust, rust, and other particles that might hinder adhesion. Surface methods like cleaning, sanding, and chemical treatments can enhance bonding.
- Adhesive Selection:Choosing the suitable adhesive for the specific materials and conditions is essential. Adhesives come in various types, including epoxies, cyanoacrylates, polyurethanes, and more. Each type has its own characteristics and bonding capabilities. Matching the adhesive’s properties to the substrate materials is critical to achieving a reliable bond.
- Chemical Reaction:Many adhesives undergo a chemical reaction upon curing, which forms strong molecular bonds between the adhesive and the substrate. For instance, in the case of epoxy adhesives, the resin and hardener components react to create a crosslinked polymer network that provides high strength and durability.
- Mechanical Interlocking:Adhesives can create mechanical interlocking by penetrating the microstructures of the substrate’s surface. This is more common in porous or rough surfaces—the adhesive seeps into the irregularities, creating a stronger bond.
- Wetting and Spreading:Adhesives must wet the surface they are bonding to. This means the adhesive should spread out and make intimate contact with the substrate. Good wetting ensures a larger contact area, which leads to stronger bonds.
- Curing Process:The process involves allowing the adhesive to set and harden. This can occur through various methods such as heat, UV light, moisture, or chemical reactions. Proper curing conditions are crucial, as inadequate or excessive curing can lead to weak bonds.
- Adhesive Thickness:The thickness of the adhesive layer also plays a role. A uniform and appropriate thickness ensures even stress distribution and prevents weak spots in the bond.
- Temperature and Environment:Adhesive performance can be affected by temperature and environmental conditions. Some adhesives work better in specific temperature ranges, and exposure to harsh environments like extreme heat, humidity, or chemicals can impact the bond’s reliability.
- Adhesive Strength and Flexibility:Depending on the application, adhesives must balance strength and flexibility. Too rigid, and the bond might fail under stress. Too flexible, and the glue might not hold up over time.
- Quality Control:Manufacturers ensure reliable bonds through rigorous quality control processes. These processes can involve testing the adhesive’s properties, checking the bonding process parameters, and conducting various tests to evaluate bond strength, durability, and resistance to different conditions.
Overall, achieving solid and reliable bonds with industrial adhesives requires a combination of proper adhesive selection, surface preparation, appropriate curing conditions, and attention to environmental factors. It’s also important to follow manufacturer guidelines and best practices to ensure consistent and effective bonding.
When should surface preparation be carried out before applying bonding adhesives?
Surface preparation is crucial before applying bonding adhesives to ensure a solid and durable bond between the surfaces. It helps to improve adhesion and maximize the effectiveness of the adhesive. The specific steps and timing for surface preparation can vary depending on the type of adhesive and the materials being bonded. However, here are some general guidelines:
- Cleanliness:Surfaces must be thoroughly cleaned to remove contaminants such as dust, dirt, grease, oil, moisture, or residues that could hinder adhesion. Cleanliness is essential for a strong bond. Cleaning can be done using solvents, detergents, or abrasive methods, depending on the materials involved.
- Degreasing:If the surfaces are greasy or oily, they should be degreased using appropriate methods or solvents. This step is crucial as adhesives struggle to bond to oily surfaces.
- Roughening:Some adhesive applications require roughening or etching of the surfaces. This is typically done with sandpaper, abrasive blasting, or chemical treatments to create a rough texture that enhances mechanical adhesion.
- Activation:Some adhesives require an activated surface for proper bonding. Activation methods include primers, plasma treatment, corona discharge, or chemical treatments that increase the material’s surface energy.
- Drying:Surfaces need to be completely dry before applying adhesives. Moisture can interfere with the adhesive’s ability to bond properly and lead to weak or failed bonds.
The timing of surface preparation depends on the adhesive being used. Generally, surface preparation should be carried out immediately before applying the adhesive. This is because contaminants can accumulate quickly on a surface, especially in environments with dust, humidity, or other factors affecting adhesion.
It’s essential to follow the manufacturer’s recommendations for the adhesive and the bonded materials. Different glues have specific requirements for surface preparation, so consulting the adhesive’s technical datasheet or the manufacturer’s instructions is crucial to ensure proper bonding.
Why have industrial bonding adhesives become favored for creating seamless, aesthetic final products?
Industrial bonding adhesives have become favored for creating seamless, aesthetic final products for several reasons:
1.No Visible Fasteners or Joints:Adhesives allow joining materials without the need for visible fasteners such as screws, bolts, or rivets. This absence of visible joints enhances the overall aesthetics of the final product, creating a clean and seamless appearance.
