Electric Appliance Adhesive
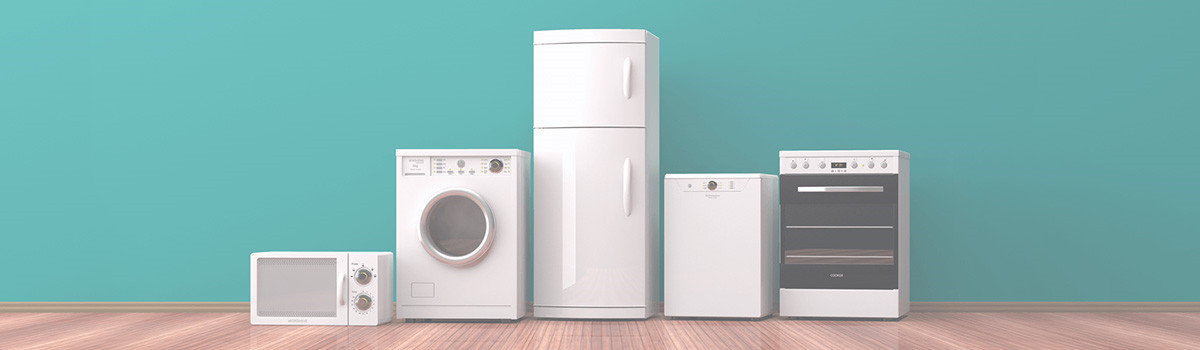
In today’s fast-paced technological landscape, electric appliances play an indispensable role in our daily lives. Behind the seamless designs and intricate mechanisms of these devices lies a crucial element that holds them together – electric appliance adhesives. These specialized adhesives ensure the durability, safety, and functionality of various electronic devices. In this comprehensive guide, we will delve into the world of electric appliance adhesives, highlighting their significance and applications across a range of industries.
Understanding Electric Appliance Adhesives
Electric appliance adhesives represent a specialized class of bonding agents designed to address the unique challenges posed by electronic devices. Engineers have designed these formulations, unlike traditional adhesives, to deliver mechanical solid bonds, exceptional electrical conductivity, thermal stability, and compatibility with delicate components. These adhesives are the backbone of various devices, including smartphones, laptops, televisions, medical equipment, and automotive electronics.
The primary objective of electric appliance adhesives is to ensure the reliable and long-lasting attachment of components within electronic devices. They facilitate the secure bonding of intricate and often miniature components such as integrated circuits (ICs), resistors, capacitors, and sensors onto substrates like printed circuit boards (PCBs). Unlike mechanical fasteners, adhesives distribute stress uniformly across surfaces, reducing the risk of damage due to localized pressure points.
Another critical aspect of electric appliance adhesives is their electrical conductivity. Engineers use conductive adhesives to establish low-resistance pathways between components in applications where electrical connections are crucial, such as in PCBs. Ensuring uninterrupted electric current flow helps maintain the functionality of the device. Furthermore, these adhesives enable heat dissipation by creating a thermal path between components and heat sinks, preventing overheating and ensuring optimal performance.
Factors such as the materials requiring bonding, operating conditions, and manufacturing processes determine the selection of the appropriate adhesive type. Epoxies, silicones, polyurethanes, and acrylics are typical adhesive families used for electric appliances, each offering distinct advantages based on their properties.
Key Properties and Characteristics
Electric appliance adhesives ensure electronic devices’ integrity, safety, and performance. Designers have engineered these adhesives to deliver robust and reliable bonding in the demanding conditions that electrical equipment often faces. Their key properties and characteristics can be summarized as follows:
Electrical Insulation
- Formulators create electric appliance adhesives to provide excellent electrical insulation properties, preventing the flow of electricity between components.
- They minimize the risk of short circuits, sparks, and potential electrical hazards by maintaining high dielectric strength.
Thermal Conductivity
- Many electric appliances generate heat during operation. Adhesives with good thermal conductivity efficiently dissipate heat, preventing overheating and potential damage.
- Thermal management properties help extend the lifespan of components and maintain performance efficiency.
Chemical Resistance
- Electric appliance adhesives often come into contact with various chemicals, including cleaning agents and solvents. They resist these substances, maintaining their bond strength and structural integrity.
Mechanical Strength
- The adhesives provide robust mechanical bonding, enhancing the overall stability of the components and preventing dislodging due to vibrations or shocks.
- They offer excellent shear, peel, and tensile strength, ensuring long-lasting adhesion under stress.
Environmental Durability
- Designers engineer adhesives for use in electric appliances to withstand challenging environmental conditions, such as humidity, temperature fluctuations, and exposure to UV radiation.
- They resist degradation and maintain their properties over time, contributing to the appliance’s reliability.
Low Outgassing
- Electric appliance adhesives are engineered with low outgassing properties, minimizing the release of volatile compounds that could interfere with sensitive electronic components.
Fast Cure Times
- Many adhesive formulations offer rapid curing, reducing assembly time and increasing production efficiency.
- Quick curing also aids in achieving a solid bond quickly, minimizing the risk of contamination during the bonding process.
Compatibility
- Formulators create adhesives to ensure compatibility with various substrates commonly found in electric appliances, including metals, plastics, ceramics, and glass.
- Compatibility ensures reliable adhesion between different materials used in the assembly of the appliance.
Regulatory Compliance
- Electric appliance adhesives often adhere to industry-specific regulations and standards, ensuring the final product meets safety and performance requirements.
- Compliance contributes to the overall quality and safety of the electronic device or appliance.
Electric appliance adhesives exhibit various crucial properties for ensuring electronic devices and appliances’ proper functioning, safety, and longevity. These characteristics together enhance the overall efficiency and reliability of the products companies use.
Importance of Bonding in Electronic Devices
Bonding is a critical aspect of electronic device manufacturing, which is indispensable in ensuring the functionality, durability, and safety of various components and assemblies. Electric appliance adhesives, specifically engineered for these applications, have emerged as crucial solutions that address the intricate bonding requirements of electronic devices. The significance of bonding in electronic devices is multifaceted and encompasses several vital subheadings:
Structural Integrity and Reliability
Electronic devices comprise intricate arrangements of components, each with specific functions. Reliable bonding ensures that these components remain securely attached, maintaining the structural integrity of the device. Whether it’s the attachment of circuit boards, sensors, connectors, or other features, the strength and durability of the bond are paramount to prevent premature failures or malfunctions.
