Low Outgassing Adhesive
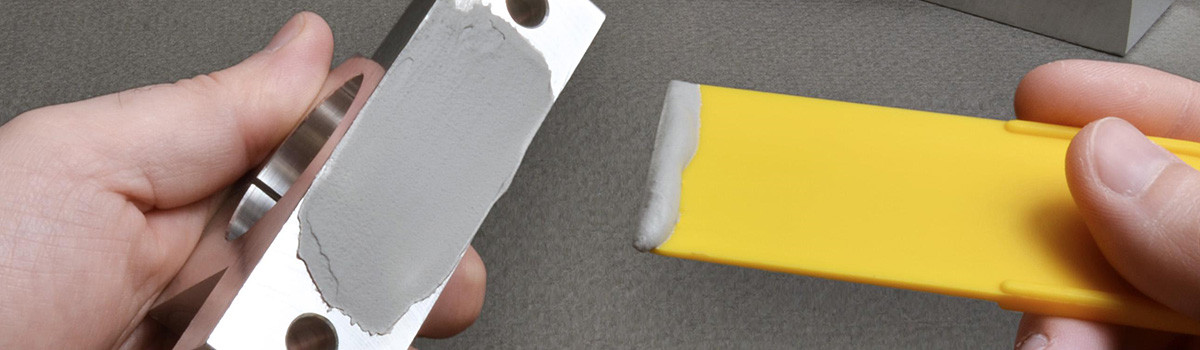
In the realm of aerospace, vacuum technology, and specialized manufacturing, maintaining a pristine environment free from contaminants is crucial. Low outgassing adhesive, a remarkable innovation, has emerged as a solution to the challenges posed by outgassing in vacuum environments. With its ability to minimize the release of volatile compounds under vacuum conditions, low outgassing adhesive has become indispensable in applications where cleanliness, reliability, and longevity are paramount. This comprehensive article delves into the world of low outgassing adhesive, exploring its mechanisms, applications, advantages, and its pivotal role in advancing industries that operate beyond our atmospheric confines.
Unraveling Low Outgassing Adhesive
Low outgassing adhesives have emerged as critical components in various advanced applications, from aerospace to electronics, where minimal volatile compound release is imperative to ensure long-term performance and reliability. These adhesives find utility in vacuum environments, clean rooms, and enclosed spaces, where outgassed substances could compromise the integrity of sensitive equipment or optics.
Significance in Space Exploration
Low outgassing adhesives are instrumental in space exploration, where materials experiencing extreme conditions require their attributes. The vacuum and temperature fluctuations of outer space can cause traditional adhesives to release gases, contaminating optical systems and sensors. Adhesives with low outgassing characteristics mitigate this risk, ensuring the clarity and precision of scientific instruments.
Electronics and Optics Manufacturing
Miniaturization has amplified the importance of low outgassing adhesives within the electronics and optics manufacturing sectors. As components pack more densely, the potential for outgassed materials to affect nearby elements escalates. Low outgassing adhesives prevent contamination and sustain the functionality of delicate electronic components over extended lifecycles.
Balancing Performance and Outgassing
While the primary goal is minimizing outgassing, engineers and scientists must maintain adhesive performance. Striking the right balance between these two factors poses an ongoing challenge. Adhesive manufacturers continually refine formulations to reduce outgassing while upholding key attributes such as bond strength, thermal resistance, and longevity.
Testing and Certification
Characterizing and certifying low outgassing adhesives are essential in their adoption. Standardized tests, such as the ASTM E595 test, are employed to quantify the volatile content of adhesives and establish their suitability for specific applications. These tests aid in assessing the potential impact of outgassing on surrounding materials.
Unraveling low outgassing adhesives underscores their pivotal role in cutting-edge sectors like space exploration and advanced electronics. As technology advances and demands for performance soar, the quest for adhesives with minimal outgassing continues to drive innovation. With a delicate equilibrium between performance and outgassing, these adhesives enable the seamless integration of components in environments where precision and reliability are paramount.
Understanding Outgassing Phenomenon
Outgassing refers to the process where volatile compounds, such as gases or vapors, are emitted from materials, particularly under vacuum or elevated temperature conditions. This phenomenon can occur in various materials, including polymers, adhesives, coatings, and metals. The volatiles released during outgassing can have multiple origins, including residual solvents, absorbed gases, and decomposition products from the material itself.
Factors Influencing Outgassing
Several factors influence the extent and rate of outgassing. Material composition, manufacturing processes, and environmental conditions play significant roles. Porous materials exhibit more pronounced outgassing due to the higher surface area for volatile release. Additionally, the vacuum, temperature, and exposure duration impact the degree of outgassing.
Impact on Applications
Outgassing can have significant consequences in specific applications. For instance, in sensitive environments like clean rooms, space exploration, and electronics manufacturing, outgassed materials can contaminate, affect optical clarity, degrade electronic components, or disturb the vacuum integrity. Understanding and mitigating outgassing is thus crucial to maintaining performance, reliability, and longevity.
Testing and Measurement
Various techniques are employed to quantify and characterize the outgassing phenomenon. Standard tests, like ASTM E595, involve subjecting materials to controlled vacuum and temperature conditions while measuring the released volatiles. These tests help evaluate materials’ suitability for specific applications and provide valuable data for engineers and manufacturers to make informed decisions.
Material Selection and Design
In engineering and design, awareness of outgassing tendencies informs material selection and product design. Choosing materials with low outgassing potential becomes essential in critical applications where volatile release can compromise functionality or contaminate sensitive systems. Engineers also consider strategies to mitigate outgassing, such as pre-conditioning materials to remove volatile components before deployment.
