Potting and Encapsulation
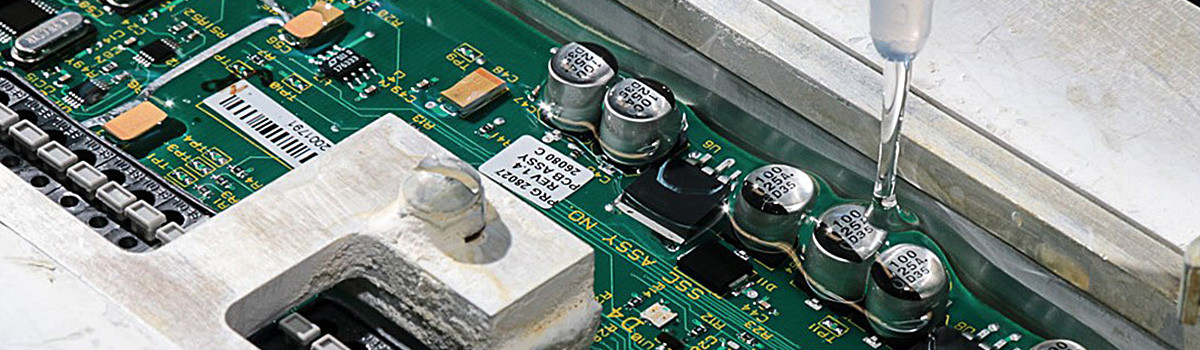
In the realm of modern manufacturing and engineering, the processes of potting and encapsulation have emerged as indispensable techniques for enhancing the protection, durability, and reliability of electronic components and various products. These methodologies involve the complete encasement of sensitive parts in a protective material, safeguarding them against external factors such as moisture, mechanical stress, and environmental contaminants. This article delves into the intricacies of potting and encapsulation, exploring their applications, benefits, materials used, and the diverse industries that benefit from their implementation.
Understanding Potting and Encapsulation
In modern manufacturing and engineering, “potting” and “encapsulation” stand as crucial techniques that protect delicate electronic components and products. These methods involve completely encasing sensitive parts within a protective material, shielding them from various external factors that could compromise their performance and longevity.
Potting refers to filling a housing or container with a liquid resin that, upon curing, forms a solid protective layer around the component. This technique effectively creates a barrier against moisture, dust, and other contaminants that could seep into the electronics, causing malfunctions or damage.
On the other hand, encapsulation involves encapsulating the entire component within a protective shell made of materials such as epoxy resins, silicone rubber, or polyurethane. This encapsulation process provides mechanical protection and guards against chemical exposure, mechanical stresses, and thermal variations that the component might encounter during its lifespan.
These techniques play a crucial role in ensuring the reliability and durability of sensitive electronics, especially in industries where components face exposure to harsh environments. Automotive electronics, for instance, experience significant benefits from potting and encapsulation as they undergo temperature fluctuations, vibrations, and exposure to moisture and chemicals. Similarly, industries like aerospace, where electronics face extreme conditions such as high altitudes and rapid temperature changes, rely on these methods to guarantee consistent performance.
Understanding the materials used in potting and encapsulation is vital. Industries widely use epoxy resins due to their excellent electrical insulation properties and chemical resistance. Silicone rubber, known for its flexibility and high-temperature resistance, finds application in components that undergo thermal cycling. Polyurethane, with its balance of protection and practicality, is often chosen for applications that require mechanical robustness.
Importance of Potting and Encapsulation
It’s impossible to overstate the importance of potting and encapsulation in modern manufacturing and engineering. These techniques offer many benefits that significantly enhance the reliability, durability, and overall performance of electronic components and products. The following points underscore the critical role these methods play:
- Environmental Protection:Potting and encapsulation create a waterproof barrier around sensitive components, safeguarding them against various environmental factors. It includes protection from moisture, dust, chemicals, and corrosive agents that could otherwise lead to malfunctions or deterioration.
- Mechanical Resilience:The protective layers formed through these processes provide mechanical reinforcement, shielding against physical impacts, vibrations, and shocks. This resilience is particularly valuable in industries where components might undergo frequent movement or encounter rugged conditions.
- Electrical Insulation:Manufacturers choose the materials for potting and encapsulation based on their high electrical insulation properties. This insulation prevents short circuits and ensures the integrity of the component’s electrical performance over time.
- Thermal Stability:Temperature fluctuations or extreme heat can subject many components to stress. You can tailor potting and encapsulation materials to withstand these temperature variations, preserving the component’s functionality even in demanding thermal environments.
- Chemical Resistance:In industries where chemical exposure is a concern, potting, and encapsulation are barriers against corrosive substances. This barrier prevents degradation and extends the lifespan of components.
- Longevity:By shielding components from various forms of wear and tear, potting and encapsulation extend the operational life of electronics, reducing the need for frequent replacements and repairs.
- Consistent Performance:Components that undergo potting and encapsulation tend to exhibit more stable and predictable performance characteristics, ensuring reliability in critical applications.
- Customization:The flexibility in choosing potting and encapsulation materials allows manufacturers to tailor the protective layer to specific needs, optimizing the balance between protection and practicality.
- Versatility:Potting and encapsulation techniques are applicable across various industries, from automotive and aerospace to medical devices and consumer electronics, highlighting their adaptability.
- Quality Assurance:Implementing these techniques during manufacturing can lead to better quality control, as they minimize potential issues stemming from environmental factors or mechanical stress.
Components Vulnerable to Environmental Factors
Potting and encapsulation are essential techniques used in electronics and engineering to protect sensitive components from environmental factors that can degrade their performance or compromise their integrity. These methods involve enclosing details within protective materials to shield them from moisture, temperature fluctuations, mechanical stress, and other potential hazards.
