One Component Epoxy Adhesive
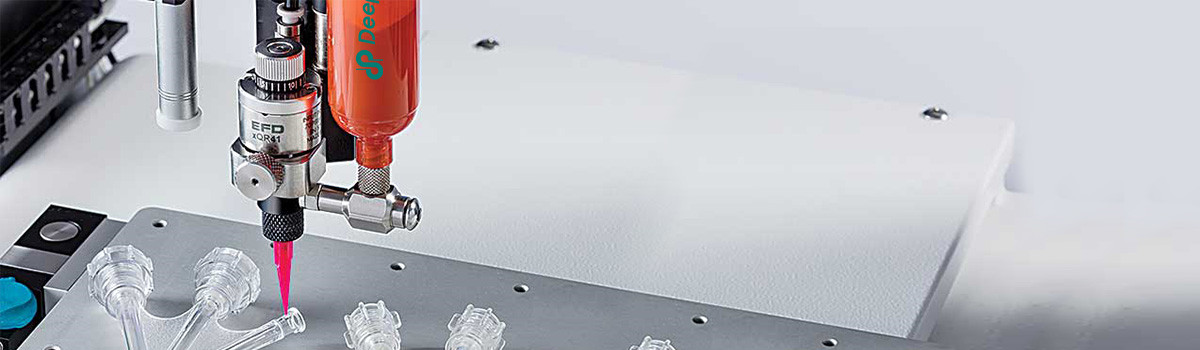
In the world of adhesive technology, one component epoxy adhesives have emerged as a game-changing solution, offering a streamlined approach to bonding that combines convenience with high-performance results. Unlike traditional two-component adhesives that require mixing, these adhesives come pre-formulated and ready for use. This unique characteristic simplifies the bonding process while retaining the exceptional strength, durability, and versatility that epoxy adhesives are known for. This comprehensive exploration delves into the realm of one component epoxy adhesives, uncovering their mechanisms, applications, benefits, and their pivotal role in transforming bonding processes across industries.
Exploring One Component Epoxy Adhesives
One component epoxy adhesives have emerged as a remarkable solution in the realm of adhesive technologies, offering a range of benefits and applications across various industries. As the name suggests, these adhesives consist of a single component that eliminates the need for mixing prior to application, simplifying the bonding process. The advantages presented by these adhesives are multi-faceted, making them a preferred choice in many scenarios.
- Simplicity and Convenience:One of the key advantages of one component epoxy adhesives is their user-friendly nature. Without the requirement for mixing multiple components, the application process becomes significantly simpler, reducing the chances of errors and saving valuable time. This feature is particularly advantageous in high-volume production settings where efficiency is paramount.
- High Bonding Performance:Despite being a single-component formulation, these adhesives offer exceptional bonding performance. They can adhere to various substrates, including metals, plastics, ceramics, and composites, providing robust and durable bonds even under harsh conditions. This versatility makes them suitable for multiple industries, such as automotive, electronics, aerospace, and medical devices.
- Chemical and Environmental Resistance: One component epoxy adhesives are known for their remarkable resistance to chemicals, solvents, and environmental factors such as temperature fluctuations and moisture exposure. This resilience ensures that the bonded joints maintain their integrity over time, contributing to the overall longevity of the related materials.
- Cost-Effectiveness: The simplified application process and the reduced likelihood of mixing errors translate to cost savings in both labor and material. Additionally, these adhesives’ high bond strength and durability contribute to longer-lasting assemblies, further enhancing their cost-effectiveness in the long run.
- Customization and Flexibility:Manufacturers can customize specific properties of one component of epoxy adhesives to meet precise requirements. These adjustments encompass cure time, viscosity, and even color, facilitating the creation of adhesive solutions that precisely match the application’s needs.
Advantages of One Component Formulation
One component epoxy adhesives have garnered significant attention due to their unique formulation and the array of benefits they offer. These adhesives, characterized by their single-component nature, come with many advantages, making them a preferred choice across diverse industries.
Simplicity and Efficiency
The foremost advantage of one component epoxy adhesives lies in their simplicity and user-friendly application process. Unlike two-component adhesives that require precise mixing, these formulations come ready to use, eliminating the need for measuring and blending. This streamlined process reduces the chances of errors and accelerates the bonding procedure, making them ideal for high-volume production environments where efficiency is paramount.
Consistent Bonding Performance
Despite their single-component composition, these adhesives exhibit remarkable bonding performance. They are engineered to establish robust and enduring bonds across various substrates, encompassing metals, plastics, ceramics, and composites. Their versatility makes these adhesives indispensable in the electronics and aerospace industries, where they securely join diverse materials.
Enduring Resilience
One component of epoxy adhesives boasts exceptional resistance to various environmental factors. From chemical exposure to temperature fluctuations and moisture ingress, these adhesives maintain their integrity over time, ensuring the longevity of bonded assemblies. This durability is particularly valuable in applications exposed to harsh conditions, contributing to the overall reliability of the finished product.
Cost-Effective Solution
The simplified application process of one component epoxy adhesives leads to cost savings on multiple fronts. Reduced labor time and minimized chances of mixing errors translate into increased efficiency and decreased production costs. Moreover, their reliable bond strength and resilience contribute to longer-lasting assemblies, reducing the need for frequent repairs or replacements.
Tailored to Specific Needs
Manufacturers can customize the properties of one component epoxy adhesives to suit specific application requirements. This flexibility allows for adjustments in cure time, viscosity, and even color, ensuring that the adhesive formulation aligns precisely with the demands of the task at hand. This versatility makes them adaptable to various applications, from intricate electronics to heavy-duty industrial bonding.