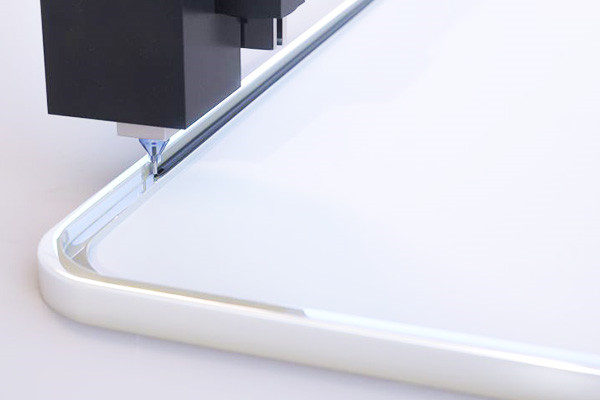
2.Uniform Distribution of Stress:Adhesives distribute stress evenly across the bonded area, unlike traditional mechanical fasteners that can concentrate focus at specific points. This results in a smoother and more even surface, reducing the likelihood of stress-induced deformations, warping, or cracking that can detract from the product’s appearance.
3.Versatile Bonding:Industrial adhesives can bond various materials, including dissimilar ones such as metals, plastics, ceramics, and composites. This versatility allows for innovative design choices combining different materials to achieve functional and aesthetic goals.
4.Reduced Weight:Unlike mechanical fasteners, which can add weight to a product, adhesives are lightweight. This is particularly important in industries where weight reduction is a priority, such as aerospace and automotive, as it can lead to better fuel efficiency and overall performance.
5.Improved Surface Finish:Adhesives create a flush, smooth bond line that eliminates the need for extensive finishing processes like grinding or polishing. This can produce a higher-quality surface finish, contributing to the product’s overall visual appeal.
6.Sealing and Protection:Certain industrial adhesives provide sealing and protective properties, shielding the bonded area from environmental factors such as moisture, chemicals, and contaminants. This not only enhances the product’s appearance but also prolongs its lifespan.
7.Design Freedom:Adhesives allow for more complex and intricate designs that are not feasible with traditional fasteners. Manufacturers can create innovative shapes, curves, and contours that enhance the product’s aesthetics and visual appeal.
8.Reduced Vibrations and Noise:Adhesives can dampen vibrations and reduce noise transmission, contributing to a smoother and quieter user experience. This is particularly relevant in industries where noise reduction is essential, such as electronics or consumer appliances.
9.Enhanced Durability:Properly chosen adhesives can provide long-lasting, durable bonds that withstand various stresses, impacts, and environmental conditions. This durability ensures that the product maintains its aesthetic appeal over time.
10.Automation and Efficiency:Industrial bonding adhesives often allow for automated application processes, reducing the need for manual labor and improving production efficiency. This can lead to consistent, high-quality bonds that contribute to the overall aesthetic of the final product.
Overall, the use of industrial bonding adhesives for creating seamless, aesthetic final products is driven by their ability to simultaneously provide strength, durability, and aesthetic appeal. Manufacturers are drawn to these benefits as they seek to produce products that meet functional and visual requirements in an increasingly competitive market.
What factors should manufacturers consider when selecting the suitable bonding adhesive for a specific application?
Selecting the appropriate bonding adhesive for a specific application is a critical decision manufacturers must make to ensure product performance, durability, and safety. Several factors should be considered during the selection process:
- Substrate Compatibility: The adhesive must be compatible with the materials being bonded. Different materials have varying surface energies and chemical properties, affecting the bonding process. Adhesives that adhere well to the substrates should be chosen without causing any chemical reactions or degradation.
- Bonding Strength: The required strength of the bond depends on the application. Some applications require high tensile, shear, or peel strength, while others may need a more flexible or temporary bond. Manufacturers should select an adhesive that provides the desired level of bonding strength.
- Environmental Conditions: Consider the environment the bonded materials will be exposed to, including temperature variations, humidity, chemicals, UV exposure, and more. Adhesives that can withstand these conditions should be chosen without losing their bonding properties.
- Curing Time and Process: Some adhesives cure quickly, while others require longer healing times. Manufacturers need to consider their production processes and whether they can accommodate the adhesive’s curing time. Additionally, some bonds require specific curing conditions such as heat, pressure, or UV light.
- Application Method: Different adhesives can be applied using various methods like spraying, brushing, dipping, or automated dispensing. Manufacturers should select a bond that can be applied using their preferred method and equipment.