Thermal Management
Modern electronic devices often generate heat during operation, leading to performance degradation or even catastrophic failures if not properly managed. Electric appliance adhesives with excellent thermal conductivity facilitate efficient heat transfer from hotspots to heat sinks or other dissipative elements. This property helps maintain optimal operating temperatures, extending the lifespan and ensuring consistent performance of the device.
Electrical Insulation
Electrical insulation is essential in electronic devices where different components operate at varying voltage levels to prevent short circuits, sparks, and potential hazards. Electric appliance adhesives with high dielectric strength act as insulating barriers, safeguarding against unintended electrical connections and ensuring the safe operation of the device.
Vibration and Shock Resistance
Electronic devices often encounter mechanical stresses such as vibrations and shocks, especially in portable and automotive gadgets. Strong bonding provided by electric appliance adhesives prevents components from dislodging due to these stresses, enhancing the device’s reliability and longevity.
Miniaturization and Design Flexibility
The trend toward smaller, sleeker electronic devices demands innovative bonding solutions. Electric appliance adhesives offer design flexibility by enabling secure bonding even in tight spaces and intricate geometries, allowing manufacturers to create compact and aesthetically appealing products without compromising performance.
Environmental Protection
Diverse environmental conditions, including humidity, temperature fluctuations, and chemical exposure, affect electronic devices. Electric appliance adhesives offer protection against these factors, shielding sensitive components and preventing their degradation over time.
Streamlined Manufacturing Processes
Electric appliance adhesives often possess fast cure times and compatibility with various substrates, which streamline manufacturing processes. Quick curing accelerates production, while compatibility with different materials reduces the need for multiple adhesives, simplifying assembly.
Types of Electric Appliance Adhesives
Electric appliance adhesives encompass various formulations designed to cater to the unique bonding requirements of electronic devices and appliances. These adhesives are essential for ensuring components’ structural integrity, thermal management, and electrical insulation. Here are some key types of electric appliance adhesives:
- Thermally Conductive Adhesives:Engineers design these adhesives to efficiently dissipate heat, making them ideal for devices like LED assemblies and power modules that generate heat during operation. They help maintain optimal operating temperatures and prevent overheating.
- Electrically Insulating Adhesives:These adhesives strongly bond while insulating against electrical currents.” They are vital for preventing short circuits and ensuring safety in devices with closely spaced components, such as circuit boards.
- Flexible Adhesives and Sealants:These adhesives are designed for flexible electronics and devices prone to mechanical stress, accommodating movements and vibrations. They prevent cracks and failures in components that experience bending or flexing.
- Conformal Coatings:These thin protective coatings shield devices from moisture, chemicals, and dust. They provide uniform coverage, even on intricate components, making them suitable for PCBs, sensors, and outdoor appliances.
- UV-Curable Adhesives:These adhesives cure rapidly under UV light, making them suitable for fast assembly processes. Applications like optical bonding and touchscreen assembly utilize them.
- Low Outgassing Adhesives:These adhesives release minimal volatile compounds, which is crucial for space, aerospace, and vacuum applications. They prevent contamination and maintain device performance.
- High-Temperature Resistant Adhesives:Engineers have designed these adhesives to withstand elevated temperatures for use in devices that operate in high-heat environments, such as automotive engine compartments.
- Electrically Conductive Adhesives:These adhesives combine bonding with electrical conductivity when used for applications like attaching electronic components and EMI shielding.
- Low-VOC Adhesives:These adhesives contain reduced VOC content, which renders them environmentally friendly and suitable for devices that require minimized emissions.
The diverse types of electric appliance adhesives play a vital role in meeting the complex bonding needs of electronic devices, ensuring their functionality, longevity, and safety in various industries.
Conductive Adhesives for Electrical Connections
Electric appliances have become indispensable to modern life, demanding innovative solutions to ensure reliable and efficient electrical connections within their intricate designs. Conductive adhesives have emerged as a groundbreaking technology in electric appliance adhesive, revolutionizing electrical connections. These adhesives offer solid and durable bonding and provide the advantage of electrical conductivity, eliminating the need for traditional soldering methods. Here, we delve into the critical aspects of conductive adhesives for electrical connections, highlighting their advantages, applications, and considerations:
Advantages of Conductive Adhesives
- Versatile Bonding:Conductive adhesives can securely bond various substrates, including metals, plastics, and ceramics, enabling compatibility with diverse electric appliance components.
- Reduced Thermal Stress:Unlike soldering, conductive adhesives operate at lower temperatures, minimizing thermal stress on sensitive electronic components.
- Improved Shock Resistance:The flexibility of conductive adhesive joints enhances shock and vibration resistance, which is crucial for maintaining appliance durability.
Applications in Electric Appliances
- Printed Circuit Boards (PCBs): Conductive adhesives attach components to PCBs, replacing conventional soldering and facilitating streamlined manufacturing processes.
- Flex Circuits:These adhesives are well-suited for flexible circuit applications, maintaining connection integrity even in bendable components.
- Sensor Integration:Conductive adhesives enable seamless integration of sensors into appliances, promoting accurate data collection and improved functionality.
- LED Assembly:Conductive adhesives ensure reliable connections and efficient heat dissipation in LED lighting systems.
Considerations for Usage
- Material Compatibility:Careful selection of conductive adhesive materials is essential to ensure compatibility with the substrates and the electrical requirements.
- Electrical Conductivity:Conductive adhesives exhibit a range of conductivity levels. Choosing a suitable adhesive with the desired conductivity is crucial for optimal performance.
- Environmental Conditions:Appliance usage environments can vary widely. Choose conductive adhesives based on their resistance to temperature, humidity, and chemical exposure.
- Process Optimization:Manufacturers must optimize their assembly processes to accommodate the unique properties of conductive adhesives, including cure time and application methods.
Conductive adhesives have emerged as a game-changer in electric appliance adhesive technology, offering versatile bonding, enhanced durability, and simplified manufacturing processes. As the demand for compact, efficient, and reliable electronic devices continues to grow, the role of conductive adhesives in ensuring robust electrical connections remains paramount.