Understanding the outgassing phenomenon involves grasping its underlying mechanisms, the factors shaping its occurrence, and the methods to quantify and manage it. This knowledge proves indispensable in fields where precise control over materials’ behavior in vacuum or high-temperature environments is crucial. By comprehending the intricacies of outgassing, engineers and researchers can make strides toward enhancing the reliability and performance of products across various industries.
The Vacuum Environment Challenge
Navigating the vacuum environment challenge demands innovative solutions due to the extreme conditions it presents. In space exploration and scientific research, vacuum environments lack the air molecules in Earth’s atmosphere, creating a unique set of hurdles for materials, equipment, and human presence.
Pressure Differential Impact: Stress on Materials and Systems
The absence of air pressure in a vacuum environment stresses materials and systems designed for Earth’s atmospheric conditions. Structural integrity, thermal management, and material outgassing become pronounced as components may expand, contract, or release volatile compounds in response to vacuum-induced changes.
Thermal Extremes: Drastic Temperature Swings
Vacuum environments expose materials to dramatic temperature fluctuations. Direct exposure to the Sun’s radiation can cause surfaces to become extremely hot while facing away from the Sun can lead to rapid cooling. Engineering materials that can withstand these rapid and extreme temperature changes are pivotal for mission success.
Impact on Electronics and Materials: Ionizing Radiation and Outgassing
Electronics face the dual challenge of ionizing radiation and outgassing in vacuum environments. Ionizing radiation can interfere with electronic components and compromise functionality, necessitating specialized shielding. Additionally, outgassing from materials can contaminate sensitive equipment, affecting optics, sensors, and experiments.
Astronaut Safety and Life Support: Ensuring Habitability
Ensuring astronaut safety and life support in a vacuum environment for crewed missions requires meticulous planning. Developing robust life support systems that provide breathable air, temperature regulation, and waste management becomes imperative to sustain human presence beyond Earth’s atmosphere.
Technological Advancements: Enabling Breakthrough Discoveries
Despite the challenges, vacuum environments also offer opportunities for breakthrough discoveries. The absence of atmospheric interference allows for unparalleled observations and measurements in fields like astronomy and astrophysics, enabling researchers to glean insights into the cosmos that are impossible to obtain from Earth.
Composition and Formulation
Creating successful products hinges on precise ingredient selection. Engineers and chemists must carefully choose components that fulfill specific performance criteria: durability, adhesion, flexibility, or resistance to environmental factors.
Balancing Act: Optimizing Properties through Proportioning
Formulation involves a delicate balance of ingredients to achieve desired properties. Adjusting the proportions of constituents can fine-tune characteristics such as viscosity, hardness, and thermal stability, ensuring the final product meets the intended specifications.
Synergistic Effects: Harnessing Ingredient Interactions
Innovative formulations often capitalize on synergistic effects, where the interaction between ingredients enhances overall performance. Compatibility studies and material testing are essential to uncover these synergies and unlock new avenues for product improvement.
Addressing Environmental Impact: Sustainability in Formulation
Modern formulations take sustainability into account. Engineers seek eco-friendly alternatives, biodegradable components, and reduced use of hazardous substances to minimize the environmental impact of products throughout their lifecycles.
Stability and Shelf Life: Ensuring Longevity and Consistency
Formulations need to maintain stability over time. Thorough testing for chemical reactions, phase separation, and degradation under various conditions is imperative to ensure the product’s shelf life and consistent performance.
Iterative Process: Testing, Refining, and Innovation
The iterative formulation process involves continuous testing, refinement, and innovation. Real-time application feedback informs adjustments, enhancing products that align with evolving industry demands.
The composition and formulation of products stand as the cornerstone of their functionality, reliability, and impact. Meticulous ingredient selection, synergistic interactions, and sustainability considerations collectively shape products that excel in various applications, from consumer goods to cutting-edge technologies.
Types of Low Outgassing Adhesives
Low outgassing adhesives are essential for aerospace, electronics, and optics applications, where the release of volatile compounds can lead to contamination or performance degradation. Designers have formulated these adhesives to minimize the release of gases and vapors that could potentially harm sensitive components or surfaces. There are several types of low outgassing adhesives available to cater to different needs:
1.Silicone-Based Adhesives:Silicone adhesives are known for their flexibility, high-temperature resistance, and low outgassing properties. They are suitable for bonding materials with disparate coefficients of thermal expansion.
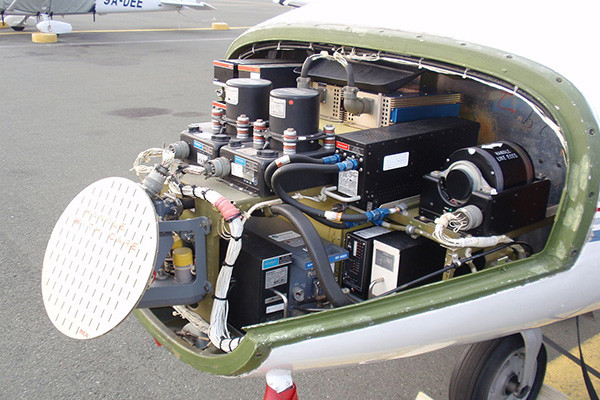
2.Epoxy-Based Adhesives:Epoxy adhesives offer excellent bonding strength and durability. Advanced formulations minimize outgassing, making them suitable for demanding applications.