Mechanisms of Epoxy Adhesion
Understanding the mechanisms behind epoxy adhesion is crucial for optimizing the performance of epoxy-based adhesive systems. The adhesion process involves intricate interactions between the adhesive, the substrate, and the surrounding environment, leading to the formation of strong and durable bonds.
Chemical Bonding
Chemical bonding is a fundamental mechanism driving epoxy adhesion. Epoxy adhesives typically contain reactive functional groups, such as epoxide (oxirane) rings, that can react with various substrates. This chemical reactivity enables the adhesive to form covalent bonds with the substrate’s surface molecules, resulting in a strong and permanent attachment. The formation of these bonds contributes to the adhesive’s ability to withstand stresses and environmental conditions.
Dispersion and Intermolecular Forces
Apart from chemical bonding, dispersion forces play a significant role in epoxy adhesion. These forces, also known as van der Waals forces, arise from temporary fluctuations in electron distribution within molecules. Dispersion forces allow epoxy adhesives to interact with substrates through weak, attractive points that facilitate adhesion on a molecular level. Additionally, intermolecular forces like hydrogen bonding can enhance the adhesive’s ability to adhere to specific substrates, further strengthening the bond.
Wetting and Spreading
The mechanism of wetting and spreading is pivotal for achieving intimate contact between the adhesive and the substrate. Proper wetting ensures the adhesive flows across the substrate’s surface, minimizing air pockets and maximizing the surface area in contact. Enhanced wetting promotes better adhesion by reducing the risk of voids and weak points within the bond.
Surface Preparation and Adhesion Promoters
Adequate epoxy adhesion often requires proper surface preparation. Substrates may have contaminants or surface oxides that hinder adhesion. Mechanisms like surface cleaning, sanding, or chemical treatments can improve the substrate’s surface energy and remove barriers to adhesion. In some cases, adhesion promoters or primers bridge the adhesive and the substrate, facilitating bonding.
Curing and Crosslinking
The final phase of epoxy adhesion involves curing, where the adhesive undergoes a chemical reaction that transforms it from a liquid or semi-liquid state to a solid. During this process, crosslinking occurs, forming a three-dimensional network of polymer chains. This network reinforces the bond and enhances the adhesive’s mechanical properties, such as strength and stiffness.
Types of One Component Epoxy Adhesives
One epoxy adhesive component has evolved to encompass a range of specialized formulations, each designed to cater to specific application needs. These adhesive types offer tailored solutions across various industries, presenting a variety of curing mechanisms, properties, and advantages.
1.Heat Cure One Component Epoxy Adhesives:These adhesives require elevated temperatures for curing, often containing thermally activated initiators. They excel in applications where controlled heat can be applied, delivering high bond strength and resistance to temperature fluctuations.
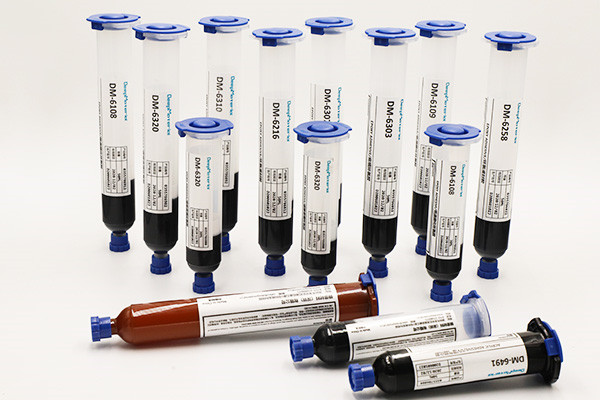
2.UV Cure One Component Epoxy Adhesives:UV-curing formulations leverage photoinitiators to achieve rapid bonding upon exposure to ultraviolet light. They are ideal for applications demanding quick assembly, precision, and immediate bond strength.
3.Moisture Cure One Component Epoxy Adhesives:Curing occurs upon exposure to ambient moisture, facilitated by moisture-activated crosslinkers. These adhesives are versatile and often chosen for challenging temperature control environments.
4.Room Temperature Cure One Component Epoxy Adhesives:These adhesives cure at ambient temperatures without requiring heat or UV exposure. They find utility in various industries, offering ease of use and strong bond formation.
5.Flexible and Toughened One Component Epoxy Adhesives:These formulations incorporate modifiers for enhanced flexibility and impact resistance. They are well-suited for vibrations, shocks, or mechanical stress applications.
6.Low Outgassing One Component Epoxy Adhesives:To prevent contamination in sensitive environments, these adhesives, designed for aerospace and electronics, release minimal volatile compounds when curing.
7.Thermally Conductive One Component Epoxy Adhesives:Engineers have designed these formulations to facilitate heat transfer, rendering them suitable for efficient thermal management applications.
8.Electrically Conductive One Component Epoxy Adhesives:These adhesives, tailored for electronics, offer bonding and electrical conductivity, enabling secure connections in electronic assemblies.
Each type of one component epoxy adhesive brings distinct advantages to the table, allowing engineers and manufacturers to select the most appropriate formulation based on the requirements of their specific project. This diversity underscores the versatility of these adhesives in industries ranging from electronics and automotive to aerospace and beyond.
Structural Bonding with One Component Epoxies
Modern manufacturing and construction rely heavily on structural bonding, a critical process wherein materials securely join to form robust and dependable products. One component epoxies have emerged as a versatile solution for achieving solid and durable bonds in various applications. These adhesives offer convenience and simplicity as they eliminate the need for mixing two components before application. This paragraph explores the benefits, applications, and considerations associated with structural bonding using one component epoxies.
Benefits of One Component Epoxies:
One component epoxies offer several advantages, making them a popular choice for structural bonding. Their single-package nature simplifies the bonding process, reducing the chances of mixing errors and waste. They also provide an extended shelf life and are ready to use, minimizing the need for complex preparation. These adhesives exhibit excellent chemical and temperature resistance, ensuring the longevity of bonded materials even in challenging environments. Additionally, their high strength and load-bearing capacity contribute to the structural integrity of the final product.