- Health and Safety: Manufacturers should consider the health and safety implications of using a particular adhesive. Some adhesives emit volatile organic compounds (VOCs) during curing, which can impact the work environment and potentially harm workers’ health.
- Cost Considerations: Adhesive costs can vary significantly based on the type of adhesive and its performance characteristics. Manufacturers should balance performance requirements with the cost of the adhesive to ensure cost-effectiveness.
- Aging and Durability: Adhesives can degrade over time due to temperature, moisture, and exposure to environmental conditions. Manufacturers should choose adhesives that offer long-term durability and resistance to aging.
- Assembly Process: The assembly process itself can influence adhesive selection. For instance, if components need to be aligned and adjusted after application, an adhesive with repositioning capability may be necessary.
- Regulations and Standards: Depending on the industry and application, specific rules or industry standards might dictate the type of adhesive that can be used. Manufacturers should ensure that the selected adhesive complies with relevant regulations.
- Ease of Use: Some adhesives require specialized equipment or skilled labor for application, while others are more user-friendly. Manufacturers should consider the ease of integrating the adhesive into their production process.
- Serviceability and Repairability: If the bonded materials need to be repaired or serviced in the future, the choice of adhesive can impact how easy or difficult it is to disassemble and re-bond the components.
- Aesthetics and Design: In some applications, the appearance of the bonded joint is essential. Manufacturers should choose adhesives that provide a clean, aesthetically pleasing finish.
By carefully evaluating these factors and conducting thorough testing, manufacturers can choose the most suitable bonding adhesive for their specific application, ensuring optimal performance and long-term reliability.
How do curing processes vary among different types of bonding adhesives?
Curing processes for bonding adhesives can vary significantly based on the type of adhesive chemistry being used. The curing process is when the adhesive transitions from a liquid or semi-liquid state to a solid state, resulting in a strong bond between substrates. Different types of adhesives use various mechanisms and conditions for curing. Here are some common types of bonding adhesives and their respective curing processes:
- Anaerobic Adhesives:Anaerobic adhesives cure in the absence of oxygen. They are commonly used for thread-locking, retaining, and sealing applications. These adhesives remain liquid until they are confined between closely fitting metal surfaces. Curing is initiated when the bond is exposed to metal ions, moisture, and the absence of oxygen. Heat can also accelerate the curing process.
- Cyanoacrylate Adhesives (Super Glue):Cyanoacrylate adhesives cure through a reaction with surface moisture. When exposed to water vapor, the adhesive polymerizes rapidly, forming a solid bond. The curing process can be slowed down using a bonding agent that reduces surface moisture or accelerated by adding an alkaline substance. These adhesives bond quickly and are commonly used for small-scale bonding.
- Epoxy Resin Adhesives:Epoxy adhesives consist of two components: the resin and the hardener. Curing is initiated when these two components are mixed. The curing process can be controlled by adjusting the ratio of resin to hardener, temperature, and the presence of any accelerators. Depending on the formulation, epoxy adhesives can cure at room temperature or elevated temperatures.
- Polyurethane Adhesives:Polyurethane adhesives typically undergo a two-step curing process. First, they react with atmospheric moisture (moisture-curing) to initiate polymerization. Then, they continue to cure through a chemical reaction involving isocyanate and hydroxyl groups in the adhesive. The curing process can occur at room temperature or with heat application.
- Acrylic Adhesives:Acrylic adhesives cure through a process known as “evaporation of the solvent.” These adhesives are often solvent-based, and the solvent must evaporate for the glue to solidify and create a bond. Temperature, humidity, and air circulation can control the evaporation rate.
- UV-Curable Adhesives:UV-curable adhesives are formulated to cure when exposed to ultraviolet (UV) light. These adhesives remain liquid until they are exposed to the specific wavelength of UV light, triggering a polymerization reaction. This type of adhesive offers rapid curing times and is often used in applications that require quick assembly.
- Heat-Curing Adhesives:Some adhesives require elevated temperatures to cure. These adhesives are often used in industrial applications requiring high bond strength and temperature resistance. The curing temperature and duration depend on the adhesive formulation and bonded materials.
It’s important to carefully follow the manufacturer’s guidelines for curing each type of adhesive, as improper curing can result in weak bonds or other undesirable outcomes. The curing process is critical in achieving the desired adhesive performance, so understanding the specific requirements for each adhesive type is essential for successful bonding.
When is a fast curing time preferable, and when might a slower process be necessary?