3.Urethane-Based Adhesives:Experts choose urethane adhesives for their flexibility and resistance to impact. Low outgassing urethane adhesives find utility in situations where shock absorption is crucial.
4.Cyanoacrylate (Super Glue) Adhesivescure quickly and exhibit low outgassing characteristics. People commonly use them in situations that require rapid bonding.
5.Acrylic-Based Adhesives:Acrylic adhesives combine good adhesion with low outgassing properties. People often use them in optical and display-related applications.
6.Film Adhesives:Manufacturers offer film adhesives in various chemistries, and users can apply them in sheet form. They are beneficial in large-area bonding applications.
Choosing the suitable low outgassing adhesive depends on substrate materials, operating conditions, and performance requirements. It’s crucial to carefully evaluate the adhesive properties to ensure successful and contamination-free bonding in sensitive environments.
Spacecraft and Satellite Applications
Spacecraft and satellites have revolutionized our understanding of the universe and our ability to communicate and observe Earth. These advanced technological marvels serve many purposes, each demanding specific capabilities to ensure mission success and longevity. Key applications include:
- Earth Observation:Satellites equipped with sensors capture high-resolution images used for environmental monitoring, disaster management, urban planning, and agriculture.
- Communication:Communication satellites form the backbone of global telecommunications, enabling worldwide voice, data, and internet connectivity.
- Navigation:Satellite navigation systems like GPS enable accurate positioning, navigation, and timing crucial for aviation, maritime, and ground-based applications.
- Scientific Research:Spacecraft like rovers, orbiters, and telescopes provide invaluable data for studying celestial bodies, planetary composition, atmospheres, and cosmic phenomena.
- Weather Forecasting:Weather satellites monitor atmospheric conditions, track storms, and provide critical data for weather forecasting and climate research.
- Space Exploration:Probes and landers travel to other planets, moons, and asteroids to gather data about their composition, geology, and potential habitability.
- Space Situational Awareness:Satellites contribute to tracking space debris and monitoring potential collisions to safeguard operational spacecraft.
- Technology Testing:New technologies are tested in space, offering insights into their performance under extreme conditions, leading to advancements in various fields.
- National Security:Military satellites aid in reconnaissance, surveillance, and secure communication, ensuring national security interests.
- Education and Outreach:Satellites engage the public in space exploration, inspiring the next generation of scientists, engineers, and enthusiasts.
However, spacecraft and satellite applications come with unique challenges:
- Harsh Environment:Space presents extreme temperatures, vacuum, radiation, and micrometeoroid threats, requiring robust materials and shielding.
- Orbital Debris:The increasing space debris poses collision risks to operational satellites and requires mitigation strategies.
- Longevity:Ensuring a satellite’s operational life through efficient power generation, propulsion systems, and redundancy is vital.
- Data Management:Handling the vast amounts of data transmitted by satellites demands sophisticated processing and storage systems.
- Cost Constraints:Developing, launching, and maintaining satellites can be expensive; cost-effective solutions are crucial.
As technology advances, spacecraft and satellites continue to push boundaries, fostering scientific discovery, enhancing communication, and driving innovation on a global scale.
Aerospace Instrumentation
Aerospace Instrumentation plays a pivotal role in the modern aviation and space exploration industry, providing crucial data collection and analysis for safe and efficient operations. This field combines advanced technology with precision engineering to create sophisticated instruments that monitor, measure, and communicate essential parameters during flight and space missions. Key aspects of Aerospace Instrumentation include:
- Flight Data Monitoring (FDM):Aerospace instruments collect real-time data such as altitude, airspeed, temperature, and pressure. This data aids in monitoring the health and performance of aircraft and spacecraft systems, enabling timely maintenance and adjustments.
- Navigation Systems:Aerospace instrumentation includes navigation tools like Inertial Measurement Units (IMUs) and Global Navigation Satellite Systems (GNSS) receivers. These ensure accurate positioning, trajectory calculation, and guidance for aerospace vehicles.
- Sensors and Actuators:Aerospace sensors detect changes in the environment and system conditions, providing critical flight control and automation inputs. Actuators respond to these inputs by adjusting surfaces, engines, and other components, contributing to stability and maneuverability.
- Structural Health Monitoring:Researchers utilize instruments to monitor the structural integrity of aerospace vehicles, identifying stress, fatigue, and damage. By avoiding catastrophic breakdowns, this approach assists in making informed decisions regarding maintenance.
- Telemetry and Communication:Aerospace instrumentation establishes communication links between vehicles and ground stations, transmitting data and receiving commands. Telemetry systems relay essential information during launch, flight, and re-entry.
- Remote Sensing and Earth Observation:Spaceborne instruments capture data from Earth, helping scientists study climate, natural disasters, and land use. These instruments provide valuable insights into our planet’s health and change over time.
- Space Science Instruments:Aerospace instrumentation enables scientific exploration beyond Earth. Telescopes, spectrometers, and other specialized sensors gather data about celestial bodies, contributing to our understanding of the universe.
- Material Testing:Aerospace instrumentation is employed to test the durability and performance of materials under extreme conditions, simulating the stress and temperature variations experienced in aerospace environments.
Semiconductor Fabrication
Semiconductor Fabrication lies at the heart of modern electronics, encompassing the intricate process of creating semiconductor devices that power everything from smartphones to computers to advanced medical equipment. This complex and precise field involves a sequence of steps to produce integrated circuits (ICs) with nanoscale features. Key components of Semiconductor Fabrication include:
- Wafer Preparation:The process begins with slicing a single crystal silicon ingot into thin wafers. These wafers serve as the base for multiple ICs.