Applications of One Component Epoxies:
The versatility of one component epoxies lends them to a wide range of applications. The automotive, aerospace, electronics, and construction industries employ these adhesives to bond various materials, including metals, composites, ceramics, and plastics. They assemble components, attach inserts, seal joints, and encapsulate sensitive electronics. The adhesives’ ability to withstand vibrations, impact, and thermal cycling makes them suitable for critical applications where reliability is paramount.
Considerations and Best Practices:
While one component of epoxies offers numerous benefits, there are considerations to consider. Proper surface preparation is crucial for achieving optimal bond strength. Surfaces should be clean, dry, and contaminant-free to ensure a robust adhesive interface. Additionally, curing time and temperature play a significant role in achieving the desired bond strength. Manufacturers must follow recommended curing procedures to avoid compromising the adhesive’s performance. It’s also important to consider the application’s specific requirements, such as the expected load, temperature fluctuations, and exposure to chemicals or moisture.
Heat and Chemical Resistance
Component Epoxy Adhesives with exceptional heat and chemical resistance have gained significant attention for their versatile application in industries requiring durable and reliable bonding solutions amidst challenging environments.
High-Temperature Stability: These adhesives exhibit robust performance even in elevated temperatures, making them suitable for applications in automotive engine compartments, aerospace propulsion systems, and electronics where heat dissipation is essential.
Chemical Protection: Component Epoxy Adhesives engineered with solid chemical resistance are ideal for industries handling corrosive agents, acids, and chemicals. They ensure long-lasting bonds in chemical processing equipment, laboratory setups, and chemical storage facilities.
Electronic Reliability: In the electronics industry, these adhesives offer heat resistance and electrical insulation properties, making them vital for bonding components subjected to elevated temperatures during operation, such as power modules and circuit boards.
Preventing Oxidation: Epoxy adhesives with heat resistance help prevent surface oxidation and degradation, enhancing bonded materials’ longevity and performance in applications ranging from aerospace components to industrial machinery.
Flexibility and Strength: Some One Component Epoxy Adhesives maintain their mechanical properties even at high temperatures, striking a balance between heat resistance and structural integrity. Automotive exhaust systems and industrial machinery experience mechanical stresses and temperature fluctuations, making these materials suitable.
However, it’s crucial to consider potential limitations:
Temperature Thresholds: While these adhesives offer heat resistance, prolonged exposure to extremely high temperatures might lead to some degradation. Ensuring that the selected bond meets the application’s temperature requirements is essential.
Chemical Compatibility: While many One Component Epoxy Adhesives exhibit chemical resistance, verifying compatibility with specific chemicals in the intended environment is vital, especially in industries involving aggressive solvents or reactive agents.
Curing and Handling Conditions: Achieving optimal heat and chemical resistance properties requires proper curing and handling during application. Deviations from recommended procedures can affect the final performance of the adhesive.
Electrical Insulation Properties
One Component Epoxy Adhesives exhibit notable electrical insulation properties that make them valuable for various electronic and electrical applications. These adhesives offer a combination of adhesive strength and electrical insulating characteristics, contributing to the performance and reliability of electronic devices and components.
Dielectric Strength: One Component Epoxy Adhesives are known for their high dielectric strength, which means they can withstand significant electric fields without breaking down. “This property is crucial for preventing electrical leakage and short circuits, especially in devices with closely spaced components.
Surface Insulation: These adhesives create an effective insulation layer on surfaces, preventing direct contact between conductive elements and reducing the risk of unintentional electrical pathways. Ensuring this in tightly packed circuitry is crucial.
Protection Against Environmental Factors: One Component Epoxy Adhesives can provide a barrier against moisture, chemicals, and contaminants that could compromise the electrical performance of components. This protective layer contributes to the longevity of electronic devices.
Thermal Stability: Many electronic applications involve heat-generating components. Epoxy adhesives with high thermal stability ensure that electrical insulation properties are maintained even under elevated temperatures, preventing insulation breakdown.
Customizable Properties: Depending on the application’s specific requirements, you can tailor the electrical insulation properties of One Component Epoxy Adhesives by selecting different formulations. Engineers can choose adhesives that meet their devices’ electrical requirements.
Adhesion to Various Substrates: These adhesives can bond to various substrates commonly used in electronics, such as metals, ceramics, and plastics. This versatility in substrate compatibility ensures consistent electrical insulation across diverse components.
However, it’s essential to consider potential limitations:
Thermal Conductivity: While One Component Epoxy Adhesives provide excellent electrical insulation, their thermal conductivity might be lower than other materials. In applications where efficient heat dissipation is crucial, careful consideration requires.
Curing and Handling: Achieving optimal electrical insulation properties requires proper adhesive curing. Curing or adequate handling could lead to compromised insulation performance.
Testing and Validation: In critical electronic applications, thorough testing and validation are necessary to ensure that the selected adhesive meets the required electrical insulation standards and reliability.
One Component Epoxy for Electronics
The demand for reliable and efficient bonding solutions is paramount in the rapidly evolving electronics landscape. One component epoxy adhesives have emerged as a versatile and indispensable option for various electronics applications. Unlike traditional two-component epoxies that require mixing before application, one component epoxies come pre-formulated and ready to use, simplifying the bonding process and enhancing productivity.
Advantages of One Component Epoxy for Electronics
- Simplicity and Convenience:
One epoxy adhesive component eliminates the need for mixing and precise ratio measurements, streamlining the assembly process. This simplicity reduces human error and accelerates production timelines, making it a go-to choice for high-volume manufacturing.