Fast curing times and slow processes have advantages and disadvantages, and their appropriateness depends on the specific context and application. Here’s a breakdown of when a short curing time might be preferable and when a slower process might be necessary:
Fast Curing Time (Advantages):
- Efficiency in Production:In industries where quick turnaround is essential, such as manufacturing, electronics assembly, and automotive production, fast curing times can lead to higher production efficiency. Reduced curing times mean more products can be manufactured in a shorter time frame.
- Emergency Repairs:In situations where a rapid repair is needed, such as fixing a leak or addressing a structural issue, fast-curing materials can be crucial. This is common in construction, plumbing, and maintenance work.
- Minimized Downtime:Using fast-curing materials can help reduce the system’s non-functional time when dealing with equipment or machinery downtime. This is particularly relevant in industries like aviation and transportation.
- Reduced Labor Costs:Faster curing times can lead to shorter waiting periods between production steps, reducing the labor costs associated with waiting for materials to set or cure.
Fast Curing Time (Disadvantages):
- Quality and Strength:Some materials may sacrifice strength and durability for quick curing. A slower curing process might be necessary to ensure the highest quality end product in applications where structural integrity is crucial.
- Limited Workability:Faster curing materials may have a shorter workable time, making it challenging to manipulate or shape the material before it sets. This could be a concern in applications like molding or casting.
Slower Process (Advantages):
- Improved Quality:Slower curing processes often result in better material properties, including enhanced strength, durability, and resistance to environmental factors. This is important in applications where the final product needs to withstand stress, wear, or harsh conditions.
- Reduced Residual Stresses:Slow curing can allow materials to cure more uniformly, reducing the risk of internal stresses that might lead to warping, cracking, or other structural issues.
- Complex Shapes:Slower curing times provide more flexibility in working with complex shapes and designs. This is crucial in industries like art, sculpture, and custom fabrication.
- Better Adhesion:Slow curing can facilitate better adhesion to substrates, essential in applications like bonding materials or coatings.
Slower Process (Disadvantages):
- Extended Production Time:Slower curing times can lead to longer production cycles, which may not be feasible in industries where rapid production is a priority.
- Increased Labor Costs:Longer curing times may require more labor to monitor and manage the curing process and additional storage space for materials in the curing phase.
In essence, the choice between fast and slow curing times depends on the specific requirements of the project or application. It’s essential to balance efficiency with the desire for high-quality end products. Sometimes, a compromise between the two may be the most appropriate solution.
Why do industries face challenges related to temperature and environmental conditions when using bonding adhesives?
Industries often face challenges related to temperature and environmental conditions when bonding adhesives due to the complex nature of adhesive materials and the specific requirements of various applications. Here are some of the key reasons:
- Adhesive Properties at Different Temperatures: Most bonding adhesives exhibit varying properties at different temperatures. Adhesive performance, including viscosity, curing time, and strength, can change significantly as the temperature fluctuates. This makes it crucial for industries to select adhesives that can maintain their effectiveness across the desired application temperature range.
- Curing and Bond Strength: Many adhesives use curing processes to develop their full bond strength. Temperature can influence the rate of curing, affecting the time it takes for the adhesive to reach its maximum strength. Low temperatures can sometimes slow curing, potentially leading to prolonged production times or reduced bond strength. High temperatures accelerate curing but could cause premature curing or reduced final power.
- Thermal Expansion and Contraction: Different materials have varying coefficients of thermal expansion, meaning they expand or contract at different rates when exposed to temperature changes. This can create stress at the adhesive interface as materials shift, potentially leading to bond failure over time.
- Chemical Compatibility: Some adhesives are sensitive to specific environmental conditions, including exposure to chemicals, moisture, UV radiation, and other factors. Extreme temperatures can exacerbate the effects of chemical exposure, causing the adhesive to degrade or lose its properties more rapidly.
- Elasticity and Brittleness: Temperature changes can impact the mechanical properties of adhesives, such as their elasticity and brittleness. Low temperatures can render certain bonds more brittle, increasing the risk of cracking or delamination under mechanical stress. High temperatures can increase elasticity, potentially causing the adhesive to creep or flow under load.
- Service Conditions: Industries often use adhesives in applications with demanding service conditions, such as aerospace, automotive, electronics, and construction. These conditions may involve exposure to wide temperature ranges, rapid cycling, and extreme environmental factors. Adhesives used in such applications must be capable of maintaining their performance under these challenging conditions.
- Regulatory Compliance: Some industries have strict regulatory requirements regarding the use of adhesives in specific environments. Adhesives must meet certain flame resistance standards, low toxicity, or environmental impact. Extreme temperatures can influence the ability of bonds to meet these standards.