- Photolithography:A crucial step, photolithography uses light to transfer intricate circuit patterns onto the wafer’s surface. Photoresist materials and masks are employed to create the desired designs.
- Etching and Patterning:Etching removes unwanted material from the wafer to create the circuit’s patterns. Chemical etching, plasma etching, and reactive ion etching shape the features precisely.
- Implantation:Dopants are introduced into specific areas of the silicon wafer through ion implantation, altering its electrical properties to create transistors and other components.
- Deposition:Thin layers of various materials are deposited onto the wafer using chemical vapor deposition (CVD) or physical vapor deposition (PVD) techniques. These layers form the circuits and insulating elements.
- Oxidation:Oxide layers are grown on the wafer’s surface to insulate and protect components, forming the gate dielectrics of transistors.
- Annealing:High-temperature treatments help to activate dopants, diffuse them into the silicon, and repair any damage caused during previous processing steps.
- Chemical Mechanical Polishing (CMP):CMP planarizes the wafer’s surface by removing excess material and ensuring uniformity, which is critical for multi-layer structures.
- Lithography Alignment:Multiple lithography steps are often required to create intricate circuits. Precise alignment between different layers ensures proper functionality.
- Testing and Packaging:Each wafer undergoes testing to identify defects and ensure functionality after fabrication. Chips are then separated, packaged, and connected to external pins for integration into electronic devices.
Semiconductor Fabrication demands a fusion of physics, chemistry, engineering, and nanotechnology. The industry’s rapid progress, characterized by Moore’s Law, continually pushes the limits of miniaturization and performance. As researchers shrink transistor sizes and explore new materials, they continue to make Semiconductor Fabrication integral to shaping the technology landscape. This process drives innovation in areas ranging from computing to artificial intelligence to the Internet of Things.
Optics and Precision Instruments
Optics and Precision Instruments constitute a multidisciplinary field that harnesses light and precise engineering to create devices that manipulate and measure light for various applications. This field’s advancements have revolutionized multiple industries, from telecommunications to healthcare to astronomy. Key components and aspects of Optics and Precision Instruments include:
1.Lenses and Mirrors:Precision-crafted lenses and mirrors are fundamental for focusing, magnifying, and steering light. These components are essential in cameras, microscopes, telescopes, and laser systems.
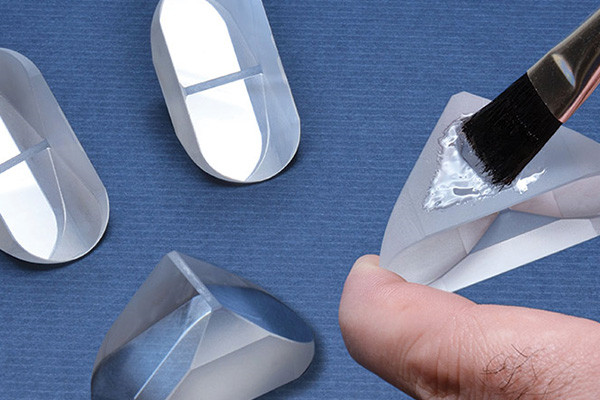
2.Lasers and Photonics:Lasers emit coherent light with various properties, finding use in applications like telecommunications, medical procedures, barcode scanning, and material processing.
3.Spectroscopy:Optical instruments analyze the interaction between light and matter. Spectrometers provide insights into chemical composition, helping scientists identify substances and study their properties.
4.Interferometry:Researchers use interference patterns of light waves to measure distances with extraordinary precision, enabling applications such as semiconductor manufacturing and gravitational wave detection.
5.Holography:Holographic techniques create three-dimensional images by recording and reconstructing light waves. Companies and institutions employ this technology in security features, art, and medical imaging.
6.Microscopy:Optical microscopy enables the visualization of tiny structures and cells. Techniques like confocal and fluorescence microscopy allow for enhanced resolution and labeling of specific systems.
7.Optical Communication:Fiber optics revolutionized data transmission by enabling high-speed, long-distance communication by efficiently propagating light signals in optical fibers.
8.Precision Metrology:Optics is crucial in accurately measuring lengths, angles, and other physical properties. In fields like manufacturing and space exploration, this is an essential factor.
9.Astronomical Instruments:Telescopes equipped with advanced optics provide astronomers with detailed views of distant celestial objects, aiding our understanding of the universe’s origins and evolution.
10.Medical Imaging:Optical imaging methods, such as endoscopy and optical coherence tomography (OCT), allow non-invasive visualization of internal body structures and aid in diagnostics.
11.Photolithography:Optical techniques are used in semiconductor manufacturing to create intricate patterns on microchips, enabling the development of smaller and more powerful electronic devices.
Optics and Precision Instruments continue to evolve with materials, fabrication techniques, and computational algorithms advancements. This interdisciplinary field merges physics, engineering, and materials science to create devices that shape the modern world, enabling technological progress across various applications.
Medical Equipment in Sterile Environments
Medical Equipment in Sterile Environments stands as a critical component of healthcare settings, ensuring the safety of patients by preventing infections and maintaining stringent hygiene standards. Such environments, including operating rooms, intensive care units, and sterile laboratories, demand specialized medical equipment that adheres to strict protocols. Key considerations and aspects of Medical Equipment in Sterile Environments include:
- Surgical Instruments:Precise and sterilizable surgical instruments are essential for performing procedures in sterile environments. Scalpels, forceps, retractors, and scissors are crafted to be easily sterilized and have minimal areas where contaminants can accumulate.