Vulnerable Components
Due to their delicate nature or material composition, specific components are particularly susceptible to environmental factors. Some of the vulnerable parts include:
- Integrated Circuits (ICs): The miniaturized design of ICs makes them sensitive to temperature changes and moisture, leading to potential short circuits or corrosion.
- Printed Circuit Boards (PCBs):PCBs are prone to damage from moisture and contaminants, which can lead to corrosion of traces and solder joints.
- Sensors:Environmental factors can affect sensor accuracy and response. Moisture can interfere with sensor readings, and temperature fluctuations can lead to calibration drift.
- Connectors:Corrosion of connector contacts due to moisture or chemicals can result in poor electrical connections.
- Coils and Inductors:These components are sensitive to temperature changes that can alter their inductance, affecting their performance in electronic circuits.
Potting: Protection through Enclosure
Potting involves enclosing individual components or assemblies within a protective potting compound, usually an epoxy resin. This process provides a barrier against environmental stressors, mechanical shocks, and moisture. Advantages include:
- It protects against humidity, dust, and chemicals.
- It offers enhanced mechanical stability and shock resistance.
- It possesses improved thermal conductivity for effective heat dissipation.
- Reduced risk of vibration-induced damage.
Encapsulation: Barrier against Harsh Conditions
Encapsulation entails surrounding components with a protective coating, often a silicone-based material. This method shields components from environmental factors and offers benefits such as:
- It exhibits resistance to moisture, chemicals, and UV radiation.
- It offers flexibility to accommodate component expansion and contraction.
- It provides electrical insulation to prevent short circuits.
- Enhanced durability in extreme conditions.
Challenges and Considerations
While potting and encapsulation are effective protective measures, there are challenges and considerations to keep in mind:
- Thermal Management:Improper potting or encapsulation can impede heat dissipation, leading to component overheating.
- Accessibility:Components become inaccessible for maintenance or repairs once potted or encapsulated.
- Material Selection: Choosing the right potting or encapsulation material is crucial to ensure compatibility with the components and the environment.
Materials Utilized in Potting and Encapsulation
The choice of materials utilized in potting and encapsulation is critical in determining the effectiveness and longevity of the protective layer surrounding electronic components. Several materials offer distinct properties, each tailored to address specific challenges and requirements. Key considerations include:
- Epoxy Resins:These resins are widely employed for their excellent electrical insulation properties, making them suitable for components where preventing short circuits is paramount. Epoxy-based encapsulation also provides high chemical and moisture resistance, further safeguarding delicate electronics.
- Silicone Rubber:Silicone rubber, known for its flexibility and high-temperature tolerance, becomes a favored choice when components undergo thermal cycling. It maintains its integrity across a wide temperature range, making it suitable for applications where temperature variations are common.
- Polyurethane:Polyurethane materials offer mechanical robustness, balancing protection with practicality, which makes them suitable for components requiring safety and frequent maintenance or accessibility. They also exhibit good resistance to chemicals and environmental stressors.
- Potting Compounds:These specialized compounds often consist of resins and hardeners. They are selected based on the desired properties of the specific application, allowing for customization and optimization of protection against environmental factors.
- Thermoplastic Materials:Industries use thermoplastics when a more flexible and removable protective layer is needed. You can reheat and reshape them, enabling easier rework or modification of components.
- UV-Curable Resins:These resins solidify upon exposure to ultraviolet (UV) light, making them suitable for applications that require rapid curing. Industries often seeking production efficiency utilize UV-curable resins.
- Parylene Coating:Parylene is a unique material applied as a vapor and solidifies into a thin, conformal coating. It offers excellent protection against moisture, chemicals, and contaminants while maintaining optical clarity and electrical insulation.
The selection of the appropriate material depends on the application’s specific requirements, including factors such as the intended operating environment, thermal conditions, mechanical stresses, and desired levels of protection. Manufacturers must carefully assess these factors to ensure that the chosen material aligns with the performance and longevity goals of the component or product. The proper choice of potting and encapsulation material is integral to achieving a successful and durable protective solution for electronic components.
Epoxy Resins: A Widely Used Encapsulation Material
Epoxy resins have emerged as a cornerstone in potting and encapsulation due to their exceptional properties and versatile applications. These thermosetting polymers have found extensive use in safeguarding sensitive electronic components, ensuring their protection against harsh environmental conditions and mechanical stress.
Advantages of Epoxy Resins for Encapsulation
Superior Protection
- Epoxy resins provide a robust barrier against moisture, chemicals, dust, and other external agents, thus shielding components from corrosion and damage.
- They effectively prevent short circuits and electrical leakages by insulating sensitive parts.
Mechanical Strength
- Epoxy encapsulation enhances the structural integrity of components, protecting them from physical impacts, vibrations, and mechanical shocks.
Thermal Resistance
- Epoxy resins exhibit high thermal stability, allowing them to withstand various temperatures without compromising their integrity.
- This property is crucial in applications where components experience varying heat levels.
Adhesion and Compatibility
- Epoxy resins adhere well to various substrates, ensuring a secure encapsulation that minimizes the risk of delamination.
- You can tailor them to match the properties of different substrates, making them suitable for various encapsulation needs.
Applications in Potting and Encapsulation
Electronics and Circuitry
- Epoxy encapsulation protects delicate electronic components like integrated circuits (ICs), semiconductors, and sensors from moisture and contaminants.
- It improves the reliability and longevity of electronic devices, even in demanding environments.
Automotive Industry
- Industries widely use epoxy resins to encapsulate electronic modules in vehicles, safeguarding critical systems against vibration, temperature fluctuations, and chemicals in automotive environments.
Aerospace and Defense
- Epoxy potting is instrumental in securing avionic components, ensuring their performance remains uncompromised amidst extreme conditions like high altitudes and rapid temperature changes.