- Rapid Curing:
When exposed to heat or other curing mechanisms, these epoxies often exhibit fast curing times. This rapid cure contributes to shorter production cycles, allowing manufacturers to meet tight deadlines without compromising bond strength or performance.
- Exceptional Bonding Performance:
One component epoxy adhesives deliver robust bonding performance with high shear and peel strength, ensuring reliable connections between delicate electronic components. The adhesive’s exceptional thermal and electrical conductivity properties improve overall performance.
Applications in Electronics Industry
- Surface Mount Device (SMD) Attachment:
One component epoxies find extensive use in attaching surface mount devices to circuit boards. Their precise dispensing capabilities and rapid curing characteristics ensure secure, lasting bonds even in miniaturized components.
- Potting and Encapsulation:
These epoxies protect sensitive electronics from environmental factors like moisture, dust, and vibration in potting and encapsulation. Their ability to encapsulate components while maintaining electrical integrity is crucial for extending the lifespan of electronic devices.
- Cable and Connector Bonding:
The flexibility of one component epoxy adhesives makes them ideal for bonding cables and connectors. They offer high adhesion to a wide range of materials, enhancing the durability and reliability of interconnections.
Aerospace and Automotive Applications
One Component Epoxy Adhesives have found significant utility and interest within aerospace and automotive applications, offering streamlined adhesive solutions for various bonding needs. In these industries, where reliability, durability, and performance are paramount, these adhesives have distinct advantages but also face notable considerations.
Structural Bonding: Component Epoxy Adhesives are vital in aerospace and automotive applications by providing strong and durable bonds for structural components. Their ability to distribute stress evenly across bonded joints contributes to enhanced load-bearing capacity, which is critical for ensuring the integrity of aircraft and vehicle structures.
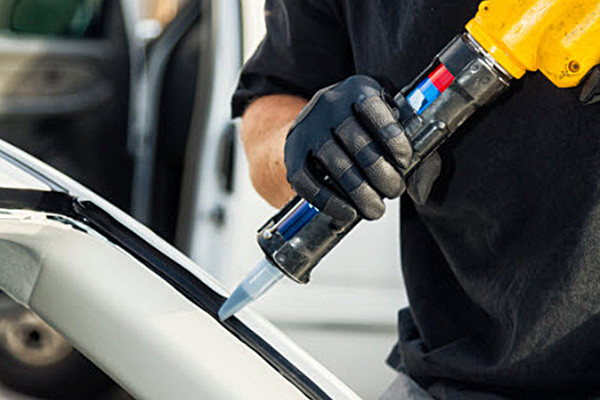
Weight Reduction: The lightweight nature of epoxy adhesives aligns with the aerospace and automotive industries’ ongoing efforts to minimize weight and improve fuel efficiency. By replacing traditional mechanical fasteners, these adhesives help achieve weight reduction without compromising structural integrity.
Complex Geometries: Aerospace and automotive components often feature intricate and complex geometries. One Component Epoxy Adhesives offer an advantage in reaching difficult-to-access areas where mechanical fasteners might be impractical, allowing for seamless bonding even in challenging shapes and spaces.
Vibration Damping: Vibrations and dynamic loads are common challenges in both industries. Epoxy adhesives exhibit excellent vibration-damping properties, which can lead to improved fatigue resistance and extended component lifespan.
Corrosion Resistance: Aerospace and automotive applications often expose components to harsh environments, including exposure to moisture and chemicals. Epoxy adhesives can provide a protective barrier against corrosion, contributing to the longevity of the bonded structures.
Time Efficiency: Component Epoxy Adhesives simplify assembly processes, reducing the need for extensive mixing and eliminating the potential for mixing errors. This time efficiency is especially valuable in industries where production timelines are crucial.
However, certain limitations and considerations also apply:
Curing Conditions: Aerospace and automotive applications can involve varying temperatures and environmental conditions. Component Epoxy Adhesives might require careful consideration of curing conditions to ensure proper bonding and performance.
Temperature Resistance: While epoxy adhesives are generally known for their temperature resistance, some formulations might have limitations in extreme conditions. Selecting bonds that can withstand the specific temperature ranges within these industries is vital.
Testing and Certification: Aerospace and automotive components often require stringent testing and certification to meet safety and regulatory standards. Adhesive selection must align with these requirements, necessitating thorough testing and validation processes.
Medical Device Assembly
In the intricate world of medical device assembly, where precision and reliability are paramount, the role of one component of epoxy adhesives emerges as a game-changer. These specialized adhesives offer a unique solution for bonding various components within medical devices, ensuring seamless integration and robust performance. From implantable devices to diagnostic tools, using one-component epoxy adhesives enhances the quality and longevity of medical equipment while adhering to stringent healthcare standards.
Advantages of Medical Device Assembly
- Simplified Application Process:
One component epoxy adhesives streamline the assembly process with their ready-to-use formulation, eliminating the need for intricate mixing and ratio measurements. This simplicity reduces the risk of human error during assembly while accelerating production timelines, which is crucial in the fast-paced world of healthcare.
- Precision and Bond Strength:
Medical devices demand precise bonding to ensure components stay securely attached over the device’s lifespan. One epoxy adhesive component offers exceptional adhesion properties, creating solid and durable bonds that withstand the rigors of medical applications, including bodily fluids, mechanical stress, and temperature fluctuations.
- Biocompatibility and Safety:
Medical devices that come into direct contact with the human body must meet strict biocompatibility standards. One component epoxy adhesives explicitly developed for medical use are designed to be biocompatible, ensuring they do not elicit adverse reactions or compromise patient safety.
Applications in Medical Device Assembly
- Implantable Medical Devices:
Implantable devices, such as pacemakers, neural stimulators, and drug delivery systems, require precise and secure assembly to function optimally within the body. One epoxy adhesive component offers the necessary combination of strength and biocompatibility to ensure these devices remain intact and effective.