- Sterilization Techniques:Medical equipment must undergo thorough sterilization procedures, often using autoclaving, ethylene oxide gas sterilization, or hydrogen peroxide vapor. These techniques eliminate harmful microorganisms and ensure the instruments are safe for patient use.
- Disposable vs. Reusable:Some equipment is designed for single-use, reducing the risk of cross-contamination. Others are built to be durable and can withstand multiple sterilization cycles.
- Personal Protective Equipment (PPE):Healthcare professionals working in sterile environments wear specialized PPE, including sterile gowns, gloves, masks, and face shields, to prevent the introduction of contaminants.
- Infection Control Measures:Designers create medical equipment with features that facilitate easy cleaning and disinfection. Smooth surfaces, minimal joints, and removable parts aid in thorough decontamination.
- Imaging and Monitoring Equipment:Integrating equipment such as X-ray machines, MRI scanners, and patient monitors into sterile environments without compromising functionality is necessary. Protective barriers and strict cleaning protocols are employed to maintain sterility.
- Environmental Controls:Sterile environments have controlled airflow, temperature, and humidity to minimize the presence of airborne contaminants. Equipment design considers these factors to prevent the introduction of particles.
- Remote Control and Automation:In some cases, remote control and automation of medical equipment reduce the need for direct contact, maintaining sterility and minimizing infection risk.
- Quality Control and Maintenance:Rigorous quality control checks ensure that medical equipment functions properly and maintains sterility. Technicians conduct regular maintenance to prevent equipment malfunction and contamination.
- Emergency Situations:In sterile environments, emergency medical equipment such as defibrillators, suction devices, and emergency carts must be readily available and sterile-packaged for immediate use.
Material Compatibility and Adhesion Strength
Material Compatibility and Adhesion Strength are crucial factors in various industries, including manufacturing, construction, and healthcare, where the interaction between different materials and their ability to bond securely can significantly impact product performance and durability. Key considerations and aspects of Material Compatibility and Adhesion Strength include:
- Material Selection:Choosing materials with compatible properties is essential to ensure strong and durable bonds. Factors such as chemical composition, thermal expansion coefficients, and mechanical properties play a role in determining compatibility.
- Surface Preparation:Properly preparing the surfaces to be bonded is critical for achieving strong adhesion. Surface cleaning, roughening, and treatments like priming or etching improve bonding effectiveness.
- Adhesive Selection:Selecting the suitable adhesive or bonding agent for the materials in question is crucial. Different adhesives, such as epoxies, acrylics, or cyanoacrylates, offer varying levels of adhesion strength and compatibility with specific materials.
- Environmental Conditions:Consideration of the operating environment is essential. Factors like temperature fluctuations, humidity, chemical exposure, and UV radiation can impact adhesion strength and material compatibility.
- Adhesion Testing:Various tests, including peel tests, shear tests, and lap shear tests, evaluate the adhesion strength between materials. These tests help determine if the bond is strong enough for the intended application.
- Mechanical Interlocking:Creating automatic interlocking features, such as rough textures or interlocking shapes, can enhance adhesion strength by providing additional surface area for bonding.
- Interfacial Bonding:Achieving a solid bond at the molecular level is crucial. Adhesive molecules interacting with the material’s surface molecules enhance adhesion.
- Thermal Expansion Compatibility:Materials with similar coefficients of thermal expansion are less likely to experience bond failure due to temperature changes as they expand and contract at similar rates.
- Long-Term Durability:Understanding the potential effects of aging, exposure to environmental factors, and cyclic loading is essential to ensure the longevity of the bonded materials.
- Biocompatibility:In the medical field, ensuring that materials used for implants and medical devices are biocompatible and exhibit strong adhesion to biological tissues is vital for patient safety.
Thermal and Mechanical Stability
Thermal and Mechanical Stability are critical attributes that influence the performance and reliability of materials, components, and systems across diverse industries. These factors determine how well a material or structure can withstand changes in temperature, mechanical forces, and other environmental stresses. Key considerations and aspects of Thermal and Mechanical Stability include:
- Temperature Range:Materials with high thermal stability can withstand extreme temperature fluctuations without undergoing significant changes in their properties. Understanding a material’s thermal expansion behavior is crucial to prevent structural failures.
- Thermal Conductivity:In applications where heat dissipation is essential, materials with high thermal conductivity ensure efficient heat transfer and prevent overheating.
- Thermal Expansion Coefficient:Matching the thermal expansion coefficients of materials in a system minimizes stress and prevents delamination or cracking due to temperature changes.
- Creep Resistance:Materials with good mechanical stability exhibit minimal deformation under prolonged mechanical stress, preventing structural failure over time.
- Fatigue Resistance:The ability to withstand repeated mechanical loading cycles without degradation is crucial in applications involving dynamic stresses, such as aerospace components and machinery.
- Strength and Toughness:High mechanical stability requires a balance between strength (resistance to deformation) and toughness (ability to absorb energy before fracturing), ensuring a material can withstand various mechanical loads.
- Elastic Modulus:The material’s elastic modulus determines how much it deforms under mechanical stress. Materials with higher moduli maintain their shape more effectively.
- Brittle vs. Ductile Behavior: Understanding a material’s response to stress is vital. Brittle materials fracture abruptly, while ductile materials deform plastically before failure.