Renewable Energy
- Epoxy encapsulation protects solar panels, wind turbine electronics, and energy storage systems, enabling these components to endure outdoor exposure.
Challenges and Future Trends
Dispensing and Curing
- Precise dispensing and curing processes are crucial to achieving uniform encapsulation, necessitating advancements in automation and control.
Environmental Impact
- Research is ongoing to develop epoxy formulations that are more environmentally friendly, addressing concerns about their long-term ecological impact.
Nanotechnology Integration
- Incorporating nanoparticles into epoxy resins could enhance their thermal, mechanical, and electrical properties, expanding their suitability for advanced applications.
Silicone Rubber: Flexibility and High-Temperature Resistance
Silicone rubber has emerged as a versatile and indispensable material in potting and encapsulation due to its remarkable flexibility and high-temperature resistance combination. This unique set of properties makes it an ideal choice for protecting sensitive electronic components, wires, and devices in challenging environments where mechanical and thermal stresses are prevalent.
Flexibility: Ensuring Reliable Protection
- Silicone rubber’s inherent flexibility allows it to conform to various shapes and sizes of components, ensuring complete coverage and protection.
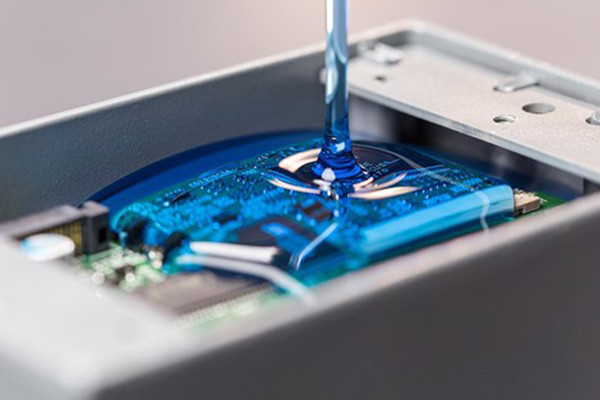
- It forms a durable yet pliable barrier that shields components from moisture, dust, and other environmental factors.
- The flexibility accommodates potential expansions, contractions, or vibrations, preventing mechanical stress-related failures.
High-Temperature Resistance: Defying Harsh Environments
- One of the most exceptional features of silicone rubber is its resistance to high temperatures, far surpassing that of many other polymer materials.
- With the ability to withstand temperatures ranging from -50°C to over 200°C (-58°F to 392°F), silicone rubber maintains its integrity and functionality in extreme conditions.
- Its high-temperature resistance makes it suitable for applications where machinery, engines, or industrial processes generate heat and expose components to those conditions.
Effective Electrical Insulation: Safeguarding Components
- Silicone rubber is an excellent electrical insulator, protecting sensitive electronic components from potential short circuits and electrical interference.
- Its high dielectric strength helps maintain the isolation and integrity of components, even in demanding electrical environments.
Chemical and Weather Resistance: Prolonging Lifespan
- Silicone rubber’s resistance to chemicals, UV radiation, and weathering ensures that encapsulated components remain shielded from corrosive agents and environmental deterioration.
- This property is crucial in outdoor installations and industries exposed to aggressive chemicals or prolonged sunlight.
Applications and Industries
- Electronics: Silicone rubber potting and encapsulation find widespread use in the electronics industry, safeguarding circuit boards, sensors, and connectors in automotive, aerospace, and consumer electronics.
- Automotive:It’s applied to ignition systems, sensors, and control modules, protecting against heat and vibrations in engine compartments.
- Energy: Silicone-encapsulated components endure the extreme temperatures and conditions in renewable energy systems, such as solar panels and wind turbines.
- Industrial Machinery: Components exposed to high temperatures, moisture, and chemicals benefit from silicone rubber’s durability and resilience.
Polyurethane: Balancing Protection and Practicality
Polyurethane is versatile in potting and encapsulation, offering a well-rounded balance between adequate protection and practicality. This material’s unique characteristics make it a preferred option for safeguarding sensitive electronic components, devices, and machinery in various demanding environments, ensuring durability and ease of use.
Adequate Protection: Shielding Components
- Polyurethane forms a robust protective barrier around components, shielding them from moisture, dust, chemicals, and physical impacts.
- Its ability to create a secure seal helps prevent corrosion and contamination, prolonging the lifespan of encapsulated elements.
- The material’s exceptional adhesion capabilities ensure a secure bond to different substrates, enhancing overall protection.
Flexibility and Impact Resistance: Withstanding Mechanical Stress
- One of polyurethane’s strengths is its flexibility and impact resistance, allowing it to absorb shocks and vibrations.
- This feature is precious in applications that expose components to mechanical stress, such as automotive and industrial settings.
- The material’s capacity to endure varying degrees of strain helps prevent cracking or damage to encapsulated elements.
Thermal Stability: Adapting to Temperature Extremes
- Polyurethane maintains its structural integrity across a broad temperature range, from sub-zero to elevated temperatures.
- Its stability makes it suitable for applications exposed to temperature fluctuations, ensuring that encapsulated components remain unaffected.
Chemical Compatibility: Defying Harsh Substances
- Polyurethane exhibits resistance to various chemicals, making it suitable for industries dealing with corrosive substances and harsh solvents.
- This chemical compatibility ensures that encapsulated components remain insulated from potential damage caused by chemical exposure.
Ease of Application: Practical Implementation
- The material’s liquid form allows easy and efficient application, adapting to complex shapes and configurations.
- Automated equipment can dispense polyurethane encapsulants, streamlining the encapsulation process in mass production.
- Its quick curing time accelerates production cycles while maintaining consistent encapsulation quality.