- Diagnostic and Monitoring Equipment:
Medical diagnostic tools, ranging from blood glucose monitors to imaging devices, rely on precise alignment and bonding of sensitive components. One component, epoxy adhesives, provide the reliability needed for accurate measurements and imaging, contributing to improved diagnoses and patient care.
- Wearable Medical Devices:
The rise of wearable medical devices, including wearable monitors and drug delivery patches, introduces the need for adhesive solutions that adhere securely to both the device and the patient’s skin. One epoxy adhesive component fulfills this requirement, providing strong adhesion without causing discomfort or skin irritation.
Construction and Infrastructure Bonding
Using one component of epoxy adhesives has emerged as a key factor in achieving unparalleled bonding strength and durability in construction and infrastructure. These specialized adhesives offer a versatile solution for joining diverse materials in projects ranging from towering skyscrapers to intricate transportation networks.
Simplified Application: With their pre-formulated composition, one component epoxy adhesives eliminate the complexities of mixing, streamlining the bonding process and reducing the potential for errors during construction.
Structural Integrity Reinforcement: These adhesives provide robust bonding that reinforces the structural integrity of construction elements, such as concrete, metal, and composites, ensuring longevity and load-bearing capability.
Resilience against Environmental Challenges: One component of epoxy adhesives demonstrates exceptional resistance to environmental factors such as moisture, temperature variations, and chemical exposure. This feature safeguards constructions against premature deterioration.
Ideal for Dynamic Loads: Structures subjected to dynamic loads, such as bridges and high-rise buildings, benefit from the fatigue resistance and stability these adhesives offer, enhancing their lifespan.
In the evolving landscape of construction and infrastructure, specific trends and considerations are shaping the application of one component of epoxy adhesives:
Sustainable Construction: These adhesives align with sustainability goals by minimizing waste, as they are ready to use without excess mixing components. Additionally, some formulations are environmentally friendly, contributing to greener construction practices.
Rapid Curing and Efficiency: The fast curing times of one component epoxy adhesives expedite construction timelines, allowing for quicker project completion without compromising bond strength.
Advanced Bonding Solutions: As construction designs become more intricate and materials more diverse, the versatility of one component epoxy adhesives makes them an essential tool for achieving reliable and durable connections.
Integrating one component epoxy adhesives into construction and infrastructure projects demonstrates their pivotal role in fostering strength, durability, and efficiency. As the industry evolves, these adhesives continue to empower engineers and builders to construct resilient structures that withstand the challenges of time and the environment.
Dispensing Techniques for Precision
The successful application of one component epoxy adhesives hinges upon the precision of dispensing techniques, as it directly impacts bonding quality, product durability, and overall process efficiency. In manufacturing, electronics, and aerospace, where reliable and strong bonds are paramount, several specialized dispensing techniques have emerged to achieve unparalleled precision.
Micro-Dispensing: This technique involves the controlled deposition of tiny quantities of epoxy adhesive. With fine nozzles and advanced dispensing equipment, micro-dispensing allows for intricate and delicate adhesive application. It’s ideal for applications requiring precision on miniature scales or when dealing with sensitive substrates, minimizing material waste and maximizing accuracy.
Jetting Systems: Jetting systems utilize pressurized air bursts to propel tiny adhesive droplets onto the substrate. These systems benefit high-speed production environments where quick and accurate adhesive application is essential. Jetting systems can handle various adhesive viscosities and offer consistent results, making them valuable for multiple industries.
Augmented Reality (AR) Assisted Dispensing: The integration of augmented reality technology into dispensing systems has revolutionized precision. By projecting virtual adhesive patterns onto substrates, operators can follow exact guidelines for adhesive application. AR-assisted dispensing minimizes human error, enhances accuracy, and speeds up the overall process.
Automated Robotic Dispensing: In scenarios involving intricate patterns or large-scale production, automated robotic dispensing systems shine. These systems can be programmed to follow predetermined paths, ensuring consistent adhesive application across various components. The accuracy and repeatability of robotic dispensing minimize variations and improve overall product quality.
The choice of dispensing technique depends on factors such as adhesive viscosity, substrate material, pattern complexity, and production volume. However, regardless of the specific method chosen, precision in adhesive dispensing yields numerous benefits:
- Enhanced bond strength and durability
- Reduced material waste and costs
- Improved product consistency and quality
- Increased production efficiency
- Minimized rework and debris due to accurate application
Quality Control and Testing Standards
Precision is inseparable from quality in adhesive application, making dispensing techniques a pivotal factor. One component epoxy adhesives find extensive use in critical industries such as electronics, aerospace, and automotive, necessitating stringent quality control and testing standards to ensure optimal performance and reliability.
Dispensing Techniques for Precision:
Micro-Dispensing: Micro-dispensing, enabled by fine nozzles and specialized equipment, allows for the deposition of minute amounts of epoxy adhesive with exceptional accuracy. This technique excels in delicate applications and intricate patterns.
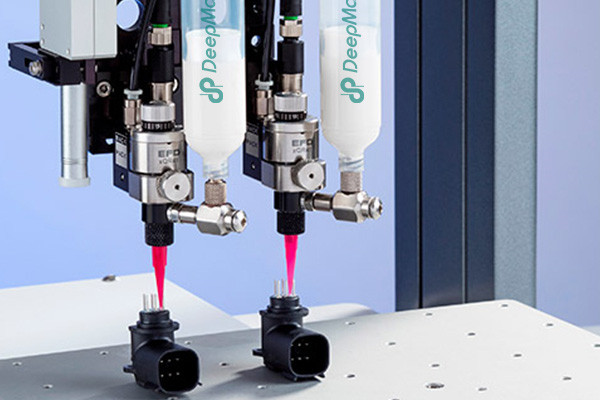
Jetting Systems: Ideal for high-speed production lines, jetting systems use compressed air bursts to propel tiny adhesive droplets onto substrates, ensuring rapid yet precise application.