- Wear Resistance:Mechanical stability often relates to a material’s ability to resist wear and abrasion, which is critical in applications involving sliding or rubbing contact.
- Corrosion Resistance:Corrosion can compromise both thermal and mechanical stability. Materials resistant to environmental factors such as moisture, chemicals, and oxidation maintain their integrity over time.
- Dimensional Stability:Materials with high mechanical stability maintain their dimensions under different conditions, ensuring precision and accuracy in applications like metrology and manufacturing.
Thermal and Mechanical Stability is integral in designing materials and structures that endure harsh operating conditions, ensuring product longevity, safety, and optimal performance. A comprehensive understanding of these factors enables engineers and scientists to make informed decisions across industries, from automotive and construction to electronics and energy.
Testing and Certification Standards
Testing and Certification Standards ensure the quality, safety, and reliability of products, systems, and services across diverse industries. These standards provide a common framework for evaluating compliance with established specifications, regulations, and performance expectations. Key considerations and aspects of Testing and Certification Standards include:
- Standard Development Organizations:Internationally recognized bodies such as ISO (International Organization for Standardization), ASTM International, and IEC (International Electrotechnical Commission) develop and maintain standards across various sectors, including manufacturing, healthcare, and technology.
- Safety and Reliability:Standards define criteria for product safety, reliability, and performance, ensuring that products meet minimum requirements for user and environmental protection.
- Testing Protocols:Standards outline specific testing procedures and methodologies to assess a product’s characteristics, functionality, and performance under various conditions.
- Material Compatibility:Standards often address material properties, ensuring that components used in products are compatible and won’t compromise the product’s overall performance.
- Interoperability:In industries like information technology, standards ensure that products from different manufacturers can work seamlessly together, promoting compatibility and avoiding vendor lock-in.
- Certification Process:Organizations may seek certification to validate that their products or processes adhere to established standards. Third-party certification bodies conduct audits, inspections, and testing to verify compliance.
- Market Access:Compliance with recognized standards is a prerequisite for entering specific markets or industries. Products with appropriate certifications may avoid barriers to market entry.
- Consumer Confidence:Products bearing certification marks instill confidence in consumers, ensuring that the product meets established quality and safety criteria.
- Environmental Sustainability:Standards increasingly address eco-friendly practices, promoting energy efficiency, reduced waste, and environmentally responsible production methods.
- Medical and Healthcare:In the medical field, standards ensure that devices and procedures adhere to established clinical and safety guidelines, safeguarding patient well-being.
- Aerospace and Automotive:These industries rely on stringent standards to ensure the safety, reliability, and performance of components used in critical applications.
- Continuous Improvement:Standards are regularly updated to incorporate new technologies, best practices, and emerging safety concerns, reflecting the ongoing evolution of industries.
Testing and Certification Standards are vital in upholding consumer trust, product quality, and safety across sectors. They enable consistency, interoperability, and adherence to best practices, contributing to technological advancements and enhancing the overall quality of products and services.
Mitigating Contaminant Buildup
Mitigating Contaminant Buildup is essential across industries to ensure product quality, operational efficiency, and health and safety. Key strategies involve a combination of preventative measures, regular maintenance, and advanced technologies:
- Design Optimization:Creating systems and products with smooth surfaces and minimal crevices reduces areas for contaminants to accumulate.
- Adequate Ventilation: Proper ventilation and air filtration systems help remove airborne particles and maintain a cleaner environment.
- Cleaning Protocols:Implementing regular and thorough cleaning procedures prevents the buildup of dirt and pollutants.
- Material Selection:To minimize the potential for contamination retention, one can choose resistant, non-porous materials.
- Controlled Environments:Establishing controlled zones with restricted access limits the introduction of contaminants.
- Monitoring and Automation:Using sensors and automated systems detects contamination events and reduces human intervention.
- Regular Inspections:Periodic assessments identify contamination sources and maintenance needs.
- Hygiene Practices:Educating personnel about contamination risks and proper hygiene habits enhances cleanliness.
- Sterilization Techniques:Employing sterilization and disinfection methods prevents the spread of pathogens.
- Collaboration and Research:Partnering with experts and staying updated on industry advancements helps develop effective mitigation strategies.
Mitigating contaminant buildup requires a comprehensive approach that combines various tactics to ensure a clean and safe environment, safeguarding product integrity and overall well-being.
Application Techniques in Cleanrooms
Application Techniques in Cleanrooms are crucial for maintaining the stringent cleanliness standards required in semiconductor manufacturing, pharmaceuticals, and biotechnology industries. These controlled environments demand specialized methods to ensure products and processes remain contaminant-free. Key strategies and aspects of application techniques in cleanrooms include:
1.Gowning and Personal Protective Equipment (PPE):Personnel must wear appropriate cleanroom attire, including gloves, masks, and sterile garments, to prevent the introduction of particles from clothing and skin.
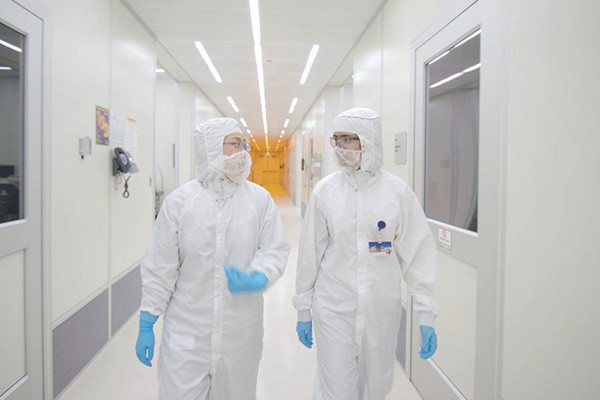
2.Surface Cleaning and Disinfection:Thorough cleaning of surfaces using lint-free wipes and approved cleaning agents helps eliminate particles and pathogens.