To address these challenges, industries must carefully consider selecting adhesive materials based on their intended application and the environmental conditions they will be exposed to. Testing and evaluating adhesive performance under different temperatures and environmental conditions are essential to ensuring the longevity and reliability of bonded assemblies.
What role does the shear strength of bonding adhesives play in applications?
The shear strength of bonding adhesives is crucial in various applications where adhesion is required to hold materials together. Shear power refers to the ability of an adhesive to withstand forces that attempt to slide or shear the bonded materials parallel to their surfaces. In other words, it measures how well the adhesive can resist the tendency of materials to separate when a lateral force is applied.
Here’s how shear strength is essential in different applications:
- Manufacturing and Construction: In industries like automotive, aerospace, electronics, and construction, bonding adhesives are used to join various materials together. Shear strength ensures that components remain securely attached even under dynamic or load-bearing conditions. For example, in aircraft construction, adhesive bonding is used to connect critical components, and the shear strength of the adhesive is essential for maintaining structural integrity during flight.
- Automotive Industry: Bonding adhesives are widely used in the automotive sector for applications such as attaching body panels, bonding interior components, and securing safety systems. Adequate shear strength ensures these components stay in place even when subjected to vibrations, impacts, and other mechanical stresses.
- Electronics and Microelectronics: In electronics assembly, adhesive bonding attaches components to circuit boards and substrates. Shear strength is essential to ensure that delicate electronic components remain securely attached, even in devices subjected to temperature variations and mechanical stress.
- Medical Devices: Many medical devices use bonding adhesives to join different materials, including plastics and metals. Shear strength is critical to maintaining the integrity of medical devices during use and sterilization processes.
- Packaging and Labeling: Adhesive bonding is used in packaging applications to seal boxes, attach labels, and secure products. Shear strength ensures the packaging remains intact and brands stay attached during transportation, handling, and storage.
- Furniture and Woodworking: Bonding adhesives are used in woodworking and furniture manufacturing to create strong joints without needing traditional fasteners like nails or screws. Shear strength is vital to ensure the longevity and stability of the furniture or woodworking project.
- Sporting Goods and Outdoor Equipment: Shear strength is crucial in applications where adhesives bond materials for sporting goods like skis, snowboards, and bicycles. These products are subjected to various forces, and the adhesive’s shear strength helps maintain its structural integrity.
In all these applications, the shear strength of bonding adhesives contributes to the final product’s overall performance, safety, and durability. Engineers and designers must consider the specific requirements of each application to select adhesives with appropriate shear strength properties. Factors like material compatibility, temperature extremes, exposure to chemicals, and mechanical stresses influence the adhesive’s choice and its shear strength characteristics.
How can industries ensure the longevity and durability of products bonded using these adhesives?
Ensuring the longevity and durability of products bonded using adhesives involves a combination of proper material selection, surface preparation, application techniques, and quality control measures. Here are some steps industries can take to enhance the lifespan and durability of products bonded with adhesives:
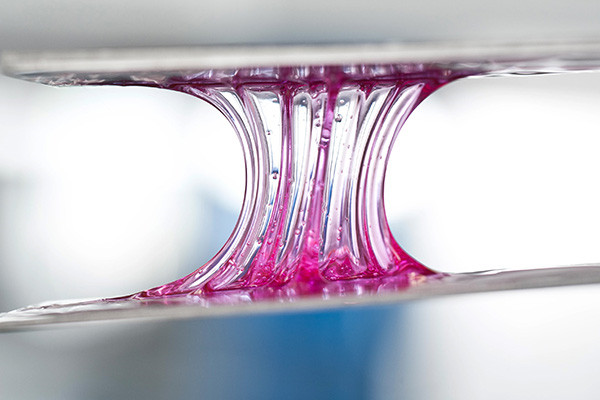
- Material Selection:Choose adhesives specifically designed for the intended application and the bonded materials. Different adhesives have varying properties, such as flexibility, temperature, and chemical resistance. Please ensure the adhesive’s properties align with the requirements of the product and its intended use.
- Surface Preparation:Proper surface preparation is crucial for creating a solid bond. Surfaces should be clean, dry, and free from contaminants like dirt, oil, grease, and rust. Depending on the materials involved, surface treatments like sanding, degreasing, or primers might be necessary to promote adhesion.
- Adhesive Application:Follow the manufacturer’s guidelines for adhesive application, including recommended temperature ranges, curing times, and mixing ratios (if applicable). Proper dispensing techniques, whether manual or automated, are essential to ensure uniform and consistent adhesive coverage.