Augmented Reality (AR) Assisted Dispensing: Augmented reality integration projects virtual adhesive patterns onto substrates, aiding operators in adhering to precise guidelines and minimizing human error.
Automated Robotic Dispensing: Automated systems offer consistency and accuracy by following predefined paths, making them suitable for complex patterns and large-scale production.
Quality Control and Testing Standards:
Adhesive Formulation Integrity: Thorough evaluation of adhesive composition and properties ensures consistency and reliability in bonding performance.
Viscosity Control: Maintaining optimal adhesive viscosity guarantees uniform dispensing and adherence to substrates.
Bond Strength Testing: Mechanical testing assesses the adhesive’s ability to withstand stress, providing insights into its long-term durability.
Thermal Performance Testing: Subjecting bonded samples to extreme temperatures assesses the adhesive’s resistance to thermal cycling.
Environmental Testing: Exposure to humidity, chemicals, and UV radiation gauges the adhesive’s resilience in real-world conditions.
Dimensional Stability: Monitoring changes in adhesive dimensions over time ensures its suitability for applications with strict dimensional requirements.
Stricter quality control and testing standards ensure adhesive reliability and impact product performance and end-user satisfaction. Adhering to these standards brings forth benefits such as:
- Enhanced bond integrity and longevity
- Reduced risk of material or process-related failures
- Improved consistency across production batches
- Cost savings by preventing rework and potential recalls
- Strengthened competitive advantage through superior product reliability
Curing Mechanisms in One Component Epoxies
One component epoxy adhesives are renowned for their robust bonding properties and versatility, owing much of their success to the intricate curing mechanisms that drive their transformation from a viscous liquid to a strong, durable bond. These curing mechanisms are essential to achieve optimal performance and ensure the adhesive’s suitability for various industry applications.
Chemical Crosslinking: One component of epoxy adhesives often contains latent curing agents that react with heat or moisture to initiate a chemical crosslinking process. This crosslinking forms a three-dimensional network within the adhesive, providing mechanical strength and thermal stability to the bond. Curing agents such as aromatic amines or anhydrides can vary, allowing tailored performance characteristics.
Heat Activation: Thermal curing is a common mechanism where heat accelerates the reaction between the epoxy resin and the curing agent. This approach is well-suited for applications where industries can easily control heat, such as in industrial settings. The process allows precise control over the curing rate and final bond properties.
Moisture Cure: Moisture-curable one component epoxies rely on atmospheric moisture to initiate the curing process. The adhesive absorbs water vapor from the environment, reacting with the curing agent to trigger polymerization. This mechanism is advantageous for applications where heat curing is impractical.
UV or Light Cure: Some one component epoxy adhesives incorporate photo-initiators that remain dormant until exposed to specific wavelengths of UV or visible light. When exposed, these initiators generate free radicals that initiate the polymerization process. UV or light curing provides rapid and precise bonding in applications that require minimal heat or moisture.
Anaerobic Cure: Anaerobic one component epoxy adhesives cure without oxygen. They remain liquid until confined between close-fitting surfaces, where the absence of oxygen triggers polymerization. Many often utilize this mechanism for thread locking and sealing applications.
Environmental Considerations and Sustainability
As industries increasingly emphasize sustainability, the environmental impact of adhesive technologies, including one component of epoxy adhesives, has come under scrutiny. While manufacturers utilize these adhesives to achieve exceptional bonding performance, they must address several vital environmental considerations to ensure compatibility with eco-friendly practices and regulatory requirements.
Raw Materials Selection: Opting for eco-friendly and renewable raw materials in epoxy adhesive formulations can significantly reduce the environmental footprint of production. Choosing bio-based resins and curing agents can mitigate the use of fossil fuels and decrease greenhouse gas emissions.
Reduced VOC Emissions: Volatile organic compounds (VOCs) released during adhesive application can contribute to air pollution and health risks. Formulating one component epoxy adhesives with low VOC content or developing VOC-free alternatives helps minimize these negative impacts.
End-of-Life Disposal: Epoxy adhesives can pose challenges during disposal, as they often form solid and persistent bonds that resist degradation. Considering the adhesive’s disassembly or removal at the end of a product’s life cycle is crucial to facilitate recycling or proper disposal.
Energy Efficiency: Manufacturing processes for epoxy adhesives require energy-intensive curing steps. Implementing energy-efficient techniques like UV or light curing can reduce energy consumption and operational costs.
Biodegradability: Developing epoxy adhesives designed to break down over time in natural environments can limit their long-term environmental impact. Biodegradable formulations ensure that the adhesive does not persist indefinitely in the ecosystem.
Life Cycle Assessment (LCA): Conducting comprehensive LCAs helps evaluate the overall environmental impact of one component of epoxy adhesives, from raw material extraction to manufacturing, application, and disposal. This assessment aids in identifying areas for improvement and guiding sustainable practices.
Balancing the performance requirements of one component epoxy adhesives with environmental considerations presents a complex challenge. However, addressing these considerations can lead to numerous benefits:
Regulatory Compliance: Meeting evolving environmental regulations and standards ensures the continued marketability of adhesive products.
Enhanced Reputation: Embracing sustainability enhances a company’s image and fosters positive relationships with environmentally conscious customers.
Resource Efficiency: Using renewable materials and minimizing waste contributes to efficient resource utilization and cost savings.
Long-Term Viability: Developing environmentally friendly adhesives positions manufacturers for long-term success in a rapidly changing marketplace.