Thermal Management with Adhesive Solutions
Effective thermal management is paramount to ensure optimal performance and longevity in the ever-evolving landscape of electronics and electric appliances. Adhesive solutions play a vital role in addressing these devices’ challenges of heat generation. From smartphones to industrial machinery, maintaining the ideal temperature range enhances efficiency and prevents potential hazards. Here’s how adhesive solutions contribute to efficient thermal management:
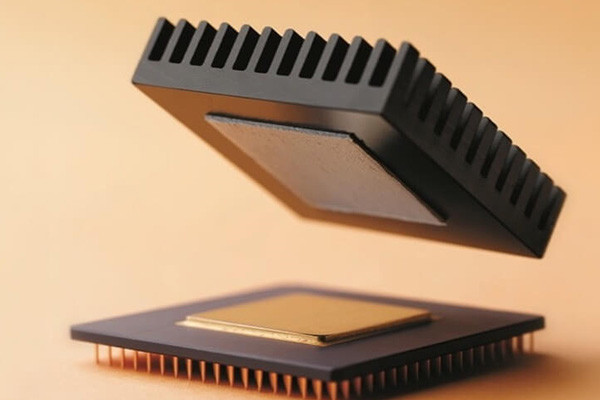
Conductive Adhesives for Heat Dissipation
- Enhanced Heat Transfer:Engineers design conductive adhesives with high thermal conductivity, enabling them to transfer heat away from sensitive components efficiently.
- Reduced Hotspots:By evenly distributing heat across surfaces, these adhesives mitigate the formation of hotspots that can degrade performance.
Gap Fillers for Air Pockets Elimination
- Eliminating Air Pockets:Designers create gap-filling adhesive materials to remove air gaps between components, guaranteeing improved thermal conduction.
- Improved Heat Flow:By minimizing insulation caused by trapped air, these adhesives promote improved heat flow throughout the device.
Phase Change Materials (PCMs) for Temperature Regulation
- Constant Temperature Maintenance:PCMs embedded in adhesives absorb and release heat as needed, maintaining a steady temperature within the device.
- Reduced Overheating Risks:PCMs act as a buffer, absorbing excess heat during peak operation and releasing it during cooling periods.
Insulating Adhesives for Heat Isolation
- Heat Isolation and Diversion:Insulating adhesives create barriers that prevent heat transfer between sensitive components and external surroundings.
- Protection from Environmental Factors:These adhesives shield delicate electronics from extreme temperatures and humidity, enhancing device durability.
In the realm of electric appliances and electronics, thermal management is critical to ensure reliability and performance. Adhesive solutions, from conductive adhesives to phase change materials, empower engineers and designers to tackle heat-related challenges effectively. By leveraging the capabilities of these adhesives, manufacturers can create devices that operate optimally, even under demanding conditions, while maximizing longevity and minimizing risks associated with overheating.
Adhesive Applications in Printed Circuit Boards (PCBs)
Printed Circuit Boards (PCBs) form the backbone of modern electronics, and adhesive solutions are pivotal in ensuring their stability, performance, and overall functionality. From bonding components to enhancing mechanical strength, adhesives offer versatile applications indispensable in PCB manufacturing. Here’s a glimpse of how adhesive solutions contribute to the efficiency and reliability of PCBs:
Component Attachment and Bonding
- Surface Mount Technology (SMT) Adhesives:These adhesives secure surface-mounted components, ensuring precise alignment and minimizing the risk of detachment.
- Through-Hole Component Bonding:Adhesives used in through-hole assembly reinforce the connection between components and PCBs, enhancing mechanical stability.
Thermal Management and Heat Dissipation
- Thermally Conductive Adhesives:These adhesives efficiently transfer heat away from sensitive components, preventing overheating and maintaining optimal performance.
- Heat Sink Bonding:Adhesive solutions securely attach heat sinks to components, improving the overall thermal efficiency of the PCB.
Protection and Insulation
- Conformal Coatings:These coatings provide a protective layer that safeguards components from moisture, dust, and contaminants, extending the lifespan of the PCB.
- Insulating Adhesives:Adhesives with insulating properties create barriers that prevent electrical interference and short circuits, ensuring reliable operation.
Vibration and Shock Resistance
- Vibration Damping Adhesives:These adhesives absorb and dissipate vibrations, reducing the risk of mechanical failure caused by dynamic loads.
- Impact-Resistant Bonding:Adhesives enhance the mechanical strength of PCB connections, making them more resistant to shocks and impacts.
In the intricate world of PCB manufacturing, adhesive solutions emerge as crucial components contributing to electronic devices’ stability, functionality, and longevity. Their applications encompass everything from ensuring secure component attachment to managing heat, protecting against environmental factors, and bolstering mechanical strength. As electronic appliances become more advanced and intricate, the role of adhesive solutions in PCBs continues to expand, underscoring their importance in maintaining the reliability and performance of modern electronics.
Securing Components: Adhesives in Mobile Devices
Adhesives play an integral role in the construction and functionality of mobile devices, ensuring the structural integrity, performance, and aesthetics of these technological marvels. From smartphones to tablets, adhesive solutions provide diverse applications that contribute to the overall user experience. Here’s a glimpse into how adhesives are instrumental in securing components within mobile devices:
- Display Bonding:Adhesive solutions bond the display panel to the device’s frame, ensuring a seamless and sturdy connection that enhances visual appeal and structural integrity.
- Battery Attachment:Adhesives secure the battery to the device’s casing, preventing any movement or damage that might result from daily usage and impacts.
- Camera Module Fixation:The precise positioning of camera modules is achieved through adhesive attachment, ensuring accurate alignment and optimal photography performance.
- Speaker and Microphone Mounting:Adhesives securely fasten speakers and microphones in place, contributing to the device’s audio quality and functionality.
- Water and Dust Resistance:Adhesive seals protect the internal components from water and dust ingress, enhancing the device’s durability and longevity.
- Slim Design Facilitation:Adhesives allow for compact and small designs by eliminating the need for bulky mechanical fasteners while maintaining structural stability.