- Joint Design:The bonded joint’s design can influence the bond’s strength and durability. Factors like standard geometry, overlap area, and stress distribution should be considered to optimize the joint for longevity. Proper joint design can minimize stress concentrations and prevent premature failure.
- Curing Conditions:Adhesives typically require specific curing conditions, such as temperature and humidity levels, to achieve their full strength. Ensure that the curing conditions are maintained throughout the curing process. Inadequate curing can lead to weakened bonds and reduced durability.
- Quality Control:Implement stringent quality control measures to monitor the adhesive bonding process. Regular testing and inspection can identify issues early on and ensure the products meet desired performance standards.
- Testing and Validation:Perform appropriate testing and validation procedures to assess the durability of the adhesive bonds. This can include mechanical testing, environmental exposure testing (e.g., temperature, humidity, UV radiation), and long-term performance testing to simulate real-world conditions.
- Maintenance and Service Life Prediction:Understand the expected service environment of the bonded product. Consider factors such as temperature fluctuations, exposure to chemicals, mechanical stresses, and other conditions that could impact the adhesive bond over time. Perform regular maintenance and inspections to identify and address any signs of degradation.
- Documentation and Training:Ensure that personnel involved in the adhesive bonding process are adequately trained and follow established procedures. Maintain comprehensive documentation of adhesive selection, surface preparation, application techniques, curing conditions, and testing results. This information can aid in troubleshooting and process improvement.
- Continuous Improvement:Continuously monitor the performance of bonded products in real-world conditions and gather customer feedback. Use this information to make informed decisions about material selection, process improvements, and design changes to enhance the longevity and durability of products bonded with adhesives.
By carefully following these steps and considering the specific requirements of each application, industries can increase the likelihood of achieving robust and durable adhesive bonds that stand the test of time.
When are flexible bonding adhesives more suitable than rigid ones?
Flexible bonding adhesives are more suitable than rigid ones in situations where the materials being bonded have different coefficients of thermal expansion, need to withstand vibration or dynamic loading, or require some degree of flexibility for movement. Here are some scenarios where flexible bonding adhesives are preferred:
- Dissimilar Material Bonding:When bonding materials with significantly different coefficients of thermal expansion, such as metal to plastic or glass to plastic, using a rigid adhesive can lead to stress buildup and eventual bond failure due to temperature changes. Flexible sealants can absorb some of this stress and allow for differential movement.
- Vibration and Dynamic Loading:Applications that experience vibration, shock, or dynamic loading, such as automotive parts, electronic devices, or aerospace components, benefit from flexible adhesives. These adhesives can dampen vibrations and prevent stress propagation through the bonded joint, enhancing the durability and longevity of the bond.
- Peel and Shear Forces:Situations involving peel and shear forces, such as joining flexible substrates like fabrics, films, or membranes, require adhesives that can withstand such stresses without cracking or delaminating. Flexible bonds provide the necessary give to accommodate these forces.
- Structural Joints with Movement:When bonding components in a structural assembly that might undergo slight movement or deflection due to load, wind, or other environmental factors, a flexible adhesive is preferable. This flexibility ensures the bond remains intact even when the materials shift slightly.
- Thermal Cycling:Applications exposed to rapid or cyclic temperature changes can benefit from flexible adhesives. Rigid adhesives can become brittle and lose their bond strength under extreme temperature fluctuations, while flexible adhesives maintain their integrity.
- Impact Resistance:Flexible bonding adhesives offer better impact resistance than rigid adhesives. They can absorb energy from impacts without rupturing the bond, making them suitable for applications where protection against sudden effects is crucial.
- Sealing and Gap Filling:In situations with irregularities, gaps, or uneven surfaces to be bonded, flexible adhesives can fill voids and provide a more uniform bond line. This is particularly important for maintaining proper sealing and preventing the ingress of contaminants.
- Non-Structural Bonding:Flexible adhesives can be used for applications where the adhesive joint doesn’t need to bear significant loads but requires some flexibility. These include cosmetic bonding, sealing, and specific electronics applications.
It’s important to note that the choice between flexible and rigid adhesives depends on the application’s specific requirements. Careful consideration of the materials being bonded, the expected mechanical stresses, and the environmental conditions to which the bonded joint will be exposed is essential to determine the most suitable adhesive type.
Why are automotive and aerospace industries increasingly adopting industrial bonding adhesives?
The automotive and aerospace industries are increasingly adopting industrial bonding adhesives for several compelling reasons:
- Weight Reduction: Adhesives are often lighter than mechanical fasteners, such as bolts and rivets. In aerospace, reducing weight is critical for fuel efficiency and overall performance, while in the automotive industry, it contributes to better fuel economy and handling.