Benefits in Production Efficiency
One Component Epoxy Adhesives has emerged as a game-changer in adhesive technology, revolutionizing production processes across various industries. Manufacturers design these advanced adhesives to streamline manufacturing operations while delivering exceptional bonding performance. A host of benefits accompany the utilization of One Component Epoxy Adhesives, making them an indispensable tool for enhancing production efficiency:
Time Savings: Component Epoxy Adhesives eliminate the need for mixing multiple components, as they come pre-formulated and ready to use. They are eliminating the time-consuming process of measuring and mixing leads to faster assembly and shorter production cycles.
Reduced Labor Costs: The simplicity of application associated with One Component Epoxy Adhesives minimizes the skill level required for adhesive application. As a result, significant cost savings are achieved by reducing training expenses and relying on highly skilled labor.
Increased Throughput: With faster curing times and a reduced need for clamping or fixturing, production lines can operate at higher speeds, boosting overall throughput. Manufacturers can achieve greater output without compromising bond quality.
Enhanced Bonding Performance: Despite being single-component, these adhesives offer exceptional bond strength, durability, and resistance to various environmental factors. Such an approach ensures reliable, long-lasting bonds that significantly contribute to the overall quality of the end product.
Improved Design Flexibility: One Component Epoxy Adhesives adhere effectively to various substrates, including metals, plastics, ceramics, and composites. This versatility allows designers to explore new material combinations and optimize product performance without concerns about adhesive compatibility.
Space and Inventory Savings: Eliminating mixing stations and reducing storage requirements for multiple components free up valuable floor space and reduce inventory management complexities. This streamlined approach leads to a more organized and efficient production environment.
Minimized Waste: Traditional two-component adhesives often produce excess material waste due to inaccurate mixing ratios or unused mixed bonds. Component Epoxy Adhesives eliminate such waste, contributing to a greener manufacturing process.
Compatibility with Different Substrates
In the realm of adhesive technology, One Component Epoxy Adhesives have achieved acclaim for their unparalleled compatibility with a diverse range of substrates. This exceptional characteristic has elevated them as a staple in various industries, offering a versatile solution for bonding challenges. The ability of these adhesives to seamlessly adhere to different materials expands the realm of design possibilities, manufacturing efficiencies, and application potential. The following key points underscore the remarkable substrate compatibility of One Component Epoxy Adhesives:
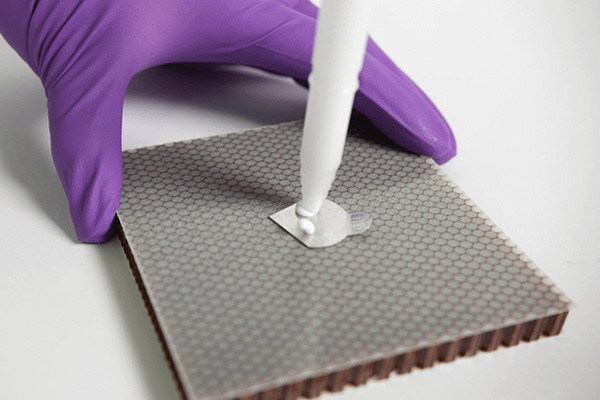
Broad Material Adhesion: Component Epoxy Adhesives demonstrate remarkable adhesion capabilities across an extensive spectrum of substrates, encompassing metals, plastics, ceramics, composites, and more. This wide-ranging compatibility eliminates concerns about material interactions and promotes cross-material bonding, enabling innovative designs and novel material combinations.
Metal Versatility: These adhesives establish robust bonds with various metals, contributing to the structural integrity of assemblies. Their compatibility with metals, including aluminum, stainless steel, and copper, is instrumental in industries where diverse metal bonding is integral, such as automotive, construction, and electronics.
Plastic and Composite Affinity: Component Epoxy Adhesives foster dependable adhesion to numerous plastics and composites, creating lightweight yet resilient structures. This property is advantageous in sectors prioritizing weight reduction without compromising mechanical strength, such as aviation, consumer goods, and renewable energy.
Ceramic and Glass Adhesion: These adhesives’ ability to adhere to ceramics and glass facilitates advancements in specialized industries, including electronics, optics, and medical devices. The compatibility with brittle materials enables the secure bonding of delicate components without compromising their intrinsic fragility.
Harsh Environment Endurance: Component Epoxy Adhesives resist harsh conditions, including chemicals, extreme temperatures, and moisture. The compatibility across diverse substrates ensures that bonded assemblies maintain their integrity in demanding operating environments, contributing to the longevity of end products.
Electrical Insulation Properties: These adhesives often exhibit excellent electrical insulation properties by leveraging their compatibility with various substrates. This feature is invaluable in applications where preventing electrical conductivity between components is essential, such as electronics manufacturing and electrical engineering.
Innovative Applications of One Component Epoxies
One Component Epoxies have emerged as a driving force behind innovation, reshaping possibilities across many industries. With their unique formulation and remarkable properties, these adhesives have paved the way for groundbreaking applications that were once deemed challenging or unattainable. The versatility and performance of One Component Epoxies open doors to novel solutions, enabling engineers and designers to push the boundaries of traditional thinking. The following points illuminate the transformative role of One Component Epoxies in pioneering new applications:
Electronics Miniaturization: One Component Epoxies find themselves at the heart of modern electronics manufacturing, supporting the trend of miniaturization by providing precise bonding in microelectronic assemblies. Their compatibility with delicate substrates and excellent electrical insulation properties ensure reliable connections in densely packed devices.
Medical Device Advancements: These adhesives play a pivotal role in the medical industry, facilitating the assembly of intricate medical devices and ensuring biocompatibility. Their compatibility with various materials allows for the secure bonding of medical components, from surgical instruments to wearable health tech.