Applications and Industries
- Electronics:Polyurethane is widely used in the electronics industry to protect circuit boards, sensors, and connectors in applications ranging from consumer electronics to industrial controls.
- Automotive:It finds application in vehicle control modules, wiring harnesses, and sensors, providing reliable protection against mechanical stress and environmental factors.
- Renewable Energy:Polyurethane encapsulation is vital in solar panels and wind turbines, safeguarding components from weathering and temperature changes.
- Industrial Machinery:Components subjected to heavy mechanical loads and extreme conditions benefit from polyurethane’s protective and adaptable properties.
Potting vs. Encapsulation: Choosing the Right Technique
In electronics and manufacturing, achieving optimal protection for delicate components is paramount. Potting and encapsulation are widely employed techniques that offer enhanced environmental and mechanical safeguarding. While both methods aim to shield sensitive parts, they diverge in application, benefits, and suitability for various scenarios.
Potting
Definition: Potting involves enclosing a component in a rigid compound, often epoxy resin, to provide physical support and insulation.
Benefits
- Exceptional mechanical protection:The solid nature of the potting compound shields components from vibrations, impact, and external pressure.
- Effective thermal dissipation:Potting materials with good thermal conductivity play a crucial role in dissipating heat, which helps prevent overheating.
- Chemical resistance:Potting compounds can provide resistance against chemicals and environmental factors, enhancing durability.
Applications
- Heavy-duty electronics:Industries such as automotive and aerospace favor potting for applications where components experience significant mechanical stress.
- Harsh environments:It is suitable for protecting electronics in environments with extreme temperatures, humidity, and chemical exposure.
Encapsulation
Definition: Encapsulation entails surrounding a component with a protective material, often silicone, to create a barrier against moisture, contaminants, and mechanical stress.
Benefits
- Flexibility:The pliable nature of encapsulation materials accommodates slight movements, making them ideal for components prone to expansion and contraction.
- Vibration dampening:Encapsulation reduces the impact of pulses, which is crucial for delicate components like sensors.
- Water and moisture resistance:The encapsulation process creates a sealed barrier, guarding components from water ingress.
Applications
- Delicate electronics:Encapsulation, such as microelectronics and sensors, suits sensitive devices where rigidity might cause stress or damage.
- Miniaturized components:The flexibility of encapsulation materials suits tiny parts that rigid potting compounds could damage.
Choosing the Right Technique
Considerations
- Mechanical stress:Opt for potting when components face heavy mechanical loads and encapsulation for parts prone to slight movements.
- Thermal factors: Potting compounds with good thermal conductivity are preferable for components generating substantial heat.
- Environmental exposure:You should select encapsulation for moisture-prone environments and opt for potting when dealing with extreme temperatures and chemical exposure.
Hybrid Approach
- In some cases, combining potting and encapsulation can offer a balanced solution, providing mechanical protection and flexibility.
Electrical Insulation Advantages
Electrical insulation, a fundamental aspect of electronic component protection, offers a host of advantages that are pivotal for ensuring the stability and effectiveness of devices. Methods like potting and encapsulation employ electrical insulation, making a significant contribution to electronic systems’ functional and safety aspects.
1.Dielectric Strength Enhancement: Electrical insulation materials possess high dielectric strength, bolstering their ability to withstand voltage stress and preventing breakdowns that could lead to malfunctions or short circuits.
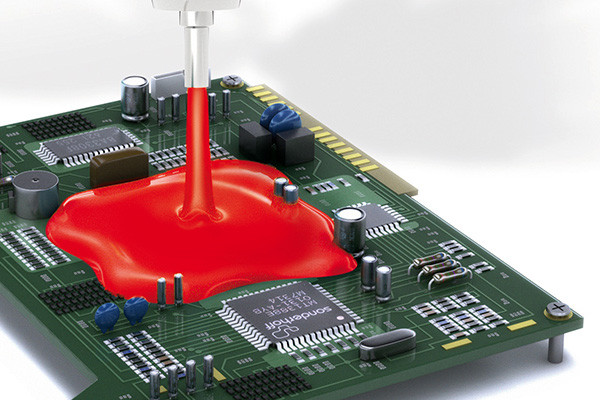
2.Isolation from Conductive Pathways: Insulation effectively isolates components from conductive materials, thwarting unintended electrical paths and reducing the risk of current leakage or interference.
3.Safety Augmentation: Insulation acts as a barrier, mitigating the potential for electric shocks to users or operators, thereby enhancing the safety of devices in various settings.
4.Environmental and Chemical Resistance: Insulation shields components from environmental factors, such as moisture and chemicals, which could otherwise compromise performance or induce corrosion.
5.Efficient Thermal Regulation: Insulation materials with favorable thermal properties aid in efficient heat dissipation, preventing overheating and preserving optimal operating conditions.
6.Prolonged Component Lifespan: By safeguarding against electrical arcing and environmental stressors, insulation contributes to prolonged component longevity, minimizing maintenance needs and replacement costs.
7.Signal Integrity Preservation: Insulation maintains the integrity of electronic signals, reducing electromagnetic interference and ensuring consistent signal quality, which is especially critical for high-frequency applications.
8.Adaptability of Materials: Insulation solutions, be it rigid potting compounds or flexible encapsulation materials, can be tailored to specific component requirements, ensuring a versatile application.
9.Diminished Downtime and Maintenance: Insulation prevents the accumulation of contaminants that might lead to downtime-inducing short circuits or malfunctions, resulting in reduced maintenance demands.
10.Streamlined Manufacturing Integration: Incorporating insulation, whether through potting or encapsulation, can be seamlessly integrated into manufacturing processes, enhancing efficiency and reproducibility.