- Heat Dissipation Enhancement:Thermally conductive adhesives help dissipate heat generated by the device’s internal components, preventing overheating and maintaining optimal performance.
- Circuit Board Attachment:Adhesives bond circuit boards to the device’s frame, ensuring secure electrical connections and preventing board movement.
- Vibration Damping:Adhesive solutions absorb vibrations caused by user interactions and external forces, protecting delicate components from damage.
- Aesthetic Finish:Adhesives offer transparent and invisible bonding, maintaining the device’s sleek design and allowing for edge-to-edge displays.
In the realm of mobile devices, adhesive solutions go beyond simple bonding – they empower engineers to create devices that are functional, visually appealing, durable, and reliable. The seamless integration of adhesives within the intricate components of mobile devices ensures that users can enjoy sleek designs, robust performance, and a device that stands the test of time.
Adhesive Solutions for Wearable Electronics
In the dynamic world of wearable electronics, adhesive solutions are the unsung champions that enable innovation, comfort, and functionality. These specialized adhesives are the invisible force that holds wearable devices together, providing the necessary bond for components while ensuring user comfort and reliability. Here’s a glimpse into the diverse applications and benefits of adhesive solutions in wearable electronics:
- Skin-Friendly Comfort:When crafting adhesives for wearables, manufacturers consider skin sensitivity to ensure that users can comfortably wear the device for extended periods.
- Secure Attachment:Whether it’s fitness trackers, smartwatches, or medical wearables, adhesive solutions provide a particular bond that withstands movement and usage.
- Flexibility and Freedom:Wearable adhesives offer the flexibility required for devices to conform to body contours and movements without compromising durability.
- Sensor Integration:Adhesives enable precise sensor placement, which is crucial for accurate data collection in health monitoring and activity tracking.
- Battery Stability: Adhesive solutions securely fasten batteries to wearables, contributing to compact designs and reliable power.
- Water and Sweat Resistance:Wearable adhesives often include protective seals that guard against water, sweat, and moisture, making them suitable for active lifestyles.
- Invisible Design:Adhesives allow for discreet device attachment, maintaining the aesthetics of wearables and enabling fashionable designs.
- Biocompatibility:Adhesive materials are chosen for their biocompatibility, ensuring safe and irritation-free contact with the skin.
- Conformal Coatings:These coatings protect sensitive electronic components from environmental factors while maintaining the device’s flexibility and comfort.
- Thermal Management:Thermally conductive adhesives prevent discomfort by efficiently dissipating heat generated by wearable components.
From enabling advanced health tracking to providing a seamless user experience, adhesive solutions are the unsung heroes that empower wearable electronics to blend seamlessly into our lives. As wearables continue to evolve, these adhesives will play an increasingly critical role in ensuring devices are functional but also comfortable, stylish, and ready to withstand the demands of modern lifestyles.
Enhancing Display Technologies through Adhesives
In the realm of rapidly advancing display technologies, Electric Appliance Adhesives have emerged as a transformative force that revolutionizes modern screens’ design, manufacture, and experience. These unassuming yet indispensable components play a pivotal role in enhancing displays’ visual quality, durability, and functionality across various industries. Here’s an exploration of how Adhesive Innovations are elevating display technologies:
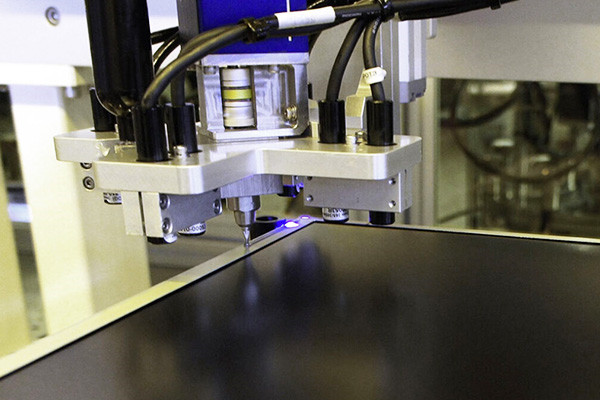
- Seamless Bonding for Flawless Visuals:Adhesives facilitate the seamless bonding of display layers, ensuring uniformity in brightness, color accuracy, and clarity. This capability enables viewers to enjoy flawless visuals without interruptions caused by gaps or inconsistencies in layers.
- Curved and Flexible Displays:Adhesive technologies enable the creation of curved and flexible displays that reshape user interactions with devices. These adhesives securely hold together the layers of flexible screens, allowing for sleek designs while maintaining structural integrity.
- Vibration Dampening for Enhanced Durability: People often subject display devices to beatings and impacts. Electric appliance adhesives act as vibration dampeners, protecting delicate components from damage and ensuring prolonged display longevity.
- Optical Clarity and Anti-Glare Properties:Advanced adhesives possess excellent optical properties, such as high transparency and minimal light scattering. This results in displays with improved visual clarity and reduced glare, enhancing user comfort and readability.
- Adapting to Diverse Materials:Manufacturers construct displays using various materials, including glass, plastic, and metal. Adhesive innovations offer versatile bonding solutions that cater to the unique properties of each material, promoting robust and reliable connections.
- Thermal Management and Cooling:High-performance displays generate heat, impacting their performance and lifespan. Adhesives with practical thermal conductivity help dissipate heat efficiently, preventing overheating and maintaining consistent display quality.
- Water and Dust Resistance:Displays in portable devices and outdoor applications require protection against environmental elements. Adhesive solutions create a barrier that guards against water and dust ingress, enhancing the durability and reliability of displays.
- Reducing Reflections and Glare:Adhesive technologies can incorporate anti-reflective and anti-glare properties into displays, reducing unwanted reflections and improving visibility, particularly in bright or outdoor settings.
- Innovations in Transparent Displays:Adhesives are critical for assembling transparent displays, which find applications in augmented reality (AR) and heads-up displays (HUDs). These innovations create seamless user experiences by overlaying digital information in the real world.