Automotive Lightweighting: One Component Epoxies contribute to the ongoing pursuit of lightweight in the automotive sector. By bonding dissimilar materials such as metals and composites, they enable the construction of structurally efficient yet lightweight components, enhancing fuel efficiency and vehicle performance.
Renewable Energy Solutions: In renewable energy applications, such as wind turbine blade manufacturing and solar panel assembly, One Component Epoxies provide exceptional bonding strength that endures extreme weather conditions. Their compatibility with diverse substrates supports the durability of these energy systems.
Aerospace Innovations: Aerospace engineers utilize One Component Epoxies for aircraft assembly, offering high-strength bonds in challenging environments. Their compatibility with materials used in aerospace manufacturing ensures the integrity of components subjected to high stress and varying temperatures.
Consumer Electronics: The trend toward sleek, compact consumer electronics relies on One Component Epoxies for secure bonding in space-constrained designs. Their compatibility with plastics, metals, and glass ensures the durability of devices while maintaining their aesthetic appeal.
Optics and Photonics: Component Epoxies facilitate the precise assembly of optical components, ensuring accurate alignment and minimal distortion. Their compatibility with glass and ceramics is crucial in fiber optics, lasers, and imaging systems.
Future Trends in Epoxy Adhesive Technology
Several compelling trends are shaping the future landscape of epoxy adhesive technology, positioning it for transformative evolution. As industries seek superior bonding solutions, epoxy adhesives are ready to respond with innovations that tackle emerging challenges and opportunities. The following bullet points highlight the key trends that experts expect to drive the evolution of epoxy adhesive technology:
Sustainability and Green Chemistry: The future of epoxy adhesives will see a heightened focus on sustainable formulations and manufacturing processes. Researchers are exploring bio-based epoxy resins derived from renewable sources, reducing reliance on petrochemicals. Green chemistry principles will guide the development of adhesives with reduced environmental impact and improved end-of-life disposal.
Innovative and Functional Adhesives: Epoxy adhesives are poised to become more than bonding agents. Future formulations will integrate functional properties, such as self-healing capabilities and thermal and electrical conductivity. These innovative adhesives will enhance product performance and open doors for electronics, aerospace, and healthcare applications.
Nanotechnology Integration: Nanoparticles and nanomaterials are expected to play a pivotal role in epoxy adhesive technology. Incorporating nanoparticles can impart improved mechanical properties, enhanced adhesion, and tailored functionalities to epoxy formulations. Nanotechnology will drive advancements in lightweight materials, wear resistance, and flame retardancy.
Customization and 3D Printing: The advent of 3D printing has already started influencing epoxy adhesive technology. In the future, epoxy adhesives will be tailored for compatibility with 3D printing processes, allowing for intricate and customized designs in various industries. By enabling rapid prototyping, efficient manufacturing, and the creation of complex geometries, this will help streamline the production process.
Health and Safety Innovations: Epoxy adhesive formulations will increasingly prioritize user safety and health. Low-volatile organic compound (VOC) and low-odor formulations will gain prominence, catering to indoor applications and reducing health risks for workers. Advances in epoxy curing mechanisms will also lead to formulations with reduced allergenic potential.
Digitalization and Data-Driven Development: Integrating digital tools, simulations, and data analytics will streamline the development and optimization of epoxy adhesive formulations. Computer-aided design (CAD) and machine learning algorithms will aid in predicting clingy behavior, optimizing formulations, and accelerating research and development cycles.
Challenges and Limitations of One Component Formulations
While offering a simplified adhesive solution, One Component Epoxy Adhesives come with challenges and limitations that industries must navigate for successful application.
Curing Time Variability: Component Epoxy Adhesives rely on chemical reactions for curing, and factors such as temperature, humidity, and surface conditions can lead to variations in curing time. Consistent bonding results may be difficult to achieve in varying environments, presenting challenges.
Incomplete Curing: Inadequate curing can lead to reduced adhesive strength and compromised bond integrity, especially in complex geometries or areas that are difficult to access. A significant limitation is ensuring thorough and uniform curing throughout the adhesive joint.
Limited Pot Life: Component Epoxy Adhesives often have a little pot life after dispensing. Use the adhesive within a specific time frame for successful bonding. Please do so to save materials.
Substrate Compatibility: Achieving strong bonds requires proper adhesion to various substrates. Component Epoxy Adhesives may have limitations in terms of substrate compatibility, necessitating thorough testing to ensure successful bonding across different materials.
Temperature Sensitivity: Some one-component epoxy formulations can be sensitive to temperature fluctuations during storage and transportation, impacting their stability and performance. Take special care to store and handle these adhesives within recommended temperature ranges.
Mechanical Properties: While one-component epoxy adhesives offer convenience, they might only sometimes match the mechanical properties of two-component systems. Trade-offs in performance characteristics such as bond strength and flexibility can occur.
Limited Customization: Component Epoxy Adhesives might have limitations in terms of customization based on specific application requirements. Unlike two-component systems, which allow for adjusting ratios for optimal performance, one-component adhesives might offer extra flexibility.
Quality Control Challenges: Monitoring the curing process and ensuring consistent adhesive performance can be challenging with one-component formulations. The lack of real-time control over the curing reaction might require advanced monitoring techniques to maintain quality standards.
One component epoxy adhesives represent a shift towards simplicity without compromising on strength and reliability. Their role in simplifying bonding processes while providing robust adhesion is pivotal in industries that value efficiency and performance. As technology advances and industries seek innovative ways to streamline manufacturing, one component epoxy adhesives will remain at the forefront of driving innovation and efficiency. With ongoing research and improvements, these adhesives are poised to shape the future of adhesive technology, contributing to the creation of products that seamlessly integrate high-strength bonding solutions into various applications.