- Enhanced Design Flexibility: Adhesives allow for more intricate and complex designs that are difficult to achieve with traditional fasteners. This flexibility leads to improved aerodynamics, aesthetics, and overall product performance.
- Stress Distribution: Adhesives distribute stress more evenly across bonded surfaces compared to localized stress points created by mechanical fasteners. This leads to better load distribution, reduced stress concentrations, and improved structural integrity.
- Improved Performance: Bonded structures often exhibit better fatigue resistance, vibration damping, and noise reduction than those assembled with mechanical fasteners. This is particularly important in aerospace, where structural integrity and passenger comfort are critical.
- Corrosion Prevention: Traditional fasteners can create galvanic corrosion due to the contact between dissimilar metals. Adhesives eliminate this issue, enhancing the longevity and reliability of bonded components, especially in harsh environments.
- Reduced Assembly Time: Adhesive bonding processes can be faster and more efficient than traditional fastening methods. This is particularly beneficial for high-volume manufacturing in the automotive industry and the complex assembly processes in aerospace.
- Improved Aesthetics: Adhesives often result in smooth, jointless surfaces, improving the overall appearance of the finished product.
- Reduced Joining Points: Adhesives can eliminate or reduce the need for mechanical fasteners, reducing the number of joining and potential failure points in the structure.
- Cost Savings: While initial material costs might be higher for adhesives, reducing assembly time, labor costs, and maintenance over the product’s lifecycle can lead to overall cost savings.
- Environmental Considerations: Adhesives can potentially be more environmentally friendly than traditional fastening methods. For example, they can reduce the need for drilling, punching, and other machining processes that generate waste and consume energy.
- Material Compatibility: Adhesives can bond various materials, including dissimilar materials like metals and composites. This provides greater freedom in material selection and design optimization.
- Advancements in Adhesive Technology: Ongoing research and development have led to the formulation of adhesives that offer superior bonding strength, durability, and resistance to extreme conditions, making them suitable for use in demanding automotive and aerospace applications.
What safety precautions should be followed during the application of bonding adhesives?
Applying bonding adhesives requires careful attention to safety to ensure both the effectiveness of the adhesive and the safety of the individuals involved. Here are some essential safety precautions to follow during the application of bonding adhesives:
- Instructions:Always carefully read and understand the manufacturer’s instructions and safety data sheet (SDS) before using any bonding adhesive. This will provide information on proper application methods, recommended safety gear, and any hazards associated with the adhesive.
- Personal Protective Equipment (PPE):Wear the appropriate personal protective equipment, including safety goggles, gloves, long sleeves, and pants. The specific PPE required can vary depending on the adhesive’s properties, so refer to the SDS for guidance.
- Ventilation:Ensure proper ventilation in the application area to prevent the buildup of potentially harmful fumes or vapors. If working in an enclosed space, consider using exhaust fans, open windows, or other ventilation methods to keep the air clear.
- Avoid Skin Contact:Avoid direct skin contact with bonding adhesives. If contact occurs, immediately wash the affected area with soap and water. Some adhesives can cause skin irritation or allergic reactions.
- Eye Protection:Wear safety goggles or a face shield to protect your eyes from splashes or accidental contact with the adhesive. If adhesive comes into contact with the eyes, flush them with water for at least 15 minutes and seek medical attention.
- Work Area Preparation:Prepare your work area by removing any unnecessary items and keeping it clean and organized. This reduces the risk of spills or accidents during the adhesive application process.
- Flammability:Be aware of the flammability characteristics of the adhesive. If the adhesive is flammable, avoid open flames, sparks, and smoking in the work area.
- No Eating or Drinking:Do not consume food, drinks, or smoke while working with bonding adhesives. This helps prevent accidental ingestion of adhesive residues.
- Chemical Compatibility:Be cautious about using the adhesive on surfaces that may not be chemically compatible. Some adhesives can react with certain materials, causing damage or compromising the bond.
- Emergency Preparedness:Keep a first aid kit and an emergency eyewash station or shower nearby in case of accidental exposure or spills. Ensure that everyone working with the adhesive knows the location of these safety resources.
- Dispose of Waste Properly:Dispose of any waste materials, containers, and rags according to local regulations and the adhesive manufacturer’s guidelines. Do not pour adhesive down drains or into the environment.
- Training:Provide proper training to individuals working with the adhesive. Ensure they understand the potential hazards, safety precautions, and emergency procedures.
Safety is paramount when working with potentially hazardous substances like bonding adhesives. Always consult the adhesive manufacturer’s guidelines and the safety data sheet for specific recommendations based on the type of adhesive you’re using. If in doubt, seeking guidance from professionals or experts in adhesive application is a good practice.