Automotive Electronics and Adhesive Innovations
In the rapidly evolving landscape of automotive technology, Automotive Electronics, and Adhesive Innovations have emerged as crucial drivers of progress, redefining how vehicles are designed, manufactured, and operated. Electric vehicles (EVs) have gained substantial traction, pushing the boundaries of traditional automotive engineering. At the heart of this transformation lies a critical component: electric appliance adhesive. This unassuming yet groundbreaking innovation has quietly revolutionized how electronic components are integrated within vehicles, ensuring seamless functionality, safety, and durability. Here are some key points highlighting the significance of automotive electronics and adhesive innovations:
- EV Proliferation:The surge in electric vehicle adoption has necessitated a reimagining of automotive electronics. Traditional internal combustion engines give way to intricate electric propulsion systems, demanding advanced electronic control units (ECUs) and battery management systems (BMS). Adhesives are pivotal in securely affixing these components, allowing for efficient heat dissipation and electrical insulation.
- Compact and Lightweight Solutions:Adhesive technologies have enabled compact and lightweight electronic module design and manufacturing. Traditional mechanical fastening methods are often bulkier and heavier, whereas adhesives provide flexibility in component placement and contribute to improved overall vehicle aerodynamics and weight distribution.
- Vibration and Shock Resistance:Modern vehicles traverse diverse terrains, subjecting electronic components to constant vibrations and shocks. Specially formulated adhesives act as shock absorbers, preventing internal damage and ensuring sustained performance, even in rugged conditions.
- Thermal Management:Electric systems generate significant heat, requiring effective thermal management. Adhesive solutions with high thermal conductivity assist in dissipating heat from sensitive components, reducing the risk of overheating and enhancing overall system reliability.
- Water and Dust Protection:Adhesive innovations extend beyond mechanical bonding; they provide a protective seal against environmental factors such as water and dust infiltration. This safeguarding mechanism is pivotal for maintaining electronic functionality and longevity in challenging weather conditions.
- Enhanced Durability and Longevity:With automotive electronics exposed to various temperature fluctuations and operational stress, superior bonding strength and chemical resistance adhesives contribute to prolonged lifespan and reduced maintenance requirements.
- Sustainable Manufacturing:As the automotive industry steers towards sustainability, eco-friendly adhesives that minimize harmful volatile organic compound (VOC) emissions are gaining prominence. These adhesives align with the industry’s push for greener manufacturing practices.
- Innovation Trajectory:The synergy between automotive electronics and adhesive technologies continues to evolve. Research and development efforts focus on creating adhesives that adapt to emerging electronic architectures, including autonomous driving systems and AI-driven functionalities.
Sustainable Practices: Eco-Friendly Adhesives for Electronics
In electronics, adopting sustainable practices has become a paramount concern, and eco-friendly adhesives are at the forefront of this shift. As the electronics industry evolves towards greater environmental responsibility, developing and utilizing adhesive solutions that prioritize sustainability are gaining prominence. Here are key points highlighting the significance of eco-friendly adhesives in fostering sustainable practices within the electronics sector:
Biodegradable and Renewable Materials
- Eco-friendly adhesives are formulated using biodegradable and renewable materials, reducing the reliance on petroleum-derived components.
- These adhesives contribute to the reduction of non-biodegradable waste and resource depletion.
Low Volatile Organic Compounds (VOC) Emissions
- Sustainable adhesives have low VOC emissions during both production and application, minimizing harmful pollutants released into the environment.
- Using low-VOC adhesives supports healthier indoor air quality and reduces environmental impact.
Energy-Efficient Production Processes
- Eco-friendly adhesive manufacturing processes prioritize energy efficiency and reduce carbon emissions.
- Sustainable production practices align with global efforts to mitigate climate change and promote resource conservation.
Recyclability and Disassembly
- Adhesive formulations allowing easy disassembly and component separation enable efficient recycling and material recovery.
- Electronics with eco-friendly adhesives are more conducive to circular economy principles.
Extended Product Lifespan
- Sustainable adhesives enhance the durability and reliability of electronic devices, prolonging their operational lifespan.
- Longer-lasting products reduce electronic waste and contribute to a more sustainable consumption pattern.
Water-Based and Solvent-Free Formulations
- Water-based and solvent-free adhesives eliminate hazardous chemicals and reduce the environmental impact of volatile solvents.
- Such adhesives are safer for manufacturers and end-users while minimizing ecosystem harm.
Compliance with Green Standards
- Eco-friendly adhesives adhere to eco-labeling and green certification standards, ensuring they meet established sustainability criteria.
- Compliance with recognized standards supports transparent communication of a product’s environmental benefits.
Innovation in Packaging
- Sustainable adhesive solutions extend beyond formulation, encompassing eco-friendly packaging materials and reducing packaging waste.
- Minimized packaging waste contributes to the reduction of the overall environmental footprint.
Challenges in Electric Appliance Bonding
The landscape of electric appliance manufacturing is marked by its intricate challenges, particularly in bonding. Adhesive technologies play a pivotal role in creating reliable and efficient connections within these devices, but they also confront a range of hurdles that demand innovative solutions. We can elucidate the challenges in electric appliance bonding through the following key points:
- Material Diversity:Electric appliances encompass various materials, from metals and plastics to ceramics and flexible substrates. Bonding adhesives must exhibit compatibility with these multiple materials while maintaining strong and durable connections.
- Miniaturization:The ongoing trend towards smaller and more compact devices necessitates bonding solutions that can operate effectively on micro and nanoscales. Ensuring consistent adhesive coverage and reliable bonding in confined spaces presents a significant challenge.
- Thermal Management:Electric appliances generate heat during operation, which can impact the performance of bonding materials. Adhesives must exhibit stability in the face of temperature fluctuations, ensuring that bonds remain secure even in high-temperature environments.
- Environmental Factors:Various environmental conditions subject appliances to humidity, moisture, UV radiation, and chemicals, and bonding materials must withstand these factors without deteriorating or losing their adhesive properties.
- Durability and Longevity:We expect electric appliances to have a long operational lifespan, often enduring frequent use and potential mechanical stress. Adhesives must maintain their integrity over time, resisting wear, tear, and mechanical forces to ensure the device’s longevity.
- Automation and Manufacturing Efficiency:As the demand for electric appliances grows, efficient and scalable manufacturing processes become crucial. Adhesive application methods, such as dispensing and curing, must be automated and optimized for consistency and speed.