3.Aseptic Techniques:In pharmaceutical industries, aseptic techniques involving sterile equipment and handling procedures prevent microbial contamination during production.
4.Airflow Control:Directional airflow systems ensure that clean air continuously sweeps away contaminants and particles generated within the cleanroom.
5.Material Transfer Practices:Minimizing the movement of materials in and out of cleanrooms reduces the risk of introducing external contaminants.
6.Isolation and Containment:Isolators and containment systems maintain a barrier between personnel and processes, preventing contamination.
7.Particle Control:HEPA (High-Efficiency Particulate Air) filters capture airborne particles, maintaining a clean environment.
8.Static Control:Electrostatic discharge (ESD) protection prevents the release of particles due to electrostatic forces.
9.Validation and Monitoring:Regular monitoring of environmental conditions, such as particle counts and microbial levels, ensures ongoing compliance.
10.Training and Education:Personnel receive training on cleanroom protocols, hygiene, and proper application techniques to prevent contamination.
Cleanroom application techniques combine controlled processes, advanced technologies, and strict protocols to maintain the highest cleanliness levels. These strategies are pivotal in safeguarding product quality, enhancing research outcomes, and meeting regulatory requirements in critical industries.
Collaboration between Industries
Collaboration between industries is an increasingly vital aspect of modern innovation, as it fosters cross-pollination of ideas, expertise, and resources, driving collective progress and addressing complex challenges. Key benefits and characteristics of collaboration between industries include:
- Knowledge Sharing:Industries bring unique insights and knowledge, sharing best practices and lessons learned for mutual growth.
- Innovation Acceleration:Combining expertise from different fields often sparks innovative solutions that might have yet to be possible within a single industry’s scope.
- Resource Optimization:Collaborative efforts allow industries to pool resources, reducing costs and optimizing utilization.
- Technology Transfer:Technologies developed in one industry can find new applications in another, enhancing efficiency and opening new markets.
- Problem-Solving:Complex problems that span multiple domains can be tackled more effectively through diverse perspectives and expertise.
- Market Expansion:Collaboration enables access to new customer bases and markets, facilitating expansion beyond traditional boundaries.
- Regulatory Expertise:Sharing regulatory insights and compliance strategies helps industries navigate complex legal frameworks.
- Talent Development:Collaboration provides cross-training and skill development opportunities, nurturing a versatile workforce.
- Sustainability Initiatives:Joint efforts can address sustainability challenges by sharing sustainable practices and adopting eco-friendly technologies.
- Risk Mitigation:Collaboration can mitigate risks associated with market fluctuations as industries diversify their offerings.
Collaboration between industries requires effective communication, mutual trust, and a shared vision. As industries increasingly recognize the value of interdisciplinary cooperation, partnerships are becoming essential drivers of progress, enabling them to collectively tackle global challenges and create innovative solutions that benefit society.
Innovations in Low Outgassing Technology
Innovations in Low Outgassing Technology are pivotal in aerospace, electronics, and space exploration, where minimizing the release of volatile organic compounds (VOCs) and gases from materials is crucial to prevent contamination and ensure reliable performance in vacuum and high-vacuum environments. Key advancements and aspects of low outgassing technology include:
- Material Formulation:Developing materials with low volatile content and optimized chemical compositions reduces outgassing tendencies.
- Surface Treatments:Applying coatings or treatments to materials minimizes their outgassing potential, enhancing their suitability for critical applications.
- Testing and Validation:Advanced testing methods quantify outgassing rates and guide material selection for specific environments.
- Additive Manufacturing:Innovations in 3D printing techniques focus on developing low outgassing materials for creating intricate components.
- Adhesive and Bonding Solutions:Low outgassing adhesives and bonding agents ensure secure connections without compromising vacuum integrity.
- Venting Strategies:Designing components with integrated venting channels allows trapped gases to escape harmlessly.
- High-Performance Polymers:New polymer formulations reduce outgassing, making them viable for applications requiring exceptional mechanical properties.
- Environmental Considerations:Low outgassing materials contribute to eco-friendly practices by reducing contamination and preserving vacuum quality.
- Space Exploration:Innovations in low outgassing technology are crucial for space missions, preventing contamination of sensitive equipment and instruments.
Innovations in low outgassing technology drive advancements in sensitive environments, ensuring product integrity, performance, and safety. As industries continue to explore new frontiers and demand higher precision and reliability, low outgassing solutions play an integral role in shaping the future of technology.
Challenges and Research Frontiers
Navigating Challenges and Research Frontiers is a continuous endeavor across various disciplines, driving innovation, expanding knowledge boundaries, and addressing complex global issues. Key challenges and frontiers of research include:
- Climate Change and Sustainability:Tackling climate change, resource depletion, and environmental degradation requires interdisciplinary research to develop sustainable solutions for energy, agriculture, and infrastructure.
- Healthcare and Disease Management:Advancements in medical research aim to combat emerging diseases, enhance personalized medicine, and develop new therapies through genomic research, AI-assisted diagnostics, and precision treatments.
- Technological Ethics and Privacy:As technology evolves, ethical considerations around AI, data privacy, and autonomous systems require in-depth research to balance innovation with societal well-being.