Mechanical Reinforcement and Shock Absorption
Mechanical reinforcement and shock absorption are crucial aspects of potting and encapsulation processes in various industries. These techniques involve enclosing sensitive electronic components or delicate materials within protective casings to enhance their durability and reliability. Combining mechanical reinforcement and shock absorption shields the retained members from external physical impacts, vibrations, and harsh environments. This safeguarding process offers several benefits:
- Enhanced Structural Integrity:Potting and encapsulation materials, such as epoxy resins or silicone rubber, provide a robust outer layer that reinforces the structural integrity of the enclosed components. This protection prevents damage from mechanical stress, extending the lifespan of the elements and systems.
- Vibration Dampening:The encapsulation materials possess inherent vibration-damping properties, essential for applications where machinery or equipment might experience vibrations during operation. To ensure optimal functionality of the components, preventing microfractures and loose connections is necessary.
- Impact Resistance:Components subjected to mechanical shocks, impacts, or drops are susceptible to failure. The potting and encapsulation process creates a cushioning effect, distributing and absorbing the force of results across the protective layer, reducing the risk of damage.
- Sealing Against Environmental Factors: Potting and encapsulation offer an airtight seal that protects components from moisture, dust, chemicals, and other contaminants that could degrade performance over time. This sealing also prevents the formation of condensation, which can lead to short circuits or corrosion.
- Thermal Insulation:Encapsulation materials can provide a degree of thermal insulation, shielding components from extreme temperature fluctuations. This stability is crucial in applications where parts might be exposed to high or low temperatures, ensuring stable operation.
- Customization and Form Factor:You can tailor potting and encapsulation to fit specific form factors and design requirements. The materials can be molded into various shapes, sizes, and configurations, efficiently integrating complex systems.
Waterproofing and Moisture Resistance
Waterproofing and moisture resistance are crucial aspects of potting and encapsulation processes in various industries. These processes involve enclosing electronic components or devices within protective barriers to safeguard them from environmental factors, particularly moisture, which can lead to corrosion, electrical failures, and reduced performance. Ensuring effective waterproofing and moisture resistance is essential for maintaining the longevity and reliability of sensitive equipment.
Importance of Waterproofing and Moisture Resistance
- Preventing Corrosion:Moisture can lead to corrosion of metal components, affecting their functionality and lifespan.
- Electrical Insulation:Water and moisture can cause short circuits and leakage currents, compromising electronics performance.
- Chemical Protection:Encapsulation shields components from exposure to chemicals and contaminants present in the environment.
Methods and Materials
- Encapsulation: Involves completely encasing the electronic component in a protective material, often using resins or potting compounds.
- Potting Compounds:These are dense materials poured or injected around components and then hardened to create a protective barrier.
- Conformal Coatings:These thin protective coatings are applied directly to the surface of components, providing a layer of protection against moisture and other environmental factors.
Factors Affecting Waterproofing
- Material Selection:Choosing a suitable potting compound or encapsulation material is crucial for effective moisture resistance.
- Curing Process:Proper encapsulant curing ensures that it forms a solid and impenetrable barrier.
- Sealing:It’s vital to seal all entry points for moisture adequately.
- Temperature Extremes:Components may expand and contract due to temperature changes, potentially creating vulnerabilities in the encapsulation.
Testing and Quality Control
- IP Rating:Ingress Protection rating indicates the level of protection a casing or enclosure provides against dust and water.
- Accelerated Aging Tests:We are simulating harsh environmental conditions to assess the long-term effectiveness of waterproofing.
- Visual Inspection: Regular examination for signs of degradation or moisture ingress.
- Electrical Testing: Checking for insulation resistance and leakage currents to ensure no moisture-related electrical issues.
Applications
- Electronics Industry:Waterproofing is essential for consumer electronics, industrial automation, and automotive electronics.
- Renewable Energy:Solar panels, wind turbines, and battery systems require robust moisture protection.
- Medical Devices:Waterproofing is critical for the longevity and accuracy of medical equipment.
Chemical and Corrosion Protection
Chemical exposure and corrosion pose significant threats to the longevity and functionality of electronic components and devices, especially those deployed in harsh environments. Engineers and manufacturers often employ potting and encapsulation techniques to mitigate these risks. These methods involve using protective materials to coat or encase sensitive components, providing a barrier against chemicals, moisture, and corrosive agents.
Potting: A Protective Enclosure
Potting is a process that entails encasing electronic components in a protective compound, typically a resin or silicone-based material. This method offers several advantages:
- Physical Protection:Potting creates a robust physical barrier that shields components from material impact, dust, and debris.
- Chemical Resistance:The chosen potting material can resist various chemicals, including acids, bases, solvents, and oils, safeguarding electronics from chemical deterioration.
- Moisture Barrier:Potting materials are often water-resistant, preventing moisture ingress that could lead to short circuits or corrosion.
Encapsulation: Safeguarding with Coatings
Encapsulation involves applying a protective coating directly onto the electronic components, safeguarding them from chemical exposure and corrosion:
- Thin-Film Coatings:Thin films of conformal coatings, such as perylene or acrylics, are applied to components, forming a protective layer that conforms to their shape.
- Chemical Resistance:These coatings exhibit excellent resistance to various chemicals and environmental stresses, preventing contact between the component and harmful substances.
- Flexibility and Reliability:The conformal nature of these coatings allows for flexibility and expansion/contraction of components due to temperature fluctuations without compromising protection.
Choosing the Right Approach
Selecting between potting and encapsulation depends on the specific requirements of the application:
- Complexity:Potting is ideal for complex assemblies, as it fully encases the entire assembly.
- Accessibility:Encapsulation is more suitable when particular components need to remain accessible for maintenance or testing.
- Heat Dissipation:Encapsulation is advantageous if components generate significant heat, as it allows better heat dissipation than potting.