- Electrical Conductivity:In electronic devices, the adhesive must not impede electrical conductivity between components. Finding bonds that provide mechanical solid bonding and promising electrical pathways can be challenging.
- Repair and Maintenance:Manufacturers face challenges in maintaining repairability when using strong appliance adhesives. Balancing the strength of the bond with the ease of disassembly is a delicate task.
- Regulatory Compliance:Adhesive materials used in electric appliances must adhere to various regulatory standards, especially regarding health, safety, and environmental impact.
- Innovation and R&D: The field of electric appliance bonding is in constant flux, driven by advancements in adhesive technology and device design. Staying ahead of emerging trends while tackling existing challenges requires continuous research and development.
Ensuring Safety: Adhesive Role in Insulation
In the realm of insulation, adhesives play a pivotal role in ensuring safety, efficiency, and longevity across various applications. As insulation is a critical barrier against heat, electricity, and environmental factors, adhesive technologies are instrumental in creating reliable and robust insulation systems. Here are vital points illustrating the significance of adhesives in ensuring safety through effective insulation:
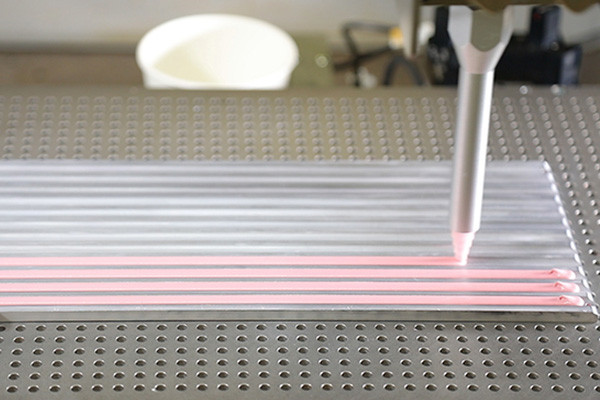
Secure Bonding for Insulating Materials
- Adhesives facilitate strong bonding between insulating materials, creating a seamless protective layer that prevents heat transfer and electrical conductivity.
- Securely bonded insulation materials ensure consistent performance and prevent potential safety hazards.
Thermal Insulation Enhancement
- Adhesive formulations with high thermal resistance properties contribute to the efficiency of thermal insulation systems.
- Insulating adhesives prevent heat transfer, maintaining temperature stability and reducing energy consumption.
Electrical Insulation Reliability
- Adhesives with superior electrical insulating properties prevent electrical current leakage, reducing the risk of short circuits and electrical malfunctions.
- Insulating adhesives are vital in applications ranging from high-voltage power distribution to delicate electronics.
Weatherproofing and Environmental Protection
- Adhesive insulation materials provide weatherproofing and environmental protection, guarding against moisture, dust, and contaminants.
- Effective sealing prevents degradation and prolongs the lifespan of insulated components.
Adhesive Sealants for Energy Efficiency
- Adhesive sealants play a role in creating airtight seals in insulation systems, enhancing energy efficiency by preventing heat loss or gain.
- Insulating sealants contribute to sustainable building practices and reduced energy consumption.
Safety in Hazardous Environments
- In hazardous environments, adhesives insulate against extreme temperatures, chemicals, and corrosive substances.
- Insulating adhesives ensures equipment and personnel safety in chemical processing and manufacturing industries.
Flexible and Versatile Applications
- Adhesives offer flexibility in application, adhering to a wide range of substrates and accommodating complex shapes and designs.
- Versatile adhesive solutions enable insulation in diverse industries, from construction to automotive to electronics.
Regulatory Compliance and Fire Resistance
- Adhesive insulation solutions meet stringent regulatory standards for fire resistance and safety.
- Fire-resistant adhesive insulators prevent the spread of flames and contribute to fire containment.
Adhesive Contribution to Water-Resistant Electronics
In the dynamic realm of electric appliance manufacturing, the role of adhesives in achieving water-resistant electronics stands as a transformative advancement. Adhesive technologies have emerged as a cornerstone in fortifying devices against water infiltration, presenting various benefits beyond mere protection. We can encapsulate the significance of the adhesive contribution to water-resistant electronics through the following key points:
- Sealing Vulnerabilities:Adhesive materials serve as robust barriers against water and moisture ingress, preventing corrosion and short circuits that can compromise device functionality. These materials work to seal gaps and crevices in electronic assemblies, ensuring long-term durability in diverse environments.
- Diverse Applications:Water-resistant adhesives have applications across various devices, from smartphones and tablets to wearables and outdoor electronics. Their flexibility in adhering to different substrates and geometries makes them indispensable for reliable waterproofing.
- Preservation of Aesthetics:Conserving sleek and streamlined designs is possible with water-resistant adhesives, as they can be applied without adding excessive bulk to the device. This approach ensures that water protection does not compromise the aesthetic appeal.
- Enhanced Reliability:Adhesive solutions contribute to the overall reliability of electronic devices, particularly those used in demanding conditions such as marine, industrial, or outdoor settings. By preventing water-related damage, these adhesives extend the lifespan of appliances and reduce maintenance costs.
- Material Compatibility:Adhesive formulations have evolved to accommodate various materials used in electronics, including metals, plastics, ceramics, and flexible substrates. This compatibility enhances their utility in diverse manufacturing scenarios.
- Innovative Bonding Techniques:Adhesive manufacturers have developed techniques such as conformal coatings and encapsulation methods to ensure comprehensive coverage and protection. These techniques address challenges associated with intricate components and complex geometries.
- Collaborative Design:Adhesive engineers collaborate closely with device designers and manufacturers to develop tailored solutions that meet specific waterproofing requirements. This collaborative approach allows for integrating water-resistant properties during the early design stages.
- Continuous Advancements:The field of water-resistant electronics is constantly evolving, driven by ongoing research and development in adhesive materials and application techniques. As electronics become more integrated into daily life, the demand for reliable water protection continues to fuel innovation in this domain.