How does ongoing research contribute to the enhancement of industrial bonding adhesive technologies?
Ongoing research is critical in enhancing industrial bonding adhesive technologies in several ways. Adhesive technologies are used in various industries, including automotive, aerospace, electronics, construction, and more. Continuous research contributes to developing adhesives with improved properties, efficiency, and versatility. Here’s how ongoing research contributes to the enhancement of industrial bonding adhesive technologies:
- Improved Formulations and Materials: Ongoing research helps scientists and engineers develop new adhesive formulations using novel materials and combinations. Researchers can identify materials that offer better adhesion, durability, and resistance to various environmental factors such as temperature, moisture, chemicals, and UV exposure. These advancements lead to adhesives with enhanced performance characteristics.
- Customization for Specific Applications: Different industries and applications have unique bonding requirements. Ongoing research enables the customization of adhesive formulations to meet the specific needs of different industries. For instance, adhesives used in aerospace applications must withstand extreme temperature fluctuations and vibrations, while electronics must have excellent conductivity and thermal management properties. Research allows adhesives to be tailored to these diverse demands.
- Enhanced Bond Strength and Durability: Research helps understand the fundamental mechanisms behind adhesive bonding. This knowledge allows scientists to optimize adhesive chemistries and bonding techniques to achieve more robust and durable bonds. An improved understanding of surface interactions, chemical reactions, and stress distribution helps design adhesives that provide reliable performance over extended periods.
- Reduced Environmental Impact: Ongoing research is focused on developing adhesive technologies that are more environmentally friendly. This includes creating adhesives with lower volatile organic compound (VOC) emissions, reduced toxicity, and improved biodegradability. These efforts contribute to sustainability goals and regulatory compliance.
- Faster Curing and Processing Times: Adhesive and processing times can significantly impact manufacturing efficiency. The research aims to develop adhesives that cure quickly without compromising bond strength. Advancements in this area can lead to faster production cycles and increased productivity.
- Innovative Bonding Techniques: Research explores new bonding techniques and methodologies that can revolutionize industrial applications. This includes methods like structural adhesives, nano adhesives, and bio-inspired adhesives. These innovative approaches expand the range of materials that can be bonded and improve overall bond performance.
- Quality Control and Testing: Ongoing research contributes to developing improved testing methods and quality control processes for adhesive bonding. Non-destructive testing techniques, such as ultrasonic or thermal imaging, can be refined to detect defects and weaknesses in bonded joints, ensuring higher reliability in industrial applications.
- Multifunctional Adhesives: Research is focused on creating adhesive technologies that offer multiple functionalities beyond just bonding. For instance, adhesives can be engineered to provide electrical conductivity, thermal insulation, corrosion resistance, or even self-healing properties. This versatility opens up new possibilities for various industries.
- Simulation and Modeling: Advanced computational techniques allow researchers to simulate and model adhesive behavior under different conditions. This helps predict performance, optimize designs, and reduce the need for extensive physical testing, thereby accelerating the development process.
When is the future of manufacturing predicted to be shaped by advancements in bonding adhesive solutions?
The specific timeline for when these advancements will significantly impact manufacturing can vary depending on factors like technological breakthroughs, market demand, and adoption rates. Adhesive bonding solutions have been gaining importance in various industries due to their ability to replace or supplement traditional mechanical fastening methods like welding, riveting, and screws.
Some areas where adhesive bonding is already having a significant impact include:
- Automotive Industry: Adhesive bonding is increasingly used in automobile manufacturing for lightweight construction, improved safety, and enhanced fuel efficiency.
- Aerospace Industry: Adhesive bonding is utilized in aerospace applications to reduce weight, improve aerodynamics, and enhance overall structural integrity.
- Electronics Industry: Miniaturization and the need for precise bonding have driven the development of advanced adhesive solutions for electronics assembly and packaging.
- Medical Devices: Adhesive bonding is essential for joining different medical devices and equipment materials, enabling improved functionality and biocompatibility.
- Consumer Goods: Adhesives play a role in creating aesthetically pleasing consumer product designs and improving durability and performance.
- Renewable Energy: Adhesives are used in manufacturing solar panels and wind turbine components, aiding in the construction of efficient and reliable renewable energy systems.
Advancements in adhesive technology are driven by ongoing research and development efforts to create stronger, more durable, and more versatile adhesive materials. These advancements can include improved adhesion to various substrates, better resistance to environmental factors, and enhanced curing processes.