- Space Constraints:Potting may be preferred when space constraints are not a concern, as it offers more comprehensive protection.
Potting and Encapsulation in Automotive Electronics
Potting and encapsulation play crucial roles in ensuring the durability, reliability, and performance of electronic components in the automotive industry. These processes involve applying protective materials around sensitive electronics to shield them from harsh environmental conditions, mechanical stresses, and chemical exposures.
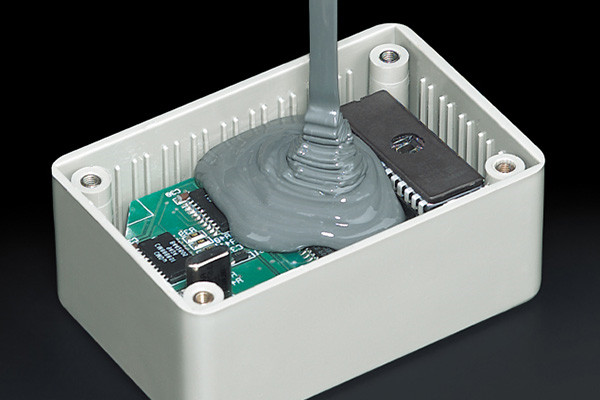
Importance of Potting and Encapsulation in Automotive Electronics
- Environmental Protection:Moisture, dust, vibrations, and temperature fluctuations subject automotive electronics to various environmental factors. Potting and encapsulation create a barrier that safeguards components against these elements.
- Vibration Damping:The constant vibrations experienced in vehicles can lead to mechanical failures and solder joint fractures. Potting and encapsulation materials absorb these vibrations, reducing the risk of damage.
Potting and Encapsulation Materials
- Epoxy Resins: Widely used for their excellent adhesion, chemical resistance, and mechanical strength. They provide a hard protective shell.
- Silicone Rubber: Known for flexibility and thermal stability. It’s suitable for components that require movement or expansion.
- Polyurethane Resins:Balancing flexibility and rigidity, making them suitable for components with varying stress levels.
- Parylene Coating:A thin, conformal polymer coating that offers excellent moisture and chemical resistance without adding bulk.
Application Process
- Preparation:Clean and dry the components thoroughly to ensure proper adhesion of the potting material.
- Mixing:Depending on the material, mix the potting compound following manufacturer guidelines to achieve the desired consistency and curing properties.
- Pouring or Injection:Carefully pour or inject the potting material, ensuring it fills all voids and covers the components uniformly.
- Curing:Allow the material to cure according to specifications. Components may face exposure to heat, moisture, or UV rays.
- Testing:Perform quality checks to ensure proper encapsulation, air bubbles’ absence, and components’ adhesion.
Challenges and Considerations
- Thermal Management:Excessive heat generated by components can affect the potting material and lead to thermal stress. Proper material selection and design are crucial.
- Repair and Rework:Components become challenging to repair or replace once encapsulated. Careful planning is necessary to avoid costly mistakes.
- Material Compatibility:Different components and potting materials may not be compatible. Compatibility tests are necessary to prevent chemical reactions.
Aerospace Applications: Ensuring Reliability
In the aerospace industry, ensuring the reliability of electronic components and systems’ reliability is paramount due to the critical nature of these applications. Potting and encapsulation techniques have emerged as crucial methods to enhance the reliability of electronics in aerospace environments. These techniques involve enclosing sensitive components in protective materials to shield them from harsh conditions such as extreme temperatures, vibrations, moisture, and mechanical stresses.
Benefits of Potting and Encapsulation
- Environmental Protection:Potting and encapsulation provide a barrier against environmental factors, including moisture, chemicals, and contaminants, which can compromise the functionality of aerospace electronics.
- Vibration Dampening:Vibrations are typical in aerospace environments, especially during takeoff, landing, and turbulent flights. Potting and encapsulation help absorb vibrations, reducing the risk of component damage or malfunction.
- Thermal Management:Aerospace systems often experience a wide range of temperatures, from cold to searing heat. Encapsulation materials with good thermal conductivity can aid in dissipating heat and maintaining stable operating temperatures.
- Mechanical Stress Resistance:Launches and landings can subject components to harsh mechanical forces. Potting materials with high mechanical strength can protect members from structural damage.
Challenges and Considerations
- Material Selection:Choosing the appropriate potting or encapsulation material is crucial. To ensure compatibility with the components and the environment, you must consider thermal expansion coefficients, chemical resistance, and adhesion properties.
- Space Constraints:Aerospace electronics are often tightly packed. Designing potting or encapsulation solutions that don’t add excessive bulk while providing adequate protection is challenging.
- Maintenance and Repairs:In the event of maintenance or repairs, the potting or encapsulation material must be removable without causing damage to the components. One must carefully consider the properties of the material and the techniques used for its removal.
Cutting-Edge Solutions
- Nanoencapsulation: Utilizing nanotechnology to create ultra-thin layers of protective materials, enhancing protection without adding significant weight or volume.
- Conformal Coatings:Thin, protective coatings closely follow the contours of components, providing a barrier against moisture and contaminants while maintaining the original form factor.
- Innovative Encapsulation:Integrating sensors within the encapsulation material to monitor temperature, humidity, and stress. With this feature, you can monitor real-time performance and predict maintenance needs.
Medical Devices: Safety and Longevity
Ensuring the safety and longevity of medical devices is paramount in the healthcare industry. Potting and encapsulation techniques are pivotal in achieving these goals by providing a protective barrier for sensitive components and enhancing the device’s overall durability. These methods involve encapsulating electronic components, sensors, and circuitry within specialized materials to safeguard them against environmental factors, mechanical stress, and potential contamination. Several key points underscore the significance of potting and encapsulation in medical devices:
- Environmental Protection:Potting and encapsulation protect medical devices from moisture, chemicals, and other external factors that could compromise their functionality. Such protection is essential for machines in various environments, including hospitals, clinics, and homes.