Miniaturization and Adhesive Precision
In the realm of electric appliance manufacturing, miniaturization, and adhesive precision have emerged as pivotal factors shaping the landscape of technological advancement. The relentless pursuit of smaller, more efficient devices has driven engineers and researchers to explore innovative miniaturization techniques, resulting in many remarkable breakthroughs. The evolution of adhesive precision, a critical enabler of assembling intricate components in confined spaces, has underpinned these developments. Several key points underscore the significance of miniaturization and adhesive precision in the realm of electric appliance adhesive:
- Shrinking Dimensions:The demand for sleeker and more compact electric appliances, from smartphones to wearable devices, has propelled the need for miniaturization. Engineers have harnessed cutting-edge fabrication processes, such as micro-electro-mechanical systems (MEMS) and 3D printing, to craft diminutive yet high-performing components.
- Enhanced Performance:Miniaturization enhances the aesthetic appeal of devices and bolsters their performance. Smaller components, often utilizing nanoscale technologies, exhibit reduced power consumption and improved speed, revolutionizing the user experience across various appliances.
- Adhesive Precision as the Glue:Adhesive precision has emerged as a linchpin in the assembly of miniaturized components. Nanoscale adhesive materials and techniques, such as anisotropic conductive adhesives (ACAs) and non-conductive adhesives (NCAs), play a pivotal role in securely bonding delicate parts without compromising electrical conductivity.
- Challenges and Solutions:As components become tinier, bonding accuracy and durability challenges have intensified. Engineers have countered these obstacles by developing advanced dispensing systems, automated assembly robots, and novel curing methods that ensure uniform adhesive distribution and practical attachment.
- Cross-Disciplinary Collaboration:Achieving adhesive precision in miniaturization necessitates collaboration across disciplines. Material scientists, mechanical engineers, and electrical engineers work synergistically to formulate adhesive solutions that meet the demands of size constraints and electrical connectivity.
- Future Prospects:The miniaturization trajectory and adhesive precision will continue evolving. With the advent of Internet of Things (IoT) devices and flexible electronics, adhesive technologies will further develop to accommodate intricate designs, flexible substrates, and diverse material compatibility.
Adhesives in Medical Electronic Devices
The integration of adhesives in medical electronic devices represents a critical intersection of technology and healthcare, enabling the development of sophisticated and life-enhancing medical solutions. Adhesive advancements are revolutionizing medical device manufacturing and performance, ensuring secure and reliable application connections. Here are key points illustrating the significance of adhesives in medical electronic devices:
Biocompatibility and Safety
- Adhesives used in medical devices prioritize biocompatibility, ensuring compatibility with human tissue and minimizing the risk of adverse reactions.
- Medical-grade adhesives undergo rigorous testing to meet strict regulatory standards and ensure patient safety.
Miniaturization and Wearable Devices
- Adhesives facilitate the design of compact and wearable medical electronic devices that patients can discreetly wear for continuous monitoring and treatment.
- Flexible and skin-friendly adhesive materials adhere to the body’s contours, enhancing patient comfort.
Precision and Reliability
- Adhesive technologies provide precise bonding, which is vital for the intricate assembly of medical electronic components.
- Reliable connections enhance the accuracy of diagnostic and therapeutic devices, ensuring consistent and dependable performance.
Sensors and Monitoring Devices
- Adhesives enable the secure attachment of sensors and electrodes to the skin, allowing for real-time monitoring of vital signs and patient conditions.
- These adhesive-bonded sensors are integral to remote patient monitoring and telemedicine.
Implantable Medical Devices
- Adhesive materials play a role in securing components of implantable medical devices, such as pacemakers and neurostimulators, within the body.
- Implant adhesive formulations ensure long-lasting stability and biocompatibility for safe and practical integration.
Waterproof and Ingress Protection
- Adhesives protect sensitive electronic components from moisture and environmental factors by providing water-resistant and ingress-protection properties.
- Waterproof adhesives maintain the reliability of medical devices exposed to bodily fluids and external elements.
Surgical Applications
- Adhesives are used in wound closure and surgical procedures, offering alternatives to traditional sutures and staples.
- Surgical adhesives promote faster healing, reduce scarring, and enhance patient comfort during recovery.
Innovation in Drug Delivery
- Adhesive patches with incorporated drug delivery mechanisms enable controlled and localized administration of medications, offering personalized treatment options.
- Transdermal patches and adhesive drug delivery systems enhance patient compliance and therapeutic outcomes.
Aerospace Applications: Adhesive Advancements
In the dynamic realm of aerospace applications, adhesive advancements are paramount in shaping the industry’s progress. As the demand for lighter, more fuel-efficient aircraft and spacecraft intensifies, adhesive technologies undergo transformative developments to meet stringent performance requirements. Here are vital points that illuminate the pivotal role of adhesive advancements in aerospace:
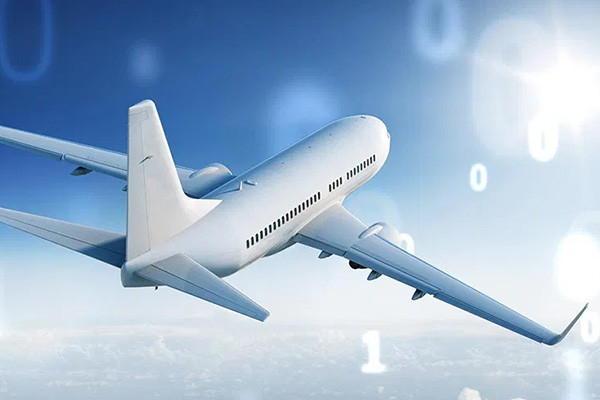
Weight Reduction and Fuel Efficiency
- Adhesives contribute to the ongoing pursuit of lightweight structures as they replace traditional fasteners and welding methods.
- Reduced aircraft weight decreases fuel consumption, lowering operational costs and environmental impact.
Bonding Dissimilar Materials
- Aerospace designs often combine materials with varying properties. Adhesives enable strong bonds between dissimilar materials, enhancing structural integrity.
- Composite materials, metals, and advanced polymers can seamlessly join, optimizing component design and performance.
Vibration Damping and Noise Reduction
- Adhesives with excellent damping properties absorb vibrations and reduce noise, enhancing passenger comfort and component longevity.
- Improved adhesive formulations lead to quieter and smoother flights.
High-Temperature Resistance
- Aerospace environments expose adhesives to extreme temperatures. Advancements deliver adhesive solutions that maintain strength and stability under challenging conditions.