- Renewable Energy and Energy Storage:Overcoming challenges in renewable energy adoption, energy storage technologies, and grid integration is essential for transitioning to a sustainable energy future.
- Space Exploration and Colonization:Expanding human presence in space requires research into life support systems, interplanetary travel, and sustainable habitats on other celestial bodies.
- Quantum Technologies:Exploring quantum computing, communication, and cryptography holds the potential to revolutionize computation and secure information transmission.
- Biodiversity and Ecosystem Health:Research on biodiversity conservation, ecosystem restoration, and climate resilience is vital to preserving Earth’s natural systems.
- Nanotechnology and Materials Science:Innovations in nanomaterials, drug delivery, and manufacturing techniques require research to understand their potential benefits and risks.
- Aging Population and Healthcare:Research into gerontology, elderly care, and age-related diseases is crucial to address the challenges an aging global population poses.
- Food Security and Agriculture:Advancing agricultural practices, crop yield optimization, and sustainable farming techniques are essential to feed a growing population.
- Crisis Response and Disaster Management:Developing efficient disaster response strategies and technologies is essential to mitigate the impacts of natural and human-made disasters.
Challenges and Research Frontiers demand collaborative efforts, interdisciplinary approaches, and a commitment to pushing the boundaries of human knowledge. These endeavors shape the trajectory of scientific progress, technological innovation, and societal well-being, ensuring a brighter future for future generations.
Sustainability and Environmental Impact
Sustainability and Environmental Impact are central concerns in today’s world, compelling industries and individuals to adopt practices that minimize adverse effects on the planet. Addressing these issues requires a comprehensive approach considering resource conservation, responsible consumption, and eco-friendly technologies. Key aspects and strategies related to sustainability and environmental impact include:
- Renewable Energy Adoption:Transitioning to renewable energy sources such as solar, wind, and hydroelectric power reduces greenhouse gas emissions and reliance on fossil fuels.
- Energy Efficiency:Implementing energy-efficient technologies and practices in buildings, transportation, and industrial processes minimizes energy consumption and lowers carbon footprints.
- Circular Economy:Adopting a circular approach by reusing, recycling, and upcycling materials reduces waste and conserves resources, preventing the depletion of natural reserves.
- Green Infrastructure:Developing green spaces, urban forests, and sustainable urban planning improves air quality, reduces heat islands, and enhances overall well-being.
- Water Conservation:Implementing water-efficient technologies and reducing wasteful water practices ensure the availability of clean water resources for future generations.
- Carbon Footprint Reduction:Calculating and mitigating carbon footprints through measures like carbon offsetting and sustainable transportation choices helps combat climate change.
- Sustainable Agriculture:Promoting agroecological practices, organic farming, and reducing food waste enhance food security while minimizing the environmental impact of agriculture.
- Waste Management:Implementing proper waste segregation, recycling programs, and reducing single-use plastics reduce pollution and conserve resources.
- Eco-Friendly Materials:Using sustainable and biodegradable materials in products reduces the environmental impact during production, use, and disposal.
- Biodiversity Conservation:Protecting natural habitats and wildlife preserves biodiversity, maintaining ecosystems’ health and resilience.
- Public Awareness and Education:Raising awareness about sustainability and environmental issues empowers individuals to make informed choices and advocate for positive change.
- Policy and Regulation:Governments play a crucial role in enforcing environmental regulations, incentivizing sustainable practices, and fostering innovation through policy frameworks.
Future Prospects of Low Outgassing Solutions
The prospects of Low Outgassing Solutions hold significant promise in advancing industries that require stringent contamination control, such as aerospace, electronics, and space exploration. As technology continues to evolve, key developments and trends in low outgassing solutions include:
- Materials Innovation:Ongoing research into novel materials with minimal volatile content will lead to a broader range of options for creating low outgassing components and products.
- Additive Manufacturing:Innovations in 3D printing materials will address the challenges of producing intricate and low outgassing structures for critical applications.
- Advanced Coating Technologies:Further advancements in coatings and surface treatments will enhance the ability to modify material surfaces to reduce outgassing tendencies.
- Space Exploration:Low outgassing solutions will play a pivotal role in ensuring the reliability and performance of spacecraft, satellites, and instruments, preventing contamination in the vacuum of space.
- Medical and Biotechnology:As industries demand high purity in medical devices and biotechnology applications, low outgassing solutions will become essential to prevent contamination in sensitive environments.
- Electronics and Optics:Low outgassing materials will continue to be integral in maintaining the integrity of electronic components and optics, enhancing the performance and longevity of devices.
- Environmental Considerations:Eco-friendly low outgassing solutions that reduce the release of harmful substances will align with sustainability goals and regulatory requirements.
The future of low outgassing solutions lies in interdisciplinary collaboration, material science breakthroughs, and technological innovation. As industries strive for higher precision, reliability, and efficiency, low outgassing solutions will remain vital in ensuring the integrity of products and systems in challenging environments.
Low outgassing adhesive stands as a testament to human ingenuity, addressing the intricate challenges presented by vacuum environments across a spectrum of industries. Its role in preserving the integrity of components, instruments, and devices exposed to space, cleanroom, and other vacuum applications cannot be overstated. As technology continues to push boundaries, low outgassing adhesives will be instrumental in enabling breakthroughs in scientific exploration, communications, healthcare, and beyond. With ongoing research and advancements, these specialized adhesives are poised to elevate the standards of reliability, performance, and cleanliness in environments where conventional bonding methods fall short.