- Mechanical Resilience:Potting and encapsulation fortify the physical integrity of medical devices. Safeguarding against physical shocks, vibrations, and impacts is essential in healthcare settings, as these are common occurrences.
- Biocompatibility:Medical devices often come into direct contact with the human body. “We carefully choose potting and encapsulation materials to ensure biocompatibility, minimizing the risk of adverse reactions or complications when implanting or using the device on patients.
- Electrical Isolation:Potting and encapsulation help to prevent electrical components from short-circuiting due to moisture or other contaminants, ensuring consistent and accurate device performance.
- Longevity and Reliability:By preventing components from degradation caused by environmental stressors, potting, and encapsulation contribute to the longevity and reliability of medical devices. This aspect is particularly crucial for devices intended for extended implantation periods within the body.
- Regulatory Compliance:Many medical devices must adhere to strict regulatory standards to ensure patient safety. Proper potting and encapsulation can facilitate compliance with these regulations by maintaining the device’s integrity throughout its lifecycle.
Consumer Electronics and Potting Solutions
Consumer electronics have become integral to modern life, from smartphones and wearables to home appliances and entertainment systems. As these devices advance and become more compact, they face various environmental stresses such as moisture, temperature fluctuations, and physical impacts. Potting solutions have emerged as a crucial technology to address these challenges and ensure the longevity and reliability of consumer electronics. Potting, or encapsulation, involves enclosing electronic components in protective materials, typically resins or polymers, to safeguard them from external factors. This process offers several benefits:
- Environmental Protection:Potting materials create a barrier that shields sensitive components from moisture, dust, and other contaminants. This consideration is significant for devices used in outdoor or harsh environments.
- Vibration and Shock Resistance:During transportation, usage, and accidental drops, consumer electronics frequently experience vibrations and shocks. Potting materials absorb these impacts, preventing damage to delicate components.
- Thermal Management:Some potting compounds have excellent thermal conductivity properties, allowing them to dissipate heat generated by electronic components. These actions enhance the overall performance of the device and prevent overheating.
- Electrical Insulation:Potting solutions provide electrical insulation, preventing short circuits and ensuring the safe operation of the device.
- Increased Reliability:By eliminating exposure to external factors that could cause malfunctions, potting solutions contribute to the long-term reliability of consumer electronics, reducing maintenance and replacement costs.
- Miniaturization and Design Flexibility:Potting compounds are adaptable to various shapes and sizes, enabling manufacturers to create sleek, compact designs without compromising protection.
- Customization:We can tailor potting solutions to meet specific requirements, like achieving optical clarity for displays or obtaining particular levels of flexibility for wearable devices.
- Waterproofing:Many potting materials offer waterproofing capabilities, allowing devices like smartphones and fitness trackers to withstand immersion in water.
- Chemical Resistance:In environments where consumer electronics might encounter chemicals or corrosive substances, potting solutions can provide an additional layer of defense.
As consumer electronics continue to evolve and push technological boundaries, the role of potting solutions in enhancing their durability and reliability becomes increasingly crucial. Manufacturers must consider not only the functional aspects of their products but also their ability to withstand real-world conditions. From extending the lifespan of intelligent appliances to ensuring the performance of portable gadgets, potting solutions play a behind-the-scenes yet indispensable role in shaping the consumer electronics landscape.
Renewable Energy Systems and Environmental Challenges
Renewable Energy Systems are pivotal in mitigating environmental challenges associated with traditional energy sources. Within this context, potting and encapsulation techniques emerge as crucial solutions, ensuring various components’ durability, efficiency, and safety in renewable energy systems. This approach involves encasing sensitive electronic components and connections in protective materials, shielding them from harsh environmental conditions and enhancing their overall performance. Several key points highlight the significance of potting and encapsulation in the realm of renewable energy and environmental sustainability:
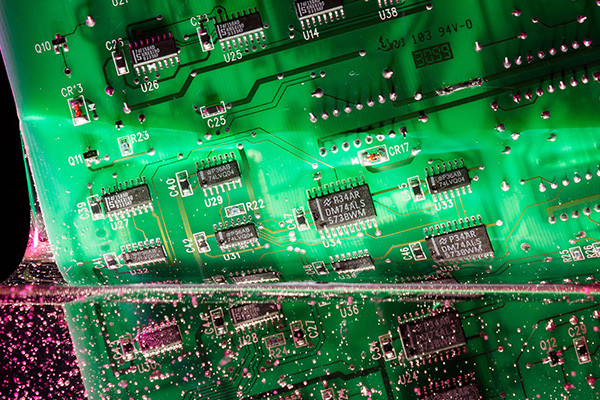
- Component Protection:Renewable energy systems encompass diverse components such as solar inverters, wind turbine controllers, and energy storage devices. Extreme temperatures, moisture, and other environmental stressors expose these components. Potting and encapsulation shield them from these conditions, prolonging their lifespan and reducing the need for frequent replacements.
- Increased Reliability:By safeguarding components from external factors, potting, and encapsulation techniques enhance the overall reliability of renewable energy systems. Increased reliability translates to higher system efficiency and reduced downtime, ensuring consistent energy production.
- Harsh Environmental Conditions:Renewable energy installations are often in challenging environments, such as offshore wind farms or desert solar arrays. Potting and encapsulation materials act as barriers against saltwater corrosion, sand abrasion, and UV radiation, preserving the functionality of critical components in these conditions.
- Maintenance Minimization:Using potting and encapsulation reduces the vulnerability of components to wear and tear, limiting the need for frequent maintenance. This approach not only lowers operational costs but also minimizes the environmental impact of maintenance activities.