- Heat-resistant adhesives ensure reliable performance in engine compartments and high-temperature areas.
Enhanced Durability and Fatigue Resistance
- Adhesive innovations focus on improving long-term durability and fatigue resistance, which is vital for the demanding conditions of aerospace travel.
- Bonded joints withstand cyclic loading, preventing premature failure and reducing maintenance needs.
Streamlined Manufacturing Processes
- Adhesives enable automated assembly processes, reducing production time and costs.
- We can efficiently bond complex structures, contributing to faster aircraft and spacecraft manufacturing.
Space Exploration and Satellite Applications
- Adhesives are critical in space missions, securing components and ensuring structural integrity in zero-gravity environments.
- Satellites benefit from lightweight and reliable adhesive bonding, enhancing overall mission success.
Regulatory Compliance and Safety
- Aerospace adhesive advancements align with stringent industry standards and safety regulations, ensuring reliable performance in critical applications.
- Adhesives undergo rigorous testing to meet the demands of extreme conditions.
As aerospace technology advances, adhesive innovations remain at the forefront of enabling progress and efficiency in the industry. The multifaceted benefits of adhesive advancements, including weight reduction, enhanced material compatibility, improved durability, and streamlined manufacturing processes, underscore their indispensable role in shaping the future of aerospace applications. Collaborations between adhesive manufacturers and aerospace engineers drive the evolution of adhesive technologies, fostering safer, more efficient, and environmentally conscious aerospace solutions.
Future Trends in Electric Appliance Adhesives
In the ever-evolving landscape of electric appliances, adhesive technologies are crucial in ensuring both functionality and aesthetics. As manufacturers aim to improve product performance, safety, and user experience, they are shaping the industry’s future trends in electric appliance adhesives. Here are some key points highlighting these upcoming trends:
Sustainability and Eco-Friendly Solutions
- Growing emphasis on environmental responsibility drives the demand for adhesive solutions with reduced environmental impact.
- Bio-based and renewable adhesive materials gain traction to replace petroleum-derived counterparts.
- Adhesives with low VOC emissions and minimal energy consumption during production have become more prominent.
Miniaturization and Bonding Precision
- As devices become smaller and more intricate, adhesives that offer precise bonding in tight spaces gain significance.
- Micro- and nano-level adhesive technologies enable reliable connections in miniature components.
- High-precision dispensing techniques and automated application processes ensure consistent and accurate bonding.
Thermal Management and Heat Resistance
- Electric appliances often generate heat during operation, making thermal management a critical concern.
- Adhesives with exceptional heat resistance and thermal conductivity help dissipate heat efficiently.
- Enhanced thermal interface materials ensure better connectivity between components and heat sinks.
Flexible Electronics and Wearables
- The rise of flexible electronics and wearables demands adhesives that bond dissimilar materials without compromising flexibility.
- Stretchable and bendable adhesive formulations accommodate the unique requirements of wearable devices.
Advanced Electronics Protection
- Adhesives with strong moisture resistance, corrosion protection, and insulating properties safeguard delicate electronic components.
- When protected by encapsulation and conformal coating adhesives, Appliances are protected against environmental factors, ultimately extending their lifespan.
Smart Bonding Technologies
- Integration of IoT technology in appliances leads to the development of intelligent adhesives capable of sensing changes in the environment.
- Self-healing adhesives repair minor damage, enhancing the durability and reliability of appliances.
Improved User Experience and Aesthetics
- Adhesives contribute to the seamless design of appliances, concealing seams and joints for a sleek appearance.
- Soft-touch adhesives enhance user comfort and grip, particularly in handheld devices.
Regulatory Compliance and Safety
- Adhesives that meet stringent industry standards and regulations gain prominence as safety remains a top priority.
- Non-toxic and flame-retardant adhesive options address health and safety concerns.
As the electric appliance landscape continues to evolve, these future trends in adhesive technologies are poised to reshape the industry by addressing challenges and enhancing performance across various applications. Manufacturers and researchers are at the forefront of driving innovation in this crucial aspect of product development, ensuring that tomorrow’s appliances are functional, environmentally responsible, and user-friendly.
User-Friendly Designs: Adhesive’s Influence on Ergonomics
In product design, user-friendliness is a pivotal principle, with ergonomic considerations playing a paramount role. An often underestimated factor contributing to user comfort and convenience is the application of advanced adhesives in electric appliances. These adhesive technologies enhance the structural integrity of appliances and significantly influence their ergonomics, fostering a seamless user experience.
Key points illustrating the impact of adhesives on ergonomics:
- Streamlined Aesthetics:Adhesives enable sleek and smooth joint designs, eliminating the need for protruding mechanical fasteners. This results in appliances with visually appealing surfaces, free from uneven contours that might disrupt the user’s tactile experience.
- Enhanced Comfort:Adhesives facilitate the bonding of soft-touch materials to device components, improving the appliance’s feel in hand. This aspect is particularly notable in appliances with handles or grips, as the absence of rough fasteners ensures a comfortable and non-abrasive touch.
- Reduced Vibrations and Noise:Adhesive bonding absorbs vibrations more effectively than traditional mechanical fasteners, reducing operational noise and enhancing the overall comfort of appliance usage.
- Seamless Sealing:In appliances that come into contact with liquids or require airtight compartments, adhesives play a vital role in creating impermeable seals. These measures prevent water or dust ingress, contributing to the appliance’s longevity while also ensuring the user’s ease of maintenance.
- Optimized Weight Distribution:Adhesives allow for strategic weight distribution in appliances, improving their balance and making them less cumbersome. This relevance is particularly notable in handheld devices like hair dryers or power tools.
- Customized Design Solutions:Adhesives offer a wide range of bonding options, allowing designers to experiment with materials and forms that might otherwise be challenging to integrate. This flexibility enables the creation of appliances that align precisely with user needs and ergonomic expectations.
Electric appliance adhesives serve as the unifying force behind the intricate amalgamation of components in modern electronic devices. From ensuring reliable connections to contributing to thermal management and safety, these adhesives play a pivotal role in numerous industries. As technology continues to evolve, electric appliance adhesives will undoubtedly remain at the forefront of innovation, enabling the creation of more advanced, efficient, and sustainable electronic devices.