- Safety Enhancement:Potting and encapsulation provide a layer of electrical insulation, protecting the components and personnel from potential electrical hazards. This safety aspect is crucial in renewable energy systems that involve high-voltage members.
- Material Selection:Potting and encapsulation materials are essential to ensure compatibility with the specific application and environmental conditions. We can choose biodegradable and environmentally friendly materials to align with sustainability goals.
- Long-Term Sustainability:Integrating potting and encapsulation techniques into renewable energy systems aligns with achieving long-term sustainability. By preserving the functionality of components, these methods reduce electronic waste and contribute to the overall reduction of environmental impact.
Challenges of Potting Large-Scale Industrial Equipment
Potting and encapsulation techniques, while advantageous for safeguarding components in various applications, present unique challenges when applied to large-scale industrial equipment. The complexities associated with such equipment demand careful consideration of these challenges:
Scale and Volume
- Large-scale industrial equipment involves bulky components and intricate systems, making the potting process more complicated and time-consuming.
- Managing the volume of potting materials becomes challenging, requiring efficient handling and distribution techniques.
Thermal Management
- Managing heat dissipation becomes more demanding due to the increased size and power of components within large equipment.
- Ensuring uniform temperature distribution throughout the potted components is crucial for optimal operation.
Material Selection
- Choosing appropriate potting materials that can cover large surfaces without compromising performance becomes critical.
- The selected materials must accommodate thermal expansion and contraction over a larger area.
Accessibility and Repairs
- Potted components are harder to access for repairs or replacements, especially in large equipment with complex layouts.
- Maintenance procedures become more intricate, potentially increasing downtime.
Curing and Processing
- Achieving consistent curing across the entirety of significant potted components is challenging.
- Longer curing times can impede production schedules, affecting overall efficiency.
Weight and Balance
- Potting compounds’ added weight can impact the equipment’s overall weight and balance, potentially affecting performance and safety.
Quality Control
- Ensuring uniform potting quality across large equipment requires meticulous quality control measures.
- Detecting defects or air pockets becomes more challenging due to the size and complexity of the potted areas.
Cost Considerations
- Large-scale equipment demands a significant amount of potting materials, increasing material costs.
- Additional labor and time required for potting can impact the overall production cost.
Environmental Impact
- Disposing potting materials on a larger scale can have environmental implications, especially when using non-biodegradable materials.
Integration with Existing Infrastructure
- Retrofitting large equipment with potting solutions can be complex, requiring careful integration to maintain existing operations.
In addressing these challenges, manufacturers of large-scale industrial equipment need to collaborate closely with material experts and consider advanced techniques such as automated potting systems, optimized material formulations, and advanced curing methods. Balancing the benefits of potting – such as protection from harsh environments, extended equipment life, and reduced maintenance – with the challenges associated with scale is essential for ensuring the reliability and sustainability of industrial operations.
Future Prospects of Potting and Encapsulation Technologies
Potting and encapsulation technologies are poised to play an increasingly vital role across various industries as advancements unfold. The evolving landscape presents several exciting prospects that are poised to shape the future of these techniques:
Material Innovations
- Continued development of novel potting materials will cater to more specific application requirements, including enhanced durability, flexibility, and biodegradability.
- Integrating intelligent materials capable of self-healing and adaptive properties will revolutionize component protection.
Miniaturization and Microelectronics
- As electronics continue to shrink, potting techniques will adapt to suit the needs of smaller, densely packed components.
- Microencapsulation may become essential for protecting sensitive microelectronics in diverse applications, from medical devices to Internet of Things (IoT) sensors.
Advanced Application Areas
- Potting and encapsulation will find new horizons in emerging fields like quantum computing, where ultra-sensitive components require pristine protection from external interference.
- High-speed communication systems, such as 5G and beyond, will demand advanced potting solutions to ensure optimal performance under diverse conditions.
Nanotechnology Integration
- We will integrate nanomaterials into potting compounds to enhance thermal conductivity, electrical insulation, and mechanical strength.
- Nanoscale encapsulation techniques will contribute to the protection of nanoelectronic devices and advanced materials.
Automation and Industry 4.0
- Integrating automation and robotics will streamline potting processes, reducing human error and increasing efficiency.
- Industry 4.0 principles will enable real-time monitoring of potted components’ performance and condition, leading to predictive maintenance strategies.
Sustainability Focus
- Increasing environmental consciousness will drive the development of eco-friendly potting materials that can be easily recycled or biodegraded.
- Sustainable potting techniques will align with global efforts to reduce electronic waste and minimize environmental impact.
Multi-Material Solutions
- Combining different materials with complementary properties, hybrid potting approaches will gain traction to address multifaceted protection needs.
- Multi-material encapsulation will become essential for complex applications like renewable energy systems and electric vehicles.
Customization and Personalization
- Advances in additive manufacturing (3D printing) will enable customized potting solutions tailored to specific components and applications.
- Personalized encapsulation methods will optimize performance and protection, minimizing material waste.
Global Integration
- We will integrate potting and encapsulation technologies into global initiatives for sustainable infrastructure development, renewable energy expansion, and healthcare solutions advancement.
Potting and encapsulation have undoubtedly become cornerstones of modern engineering, playing a pivotal role in ensuring the longevity, reliability, and resilience of a vast array of electronic components and products. As technology continues to evolve and industries advance, the demand for enhanced protection against environmental factors grows ever more significant. Whether it’s safeguarding automotive electronics, critical medical devices, or renewable energy systems, the application of potting and encapsulation techniques offers an indispensable solution. By understanding the various materials available, the distinctions between potting and encapsulation, and the unique challenges posed by different industries, engineers and manufacturers can continue to innovate and refine these methods, thus driving the advancement of technology into the future.